Published: 01.02.2023
Creative concept and photography: Rosina Pencheva
Text: Maria Boncheva
Creative concept and photography: Rosina Pencheva
Text: Maria Boncheva
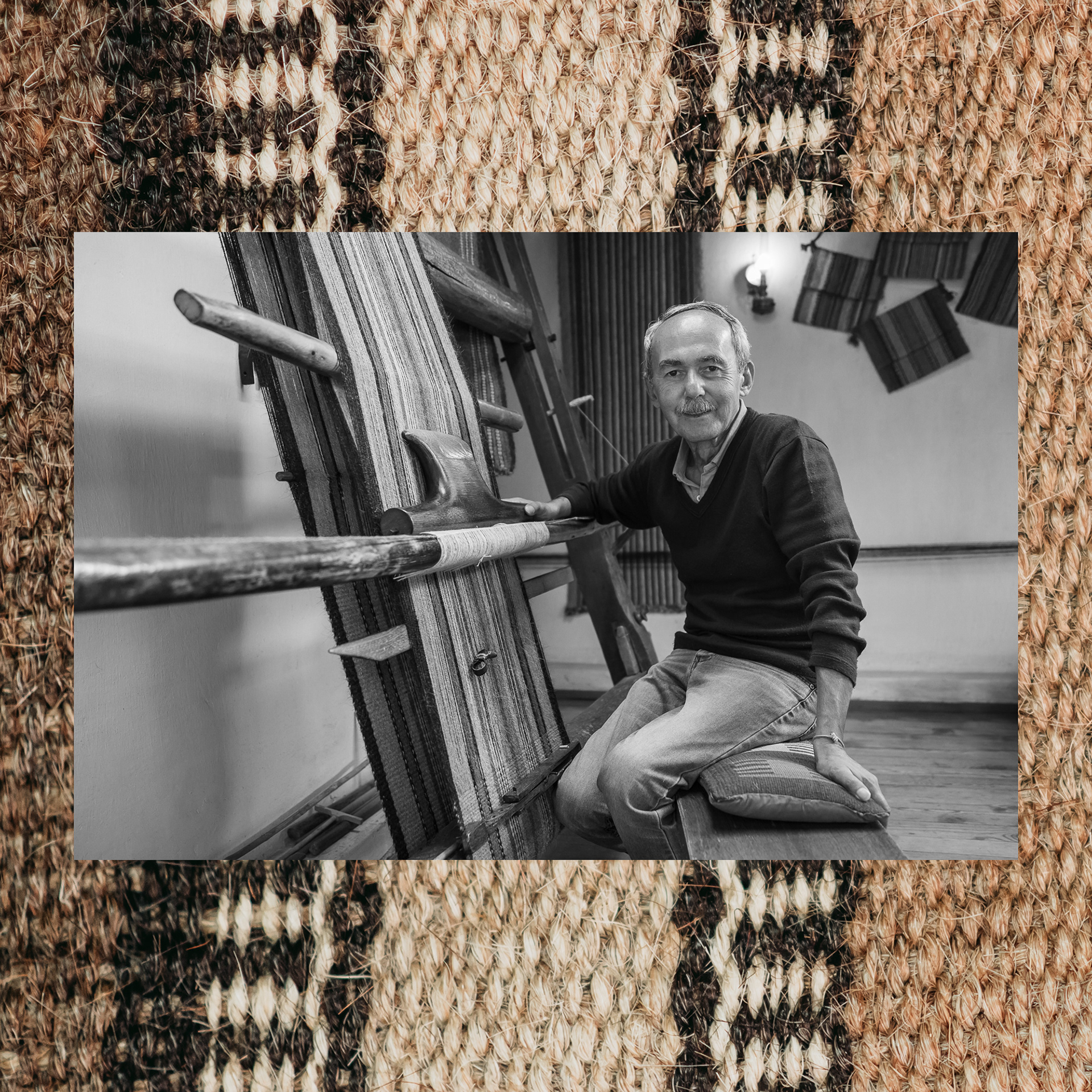
The only long-term master of the goat-hair working craft in Bulgaria.
Registered in the National System “Living Human Treasures – Bulgaria“ in the field "Knowledge and skills related to traditional crafts", 2022.
Practices the only craft in which all processes take place on the spot, at the workshop of the artisan.
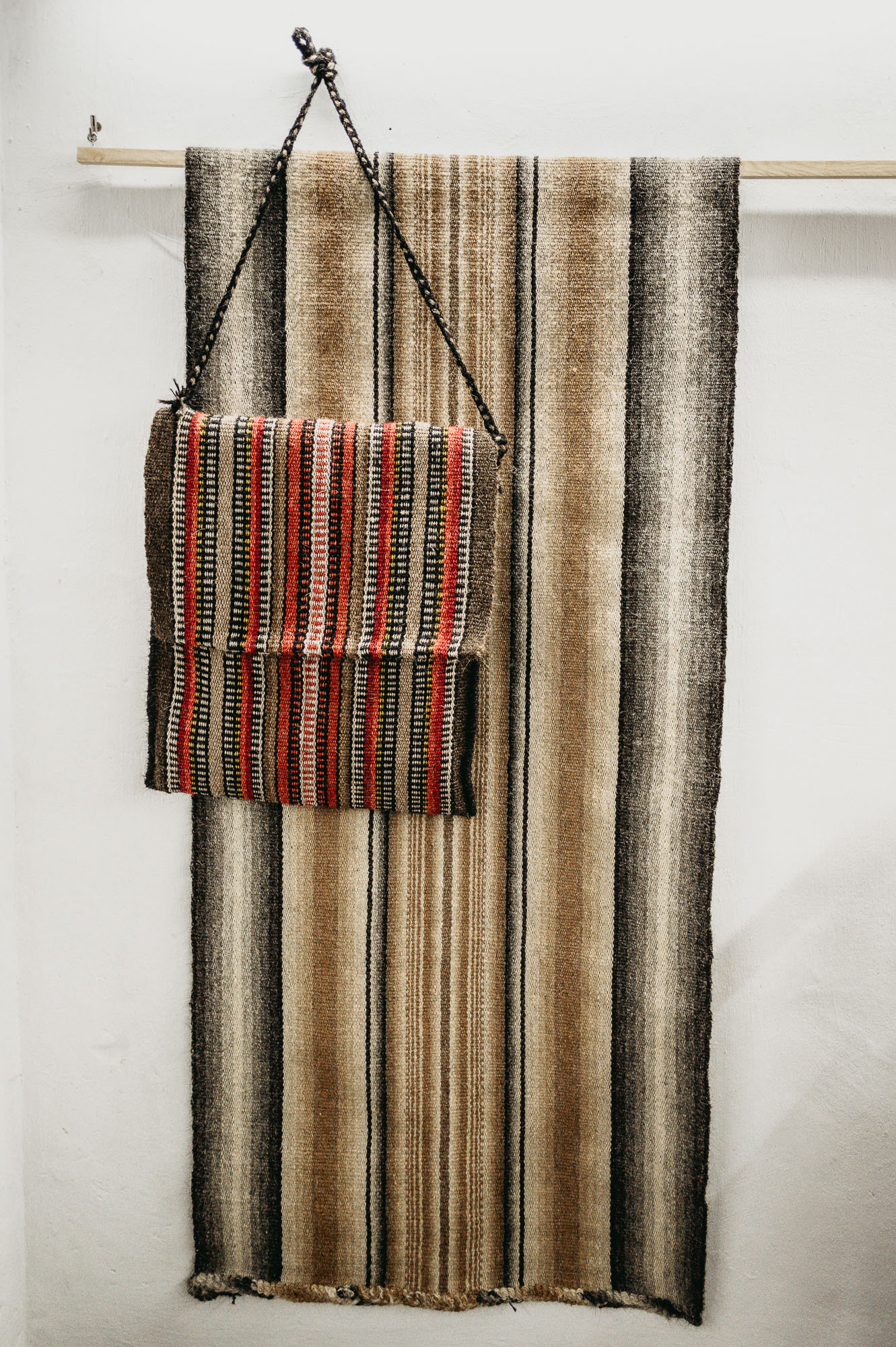
Artisan articles from goat hair by Hristo Marinov – a rug and a bag
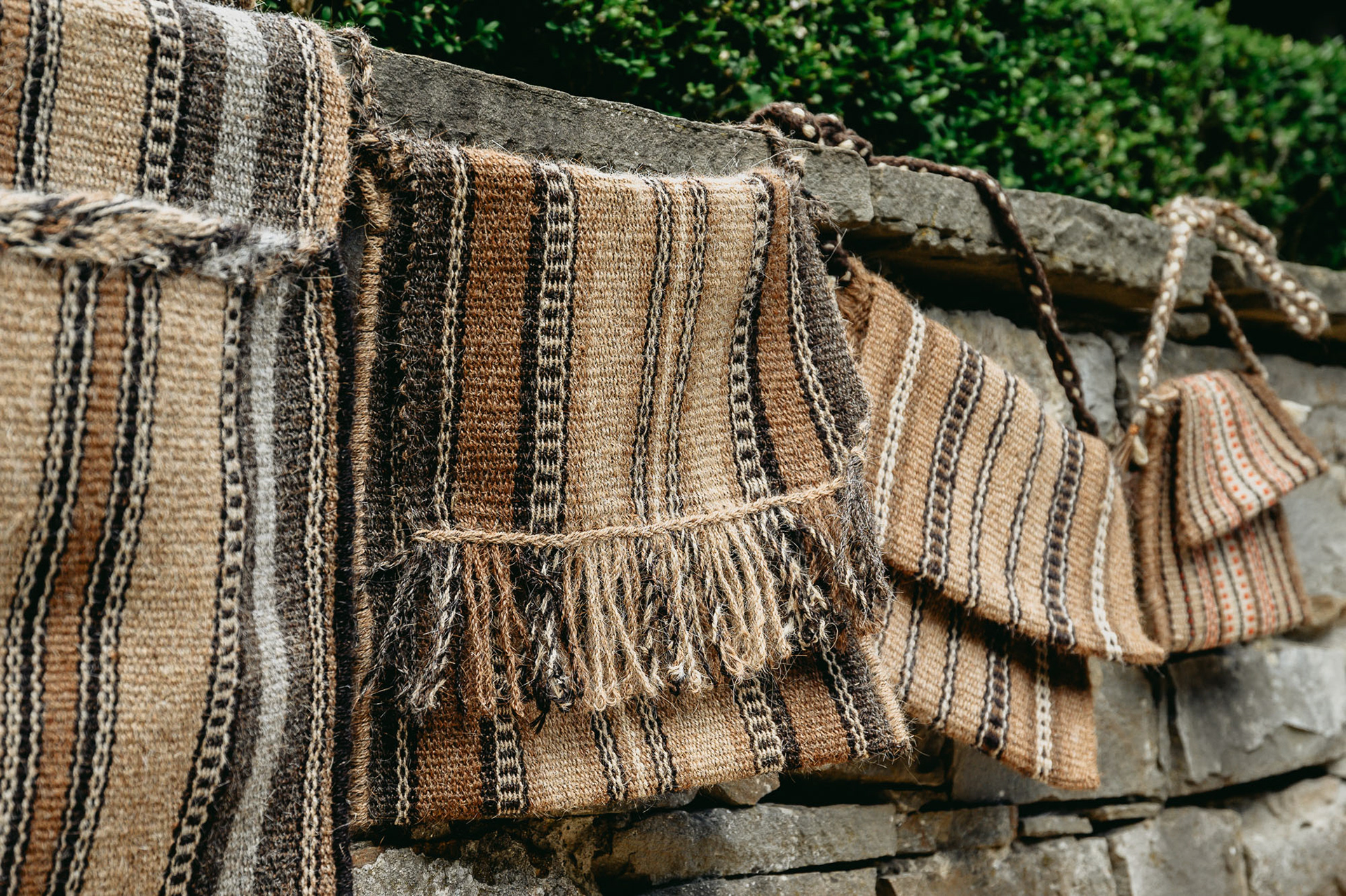
Bags in traditional Мutafchi style by Hristo Marinov
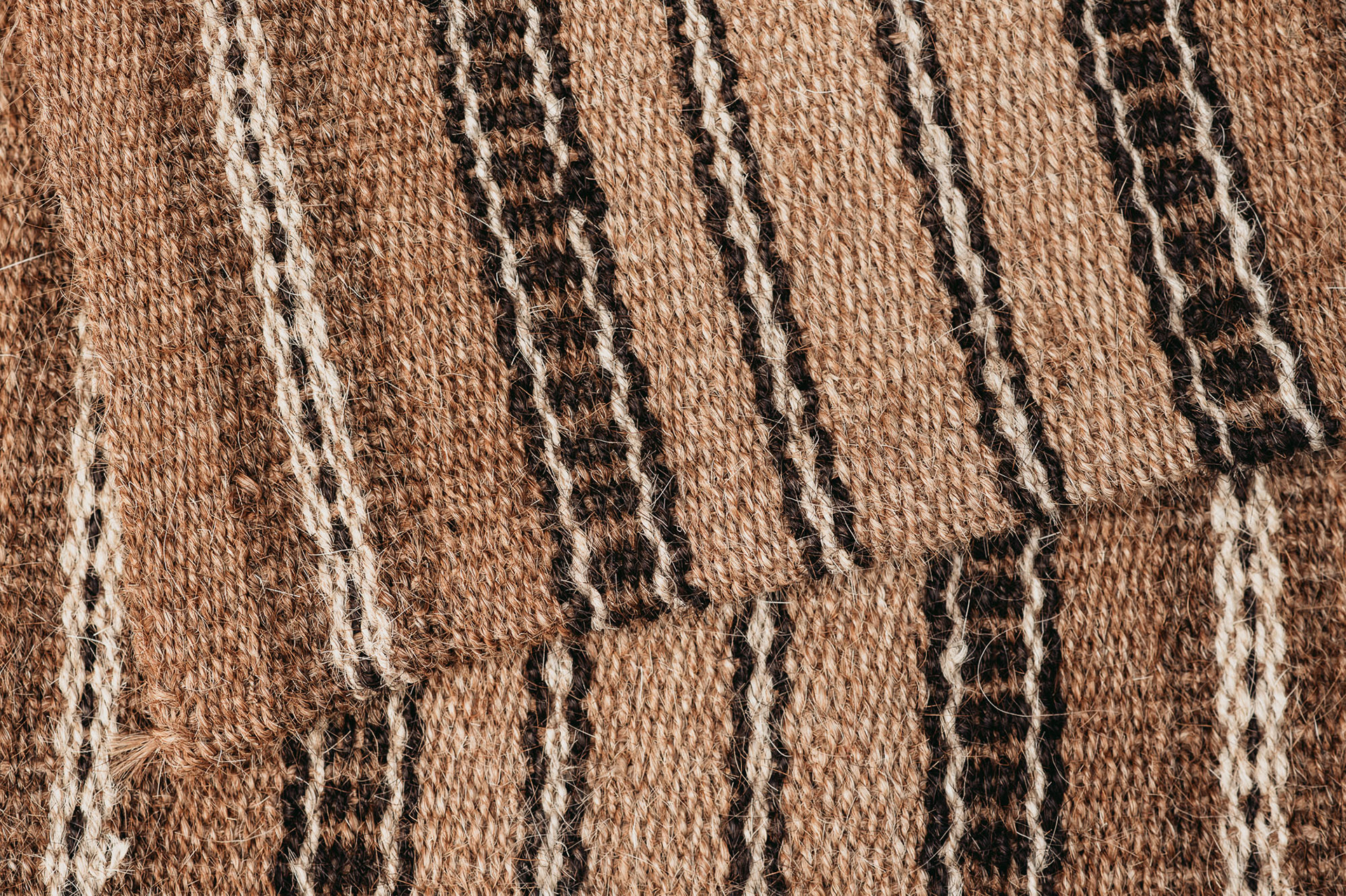
Detail of Mutafchi fabric
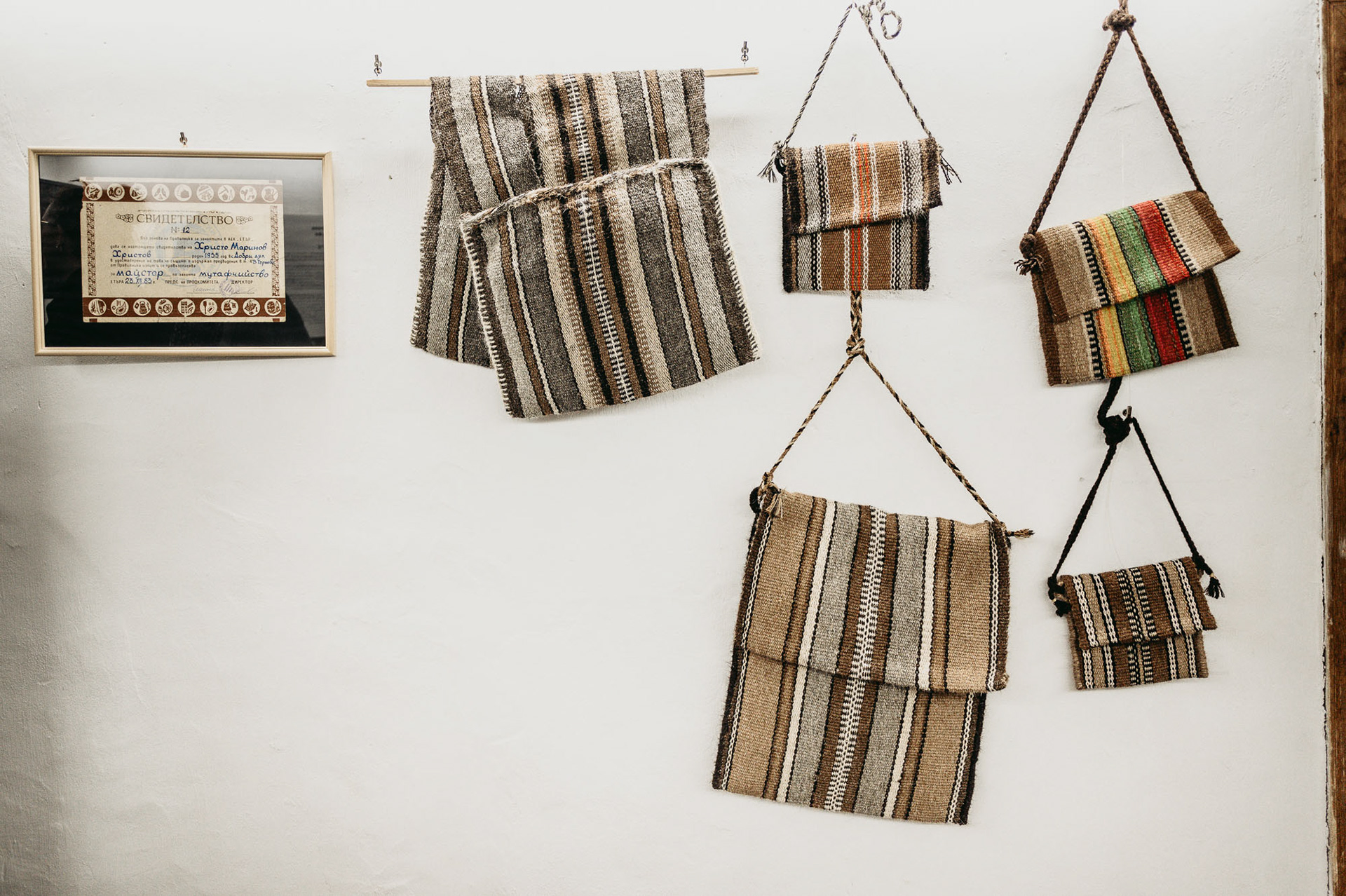
View from the retrospective exhibition "Hristo Marinov – the master creator", 2022, Etar Museum
Mutafchiistvo, sometimes also called kozinarstvo, is the craft of making various articles from goat’s hair – predominantly bags, sacks, cloths and covers, saddlebags for animals, horse harnesses and rugs. This almost extinct craft arrived in the Bulgarian lands sometime in the 17th century from Persia via the Ottoman Empire. Goat-hair working thrived during the National Revival era when numerous artisans organized in local guilds worked across the Bulgarian ethnic territory. In the mid-19th century, during the Crimean War, the trade lived through both its heyday and debacle. On the one hand, transportation of gunpowder required mass production of goat’s hair sacks boasting top quality for storage of goods – goat’s hair insulates humidity and also offers a breathing texture, durability and strength. On the other hand though, it was also the time when industrially manufactured sacks and ropes made from cheaper raw materials were introduced to the market. Goat-hair working with its slow, archaic and exclusively manual operations in processing the raw material could not resist the competition. With the subsequent changes in animal farming and the mass migration of people to cities, goat-hair working totally lost its trade worth with only few exceptions such as articles for home or tavern decoration, and rugs.
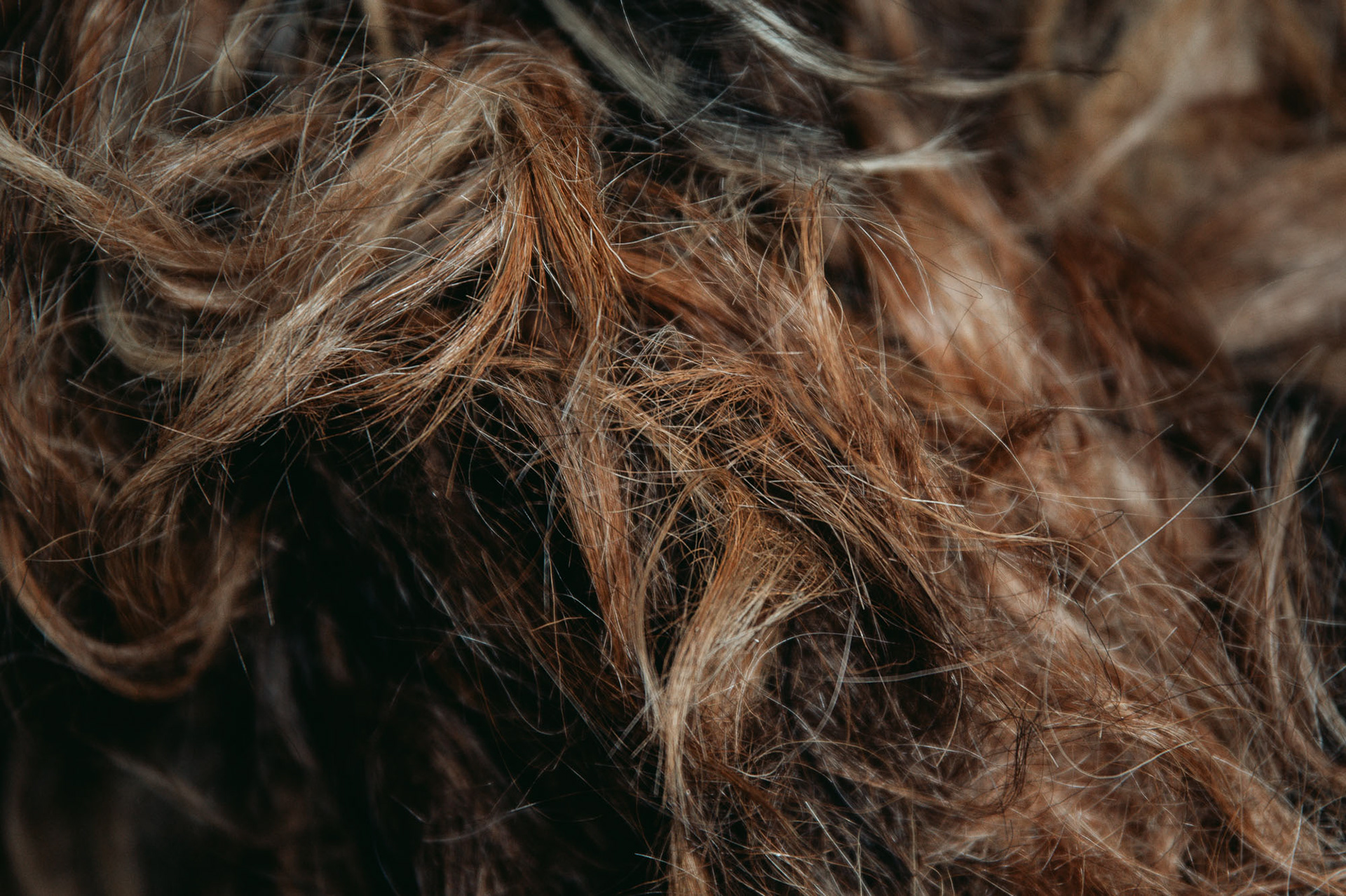
The raw material – sheared goat's hair, arrives at the master’s workshop in hard and matted state
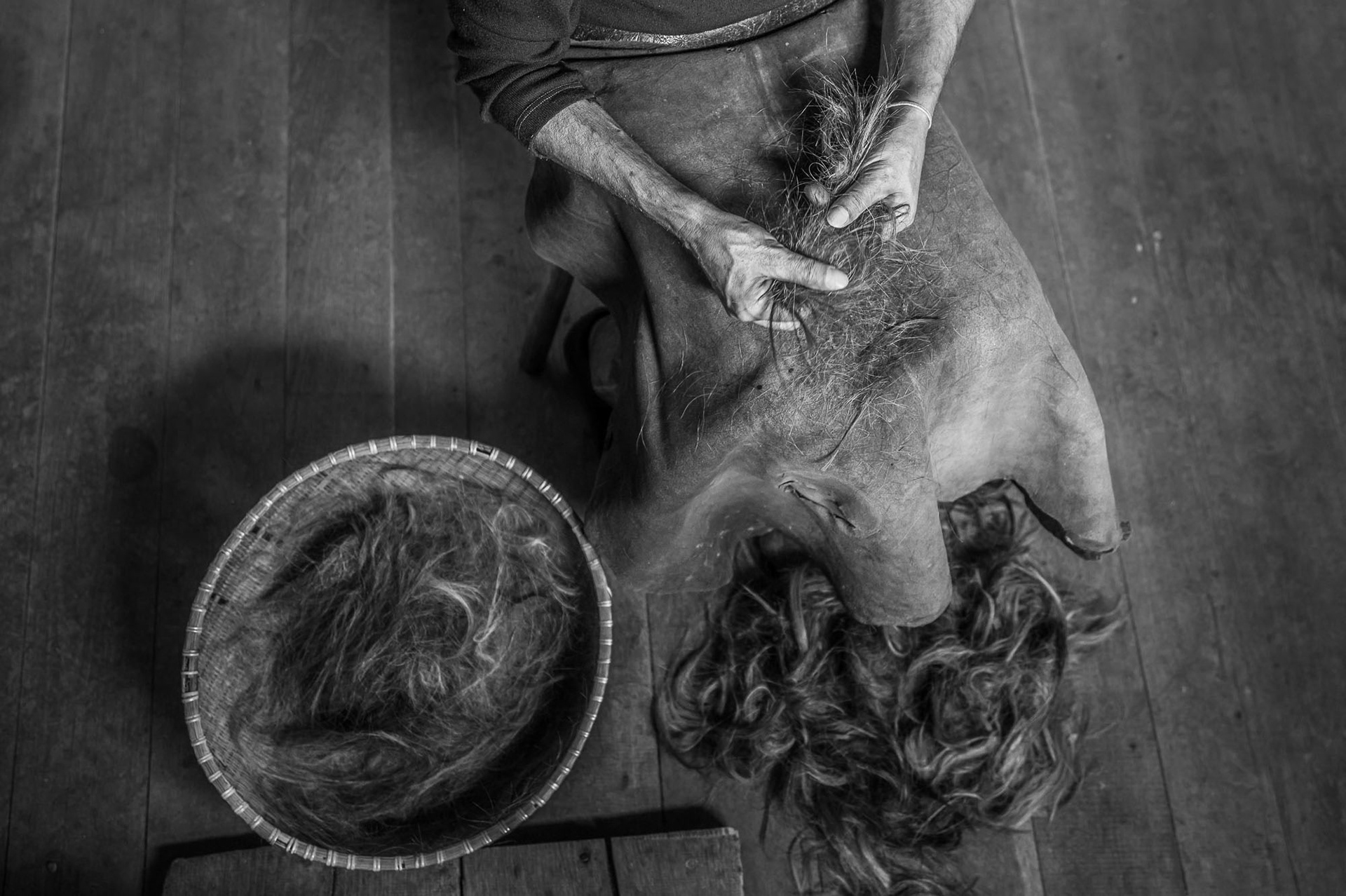
The first process in the craft is picking the hair – simultaneous cleaning and separation by color
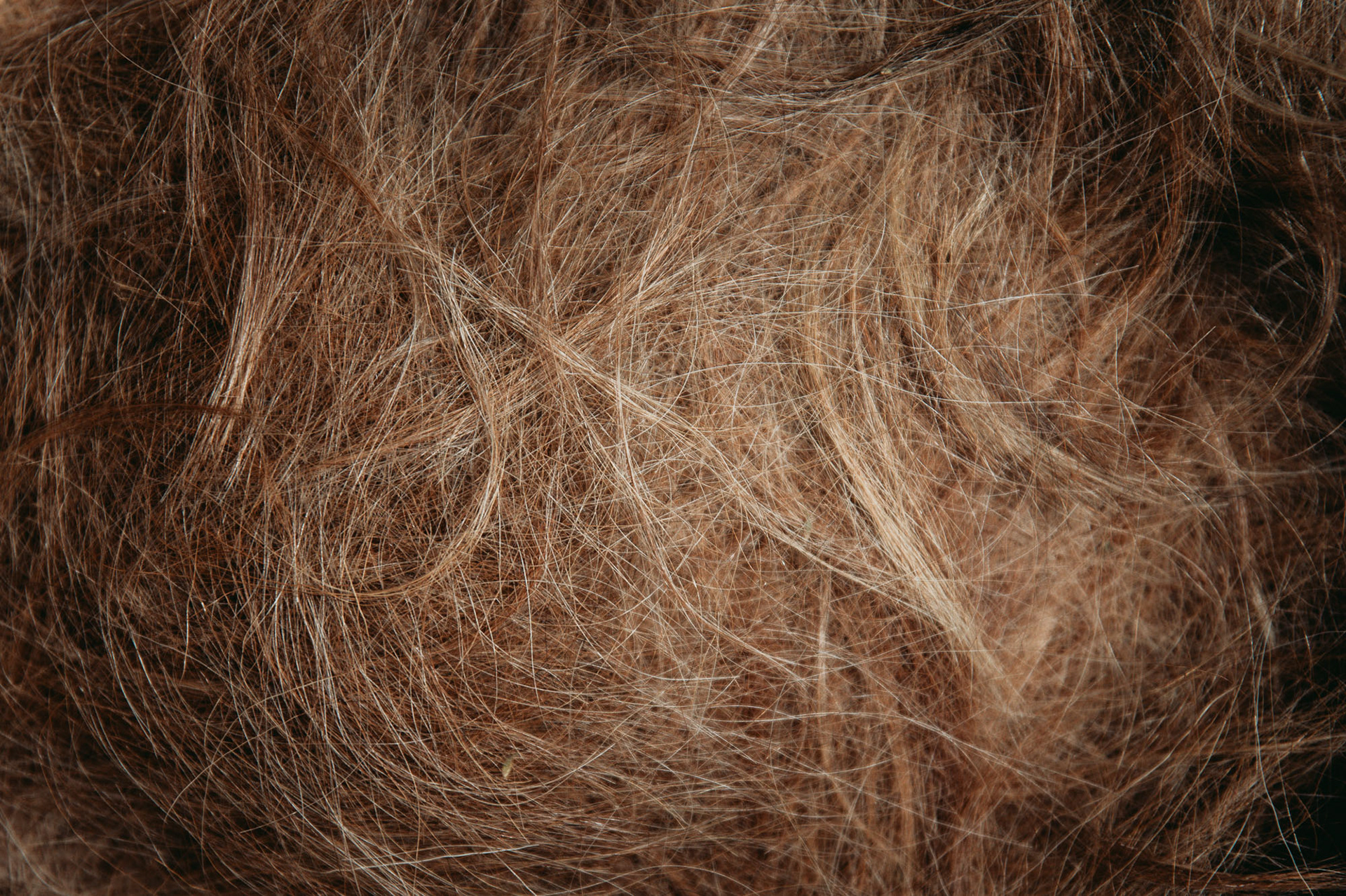
Cleaned, detangled goat hair
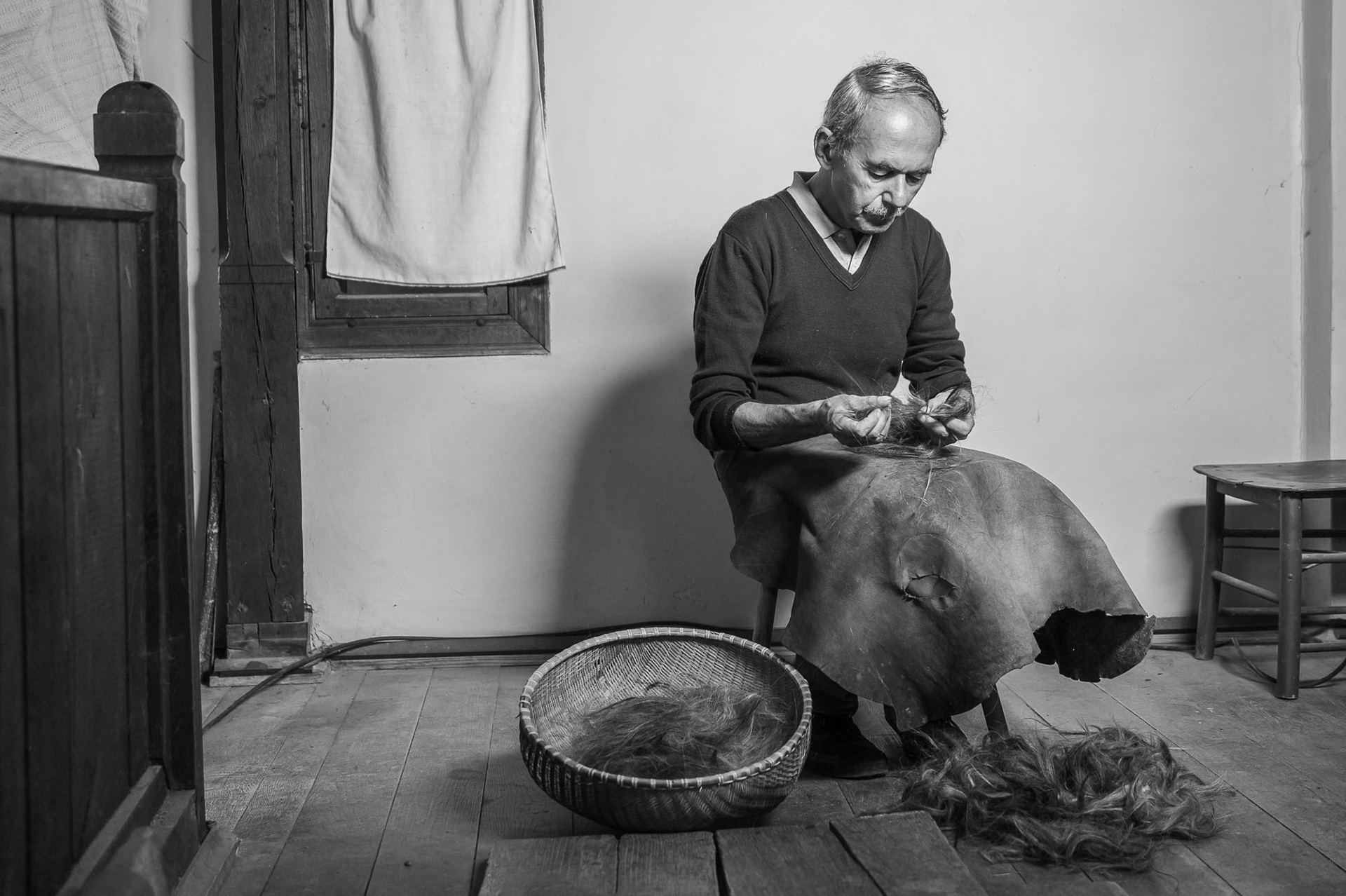
Cleaning and separating hair by hair
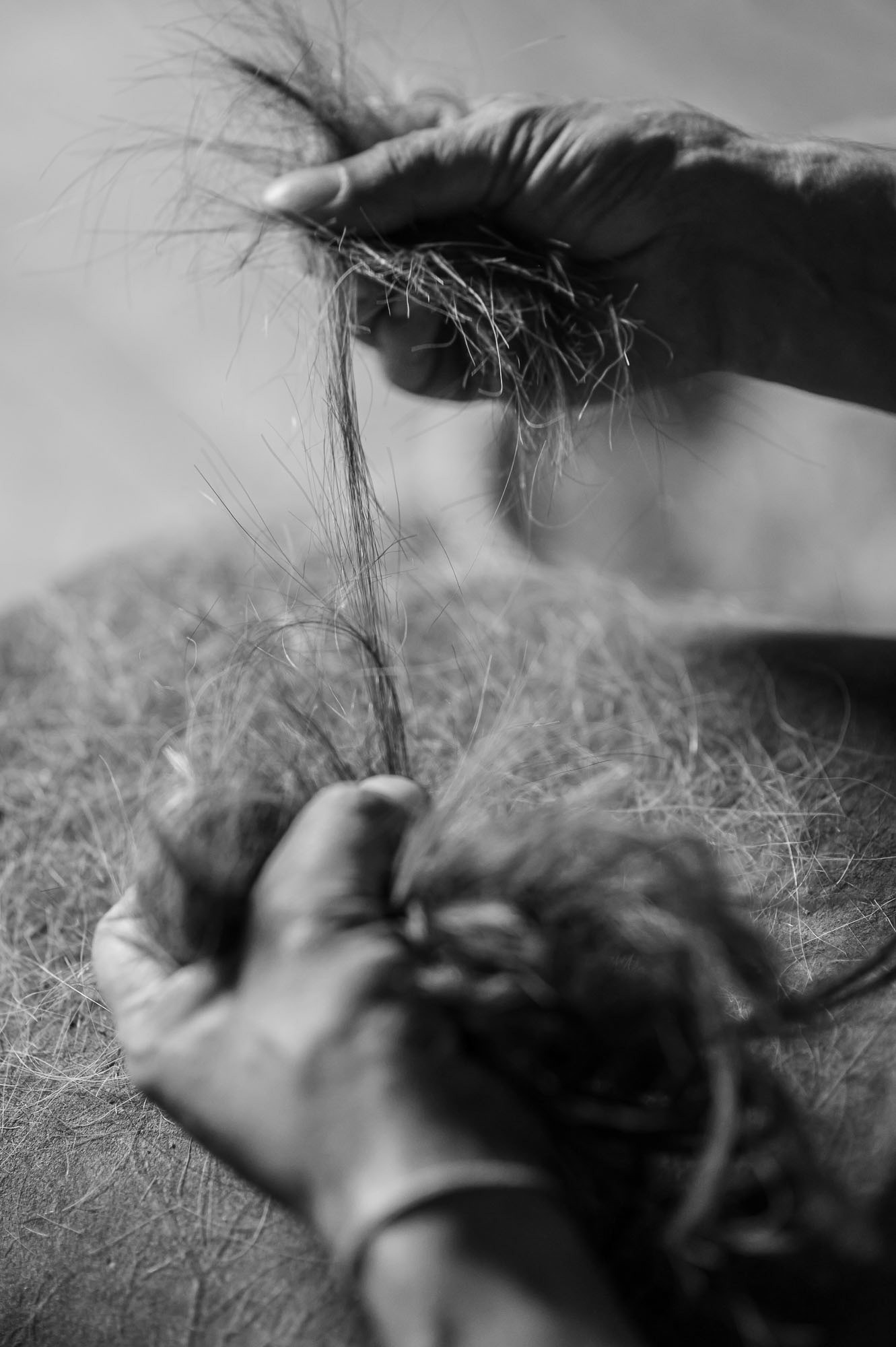
In structure, goat fur resembles human hair
“The main challenge is raw material supply. Goat herds are constantly in decline, and there was a year we had to get supplies from Greece.”
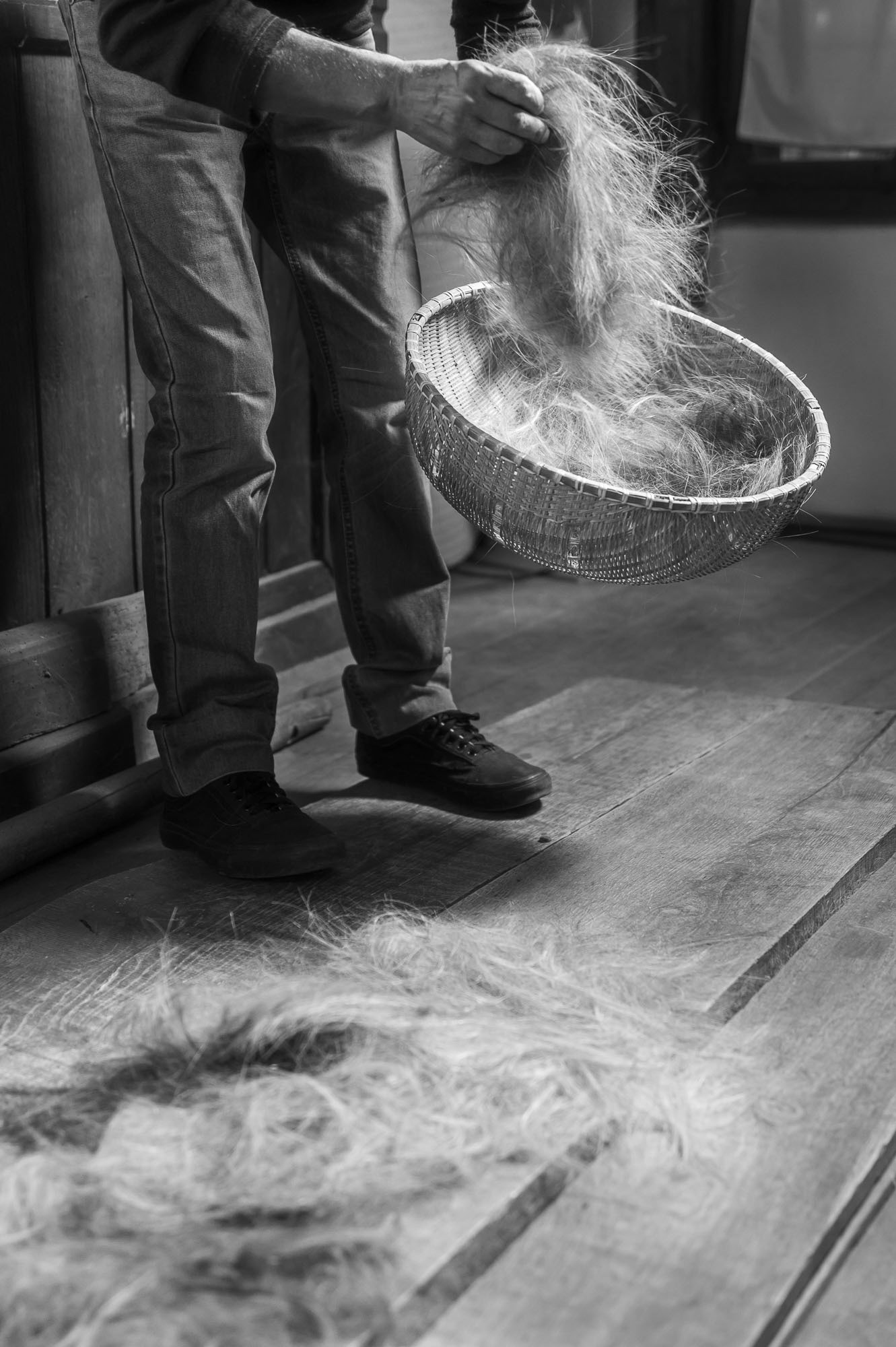
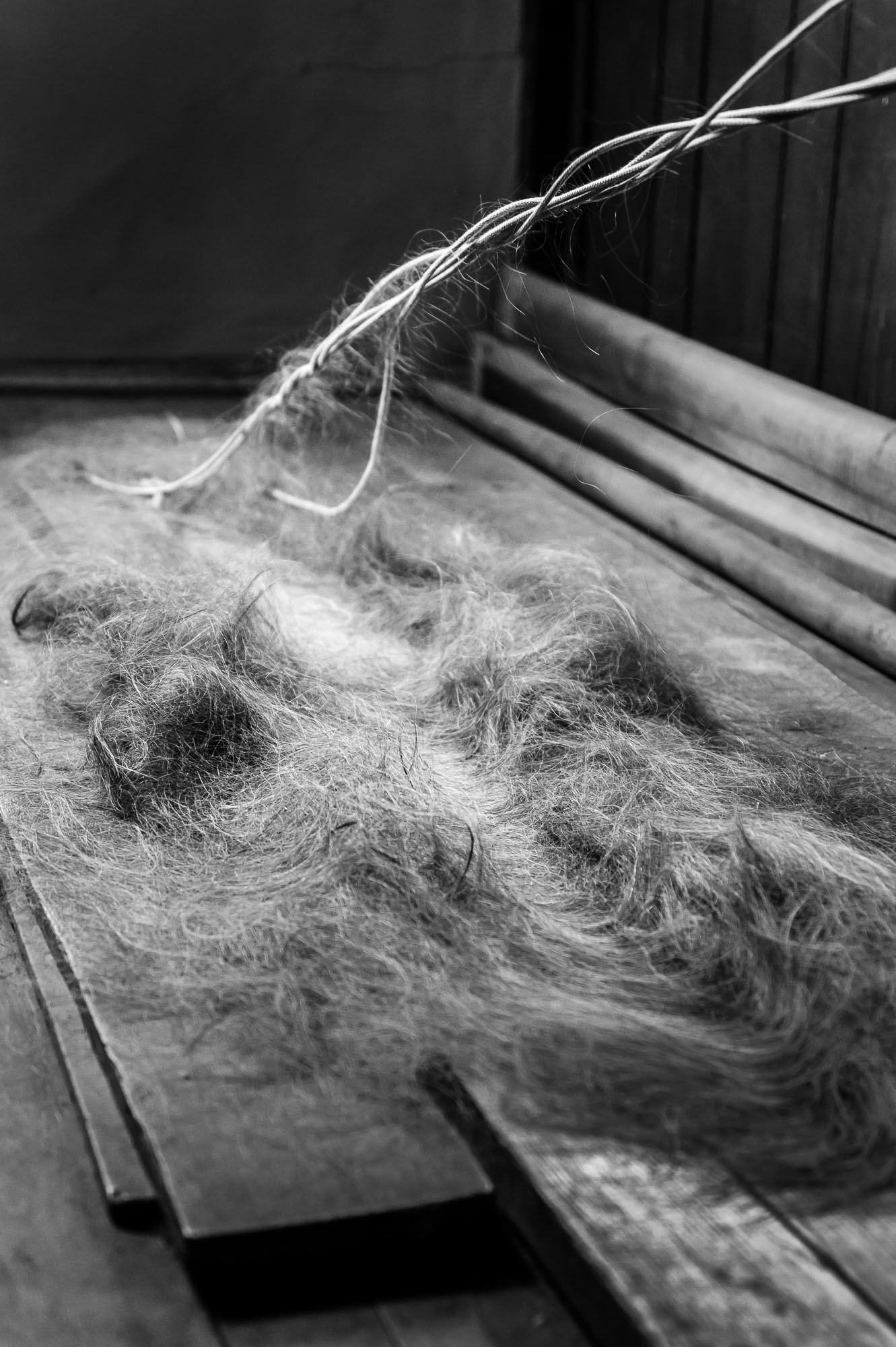
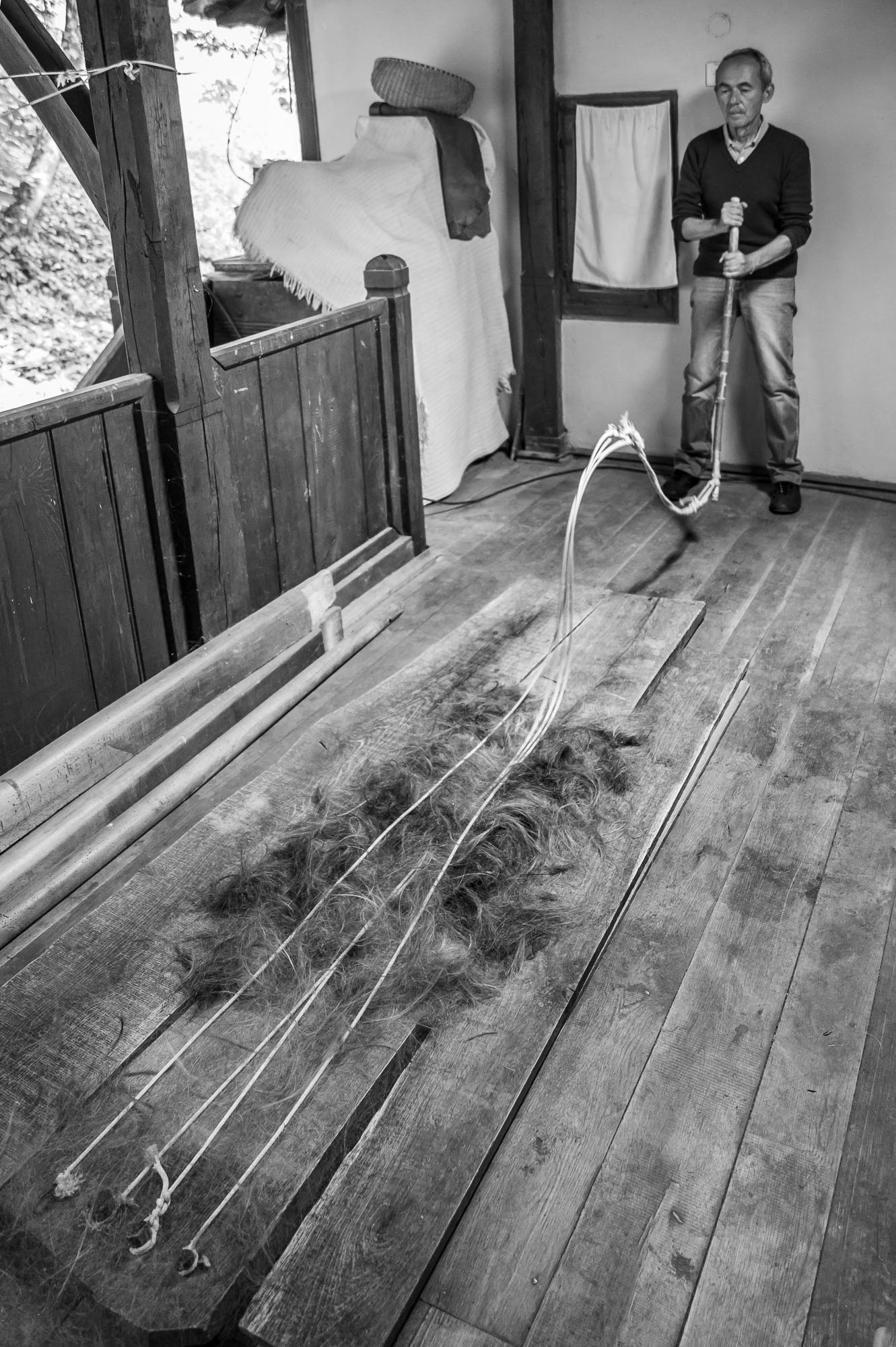
In the next stage, the fur is whipped until it becomes fluffy, ready to be spun into yarn
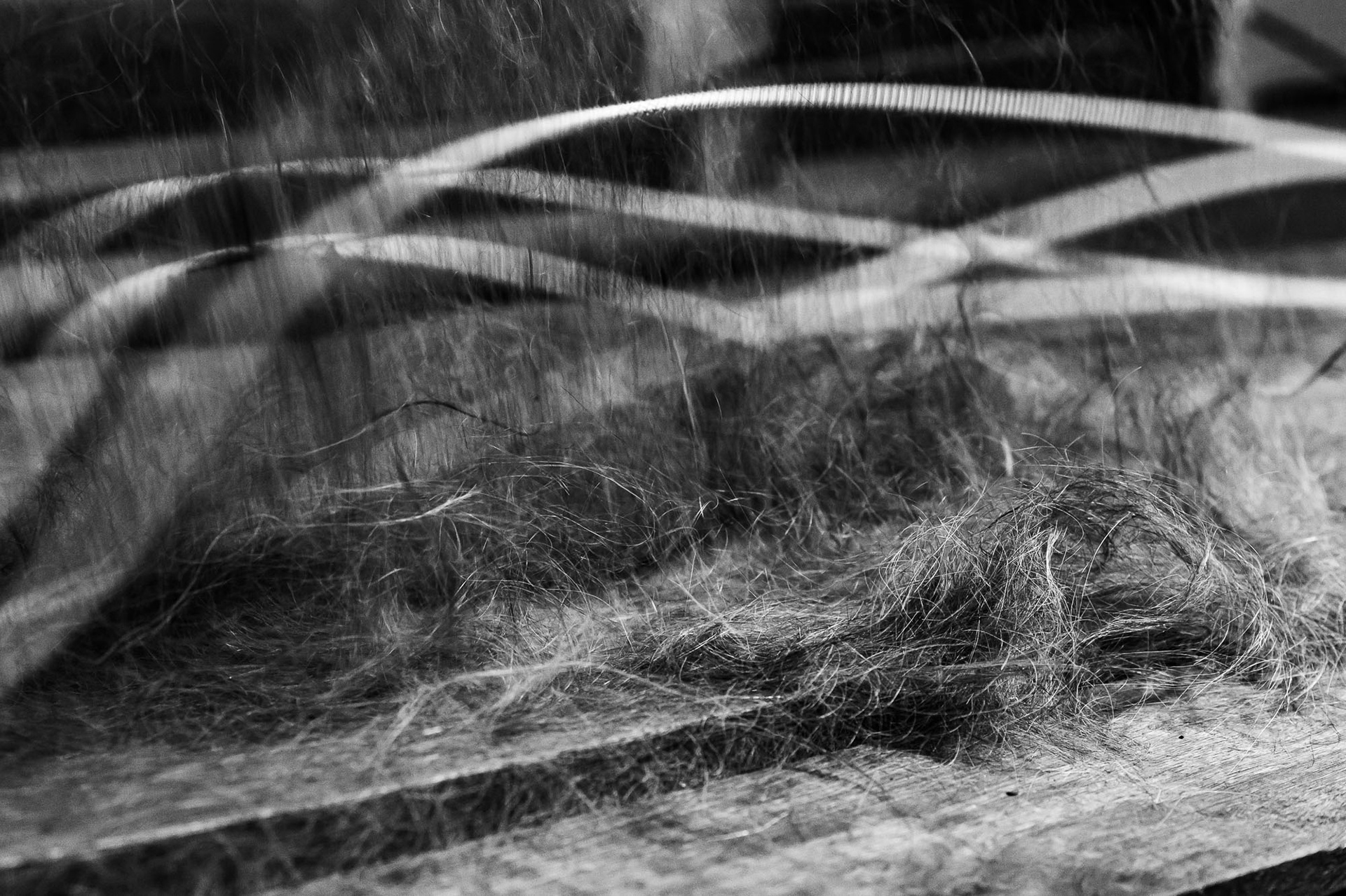
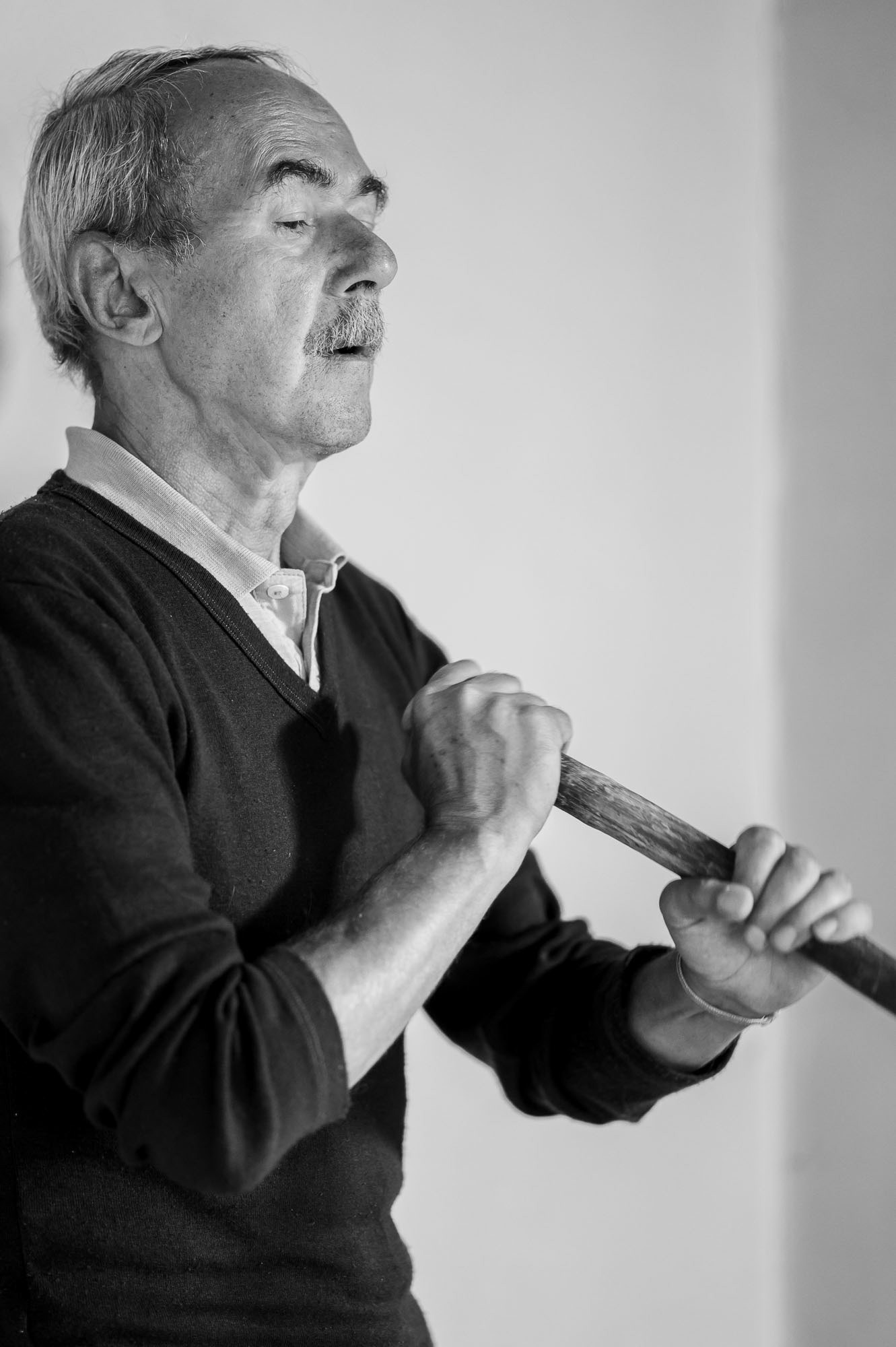
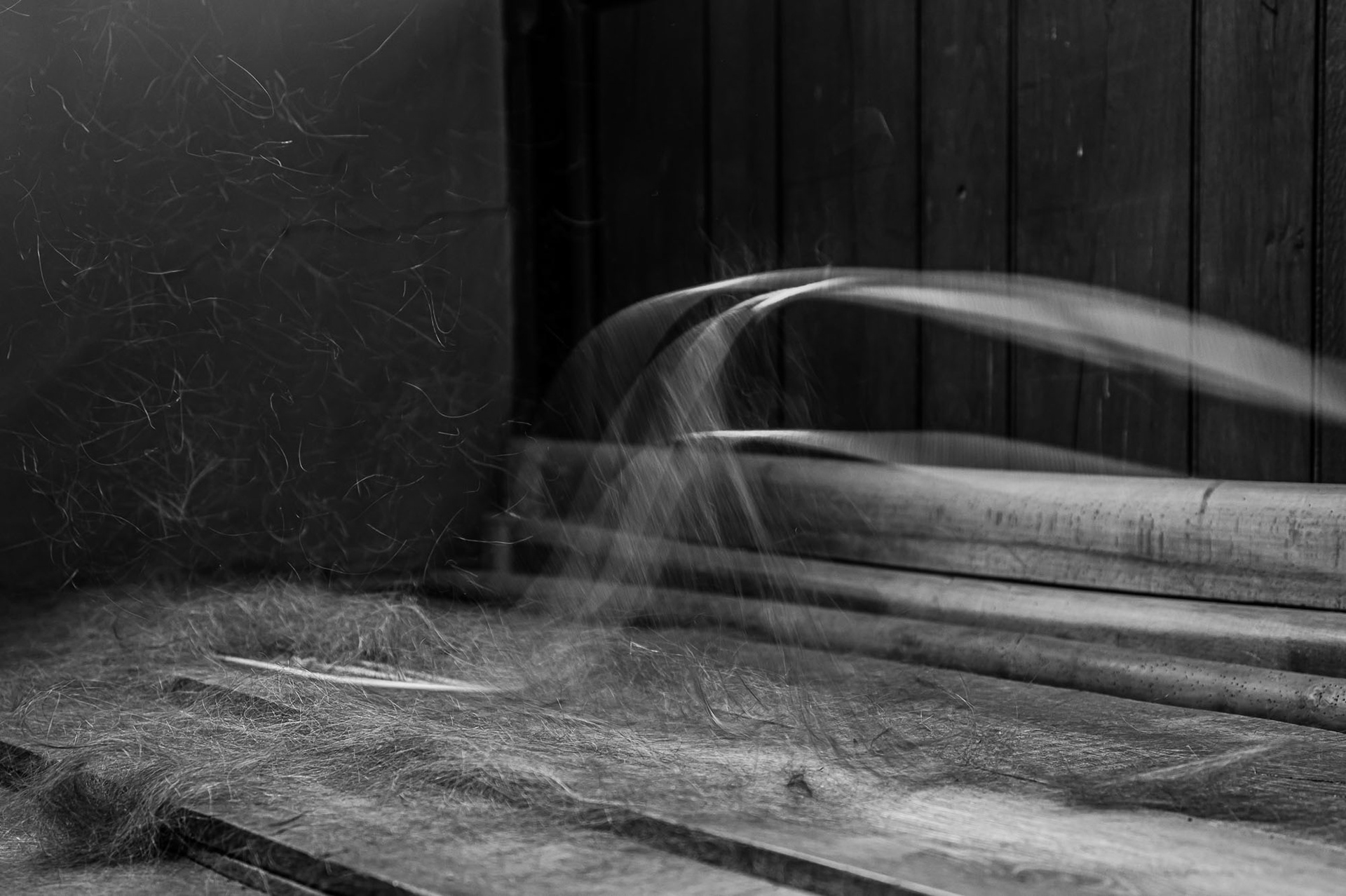
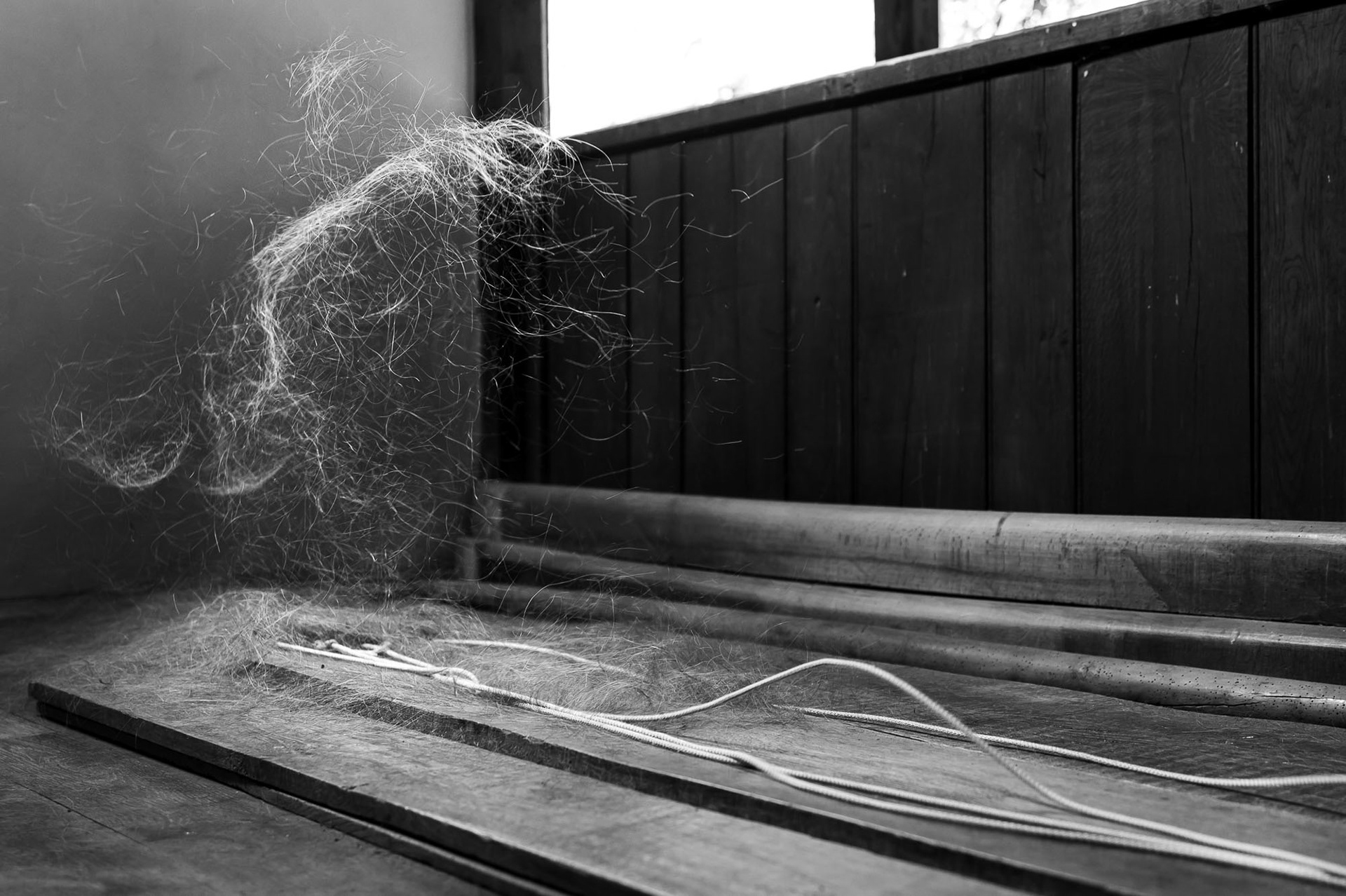
Whipping the fur
“It takes about two weeks to make a long rug – everything is made by hand on the spot at the workshop – from processing goat hair, through rug making to the finishing works.”
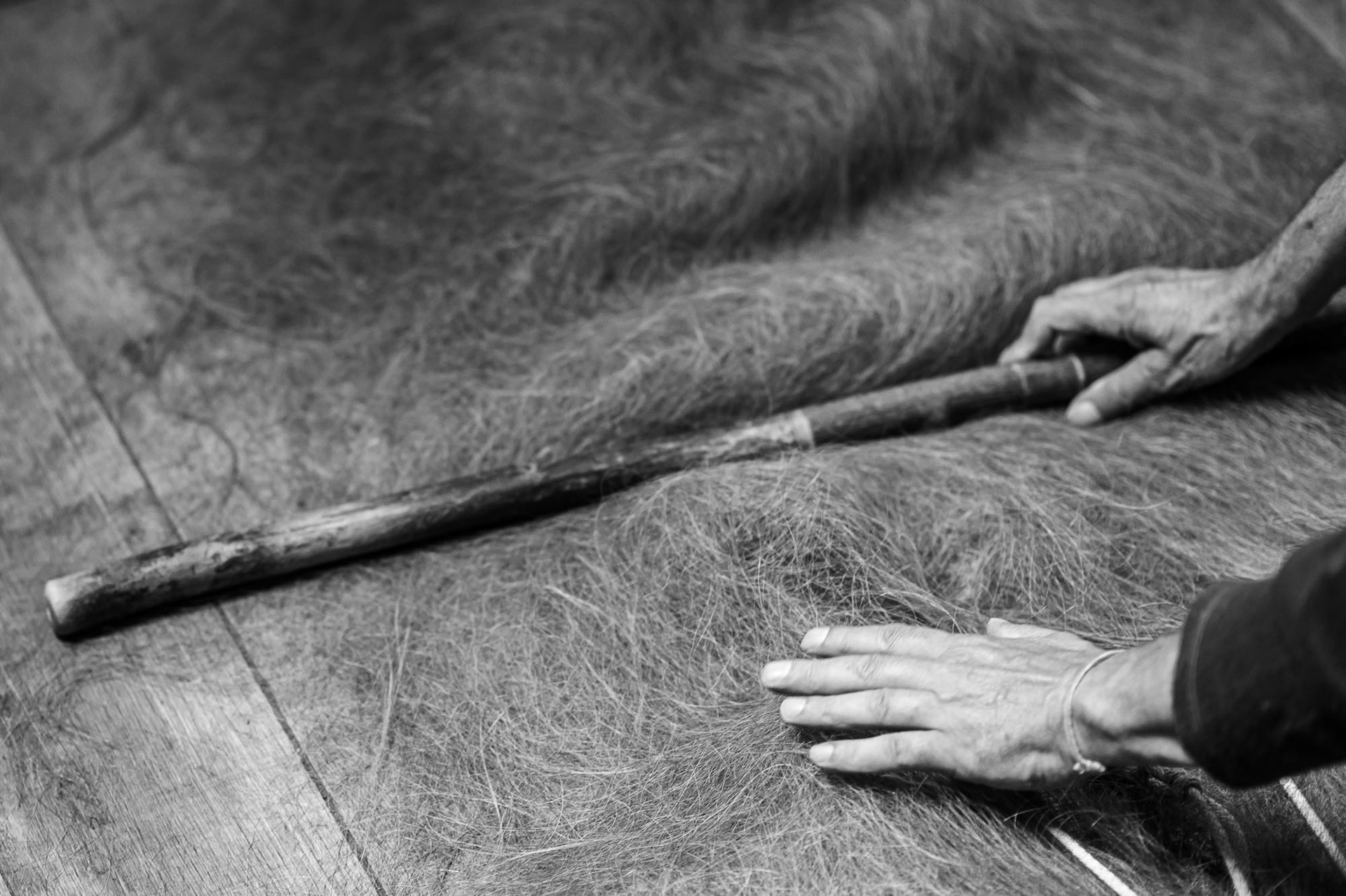
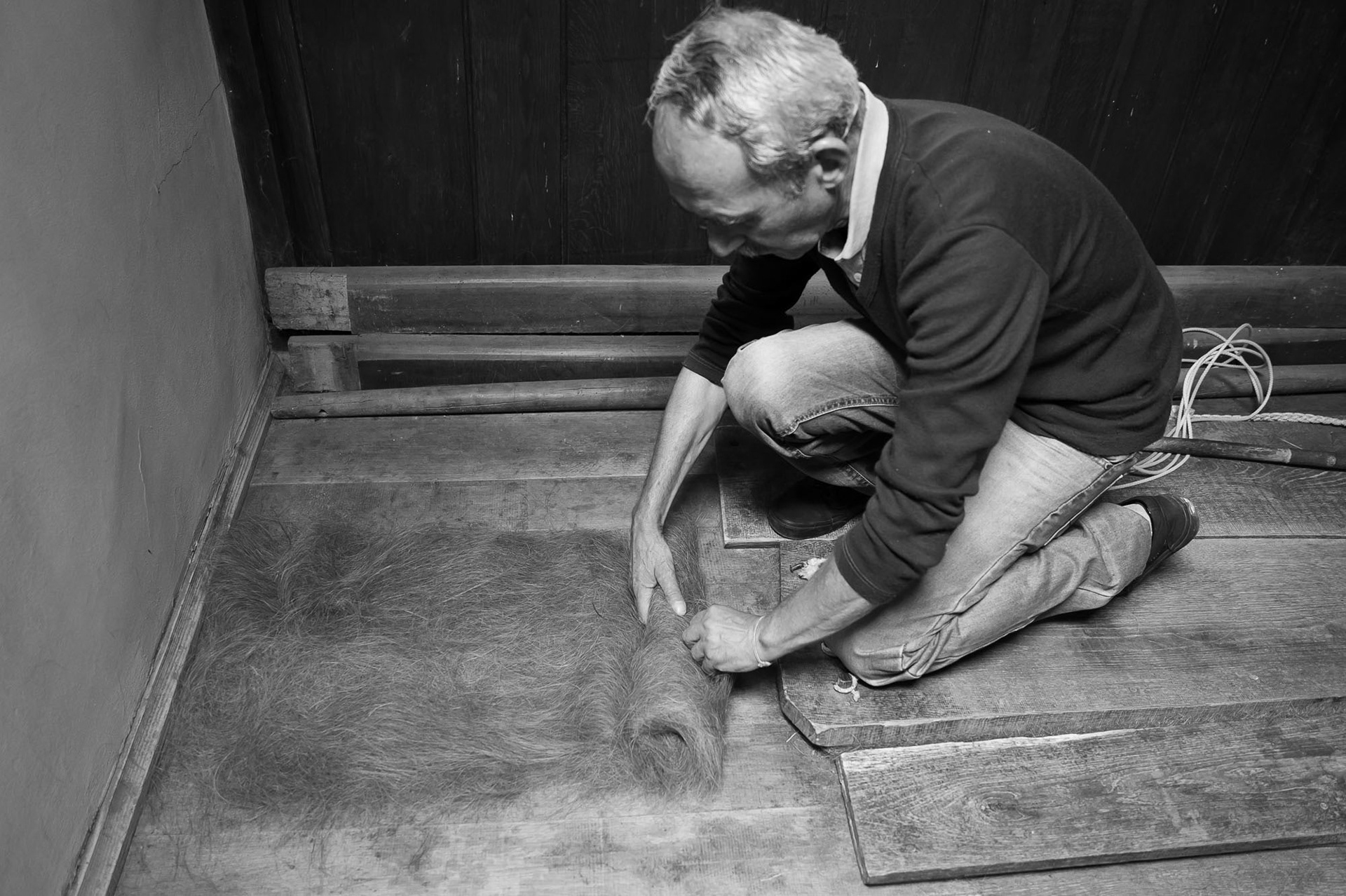
The well-beaten fur is shaped into a roll
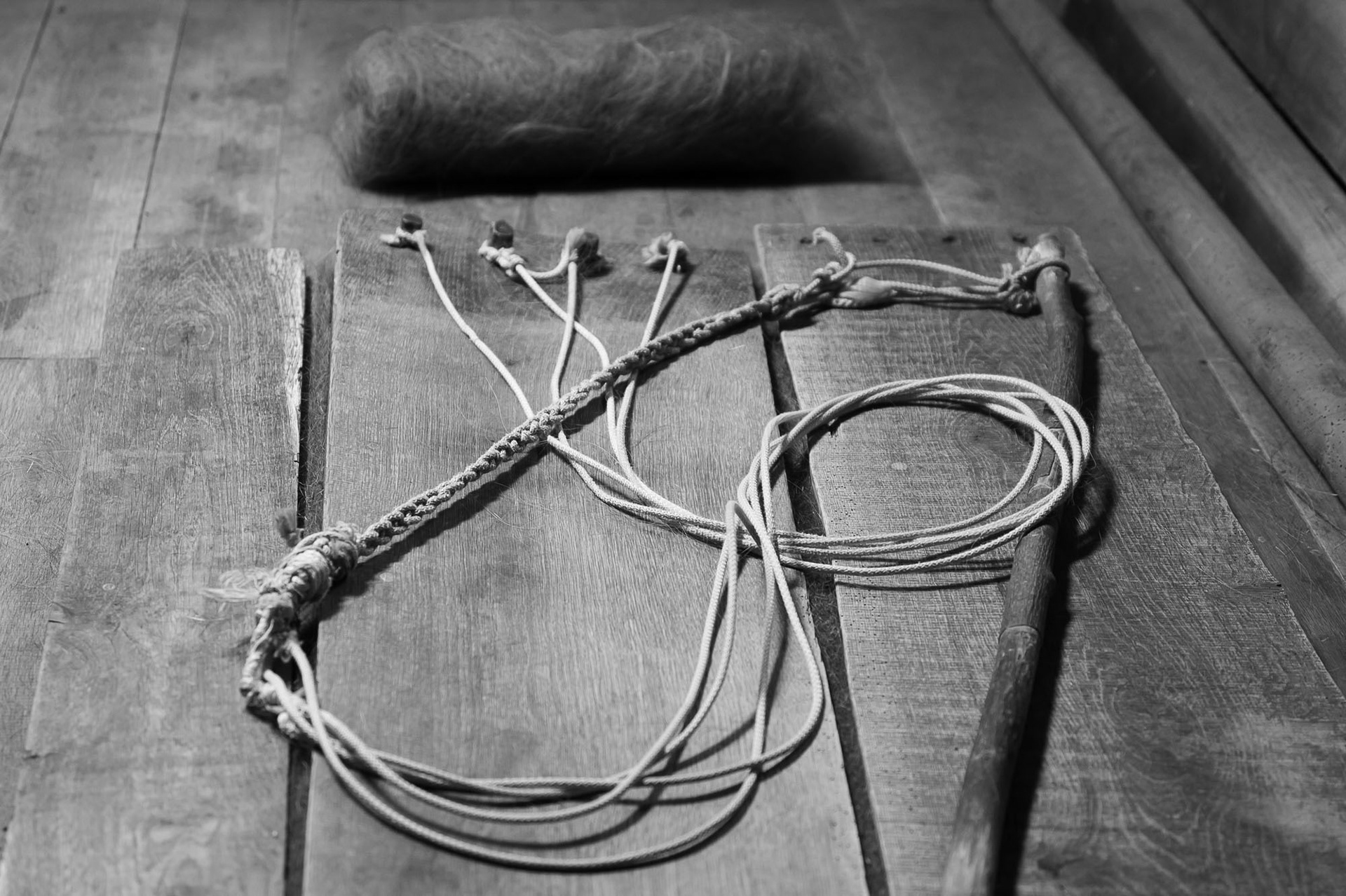
Device for whipping fur – a board with cotton ropes
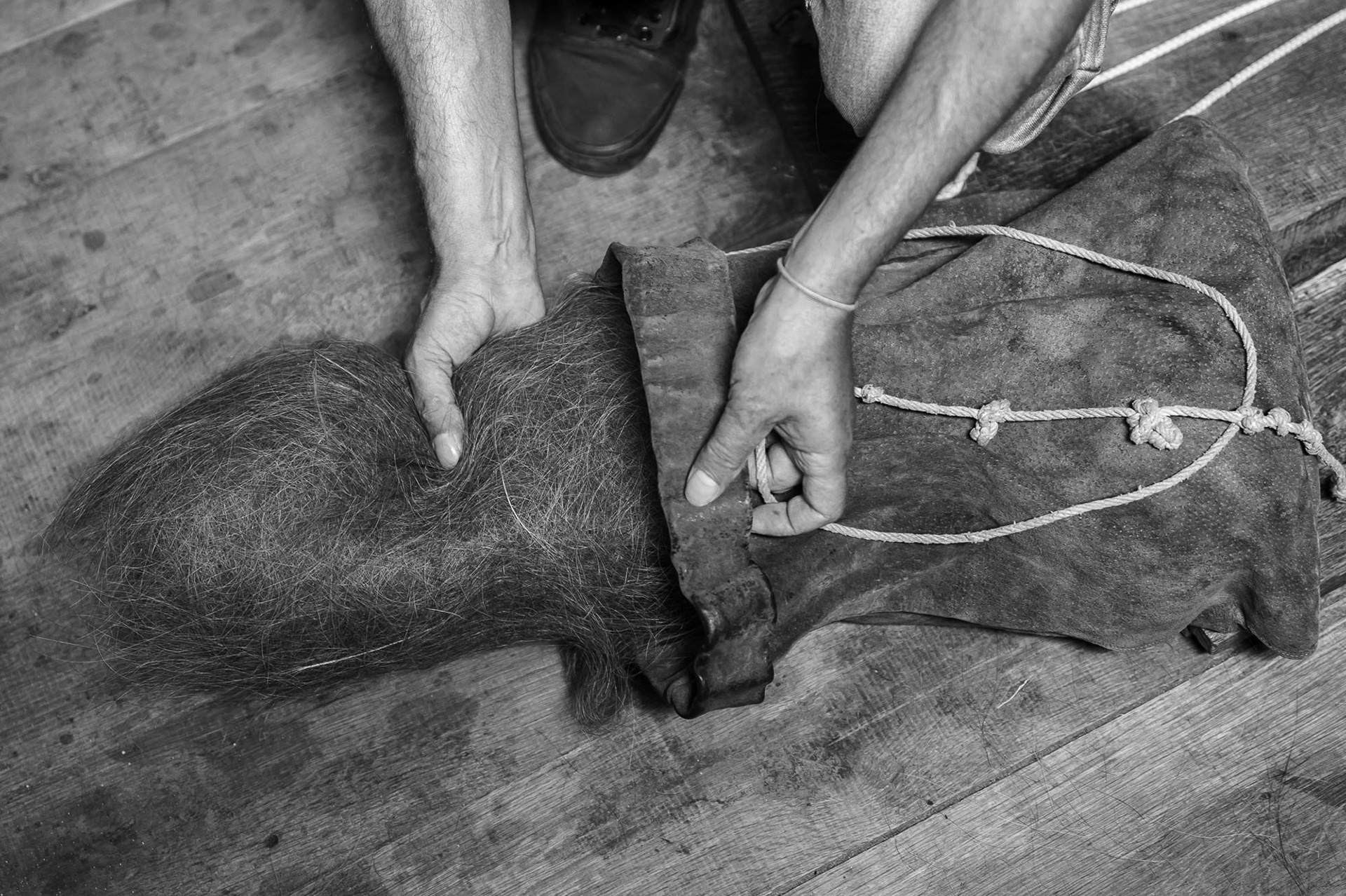
The rolled fur is placed into a “vulia” – a leather bag
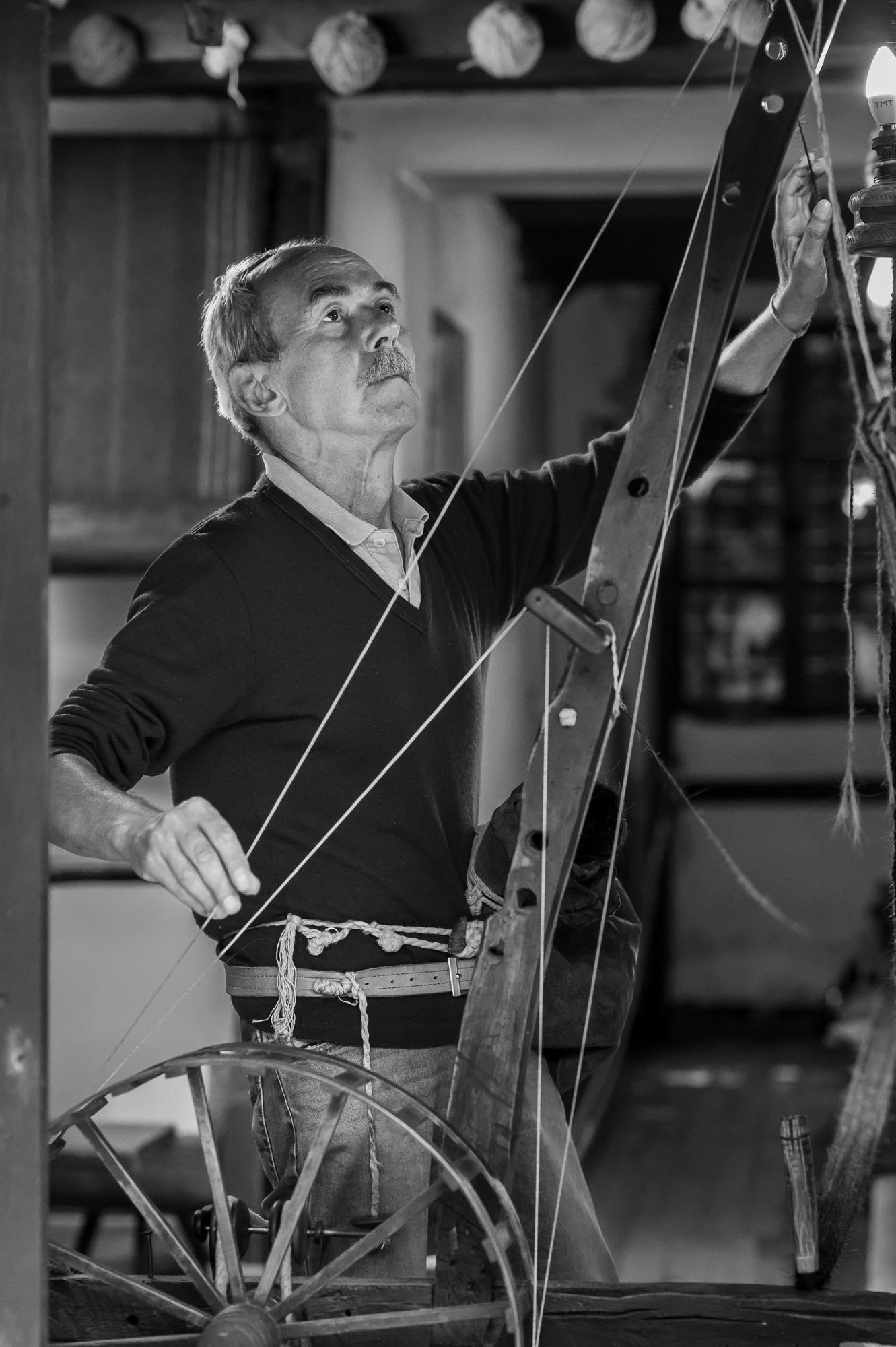
Master experience shows in every item made by Hristo Marinov – both as artistic worth and technical performance. He has mastered every process from separating the goat hair into color ranges – white, grey, black, beige and ocher to reddish-brown, through picking and beating the hair with ropes to obtain fluffy twills, on to spinning and twisting on the spinning-wheel, unique for the craft, running the weft yarn through the warp of the vertical loom, weaving proper, and all the way to the finishing stitches and braiding the edges of the fabric. Goat hair and goat yarn are exclusively used in all operations. It takes about a week to make a bag from start to finish, and about two weeks – to make a two-meter long rug.
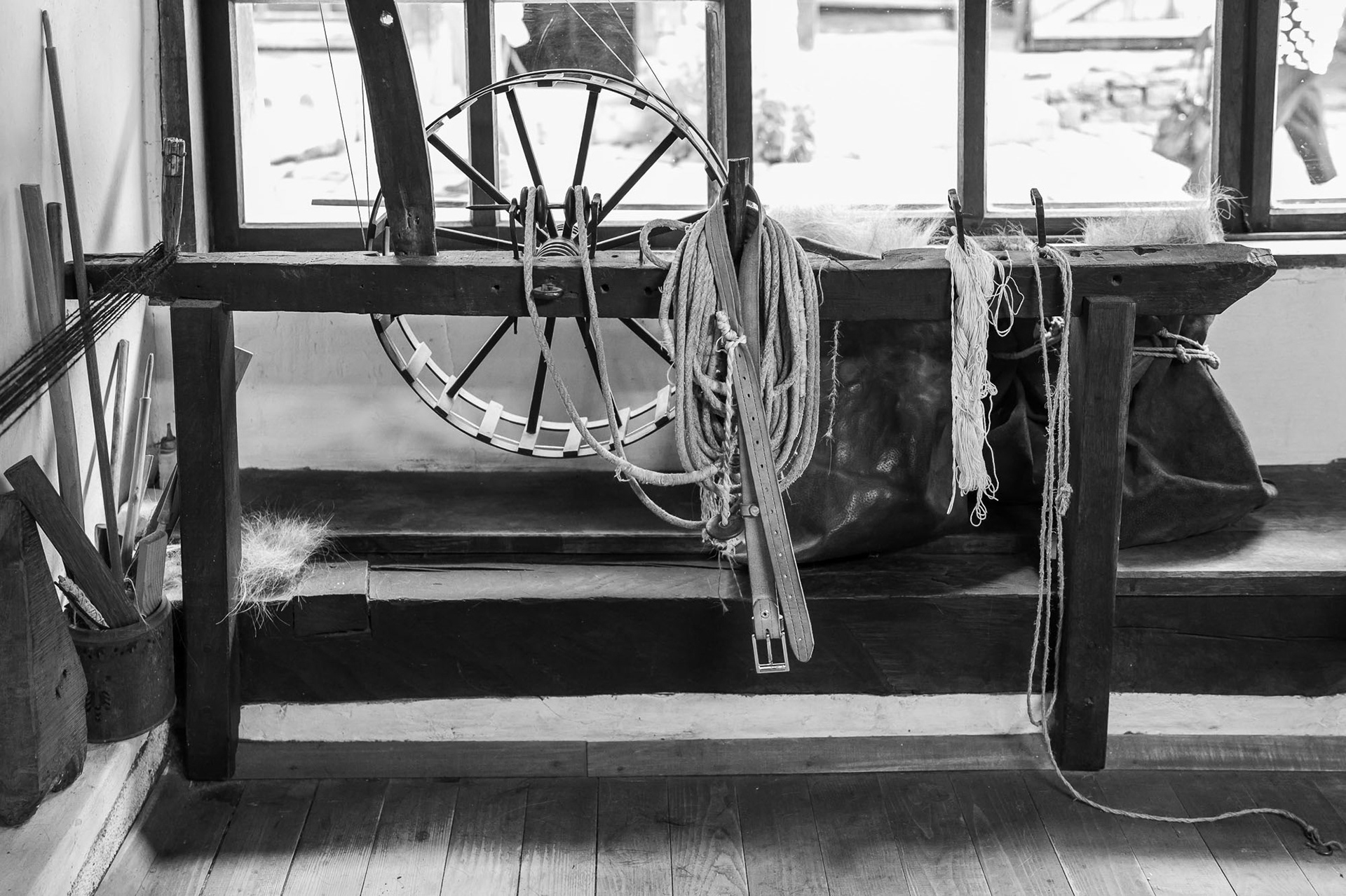
Mutafchi's spinning wheel
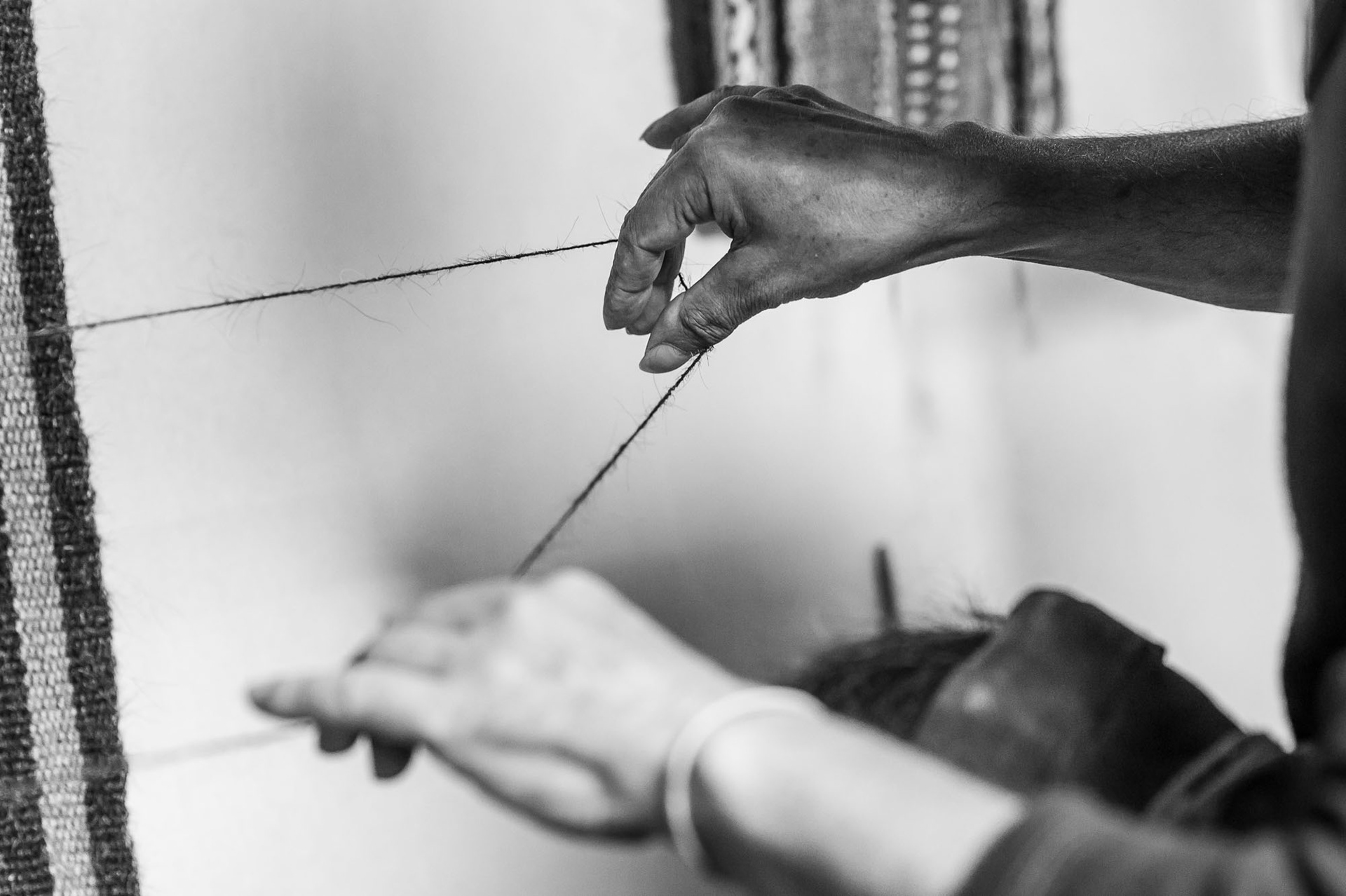
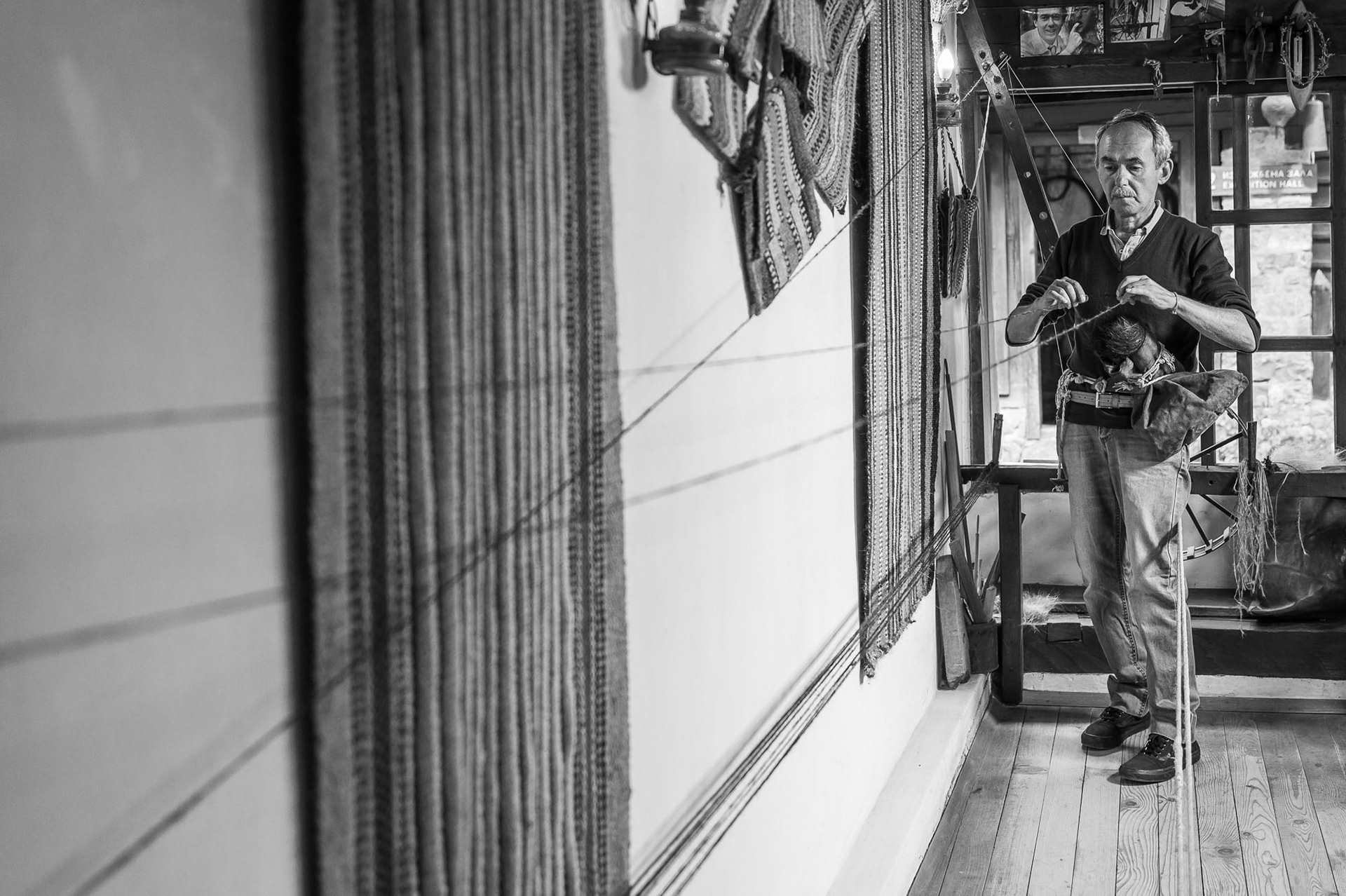
The artisan puts the leather bag in which the fur is rolled up under his arm. It is tied around the waist with a leather belt, attached to a rope that drives the mutafchi wheel.
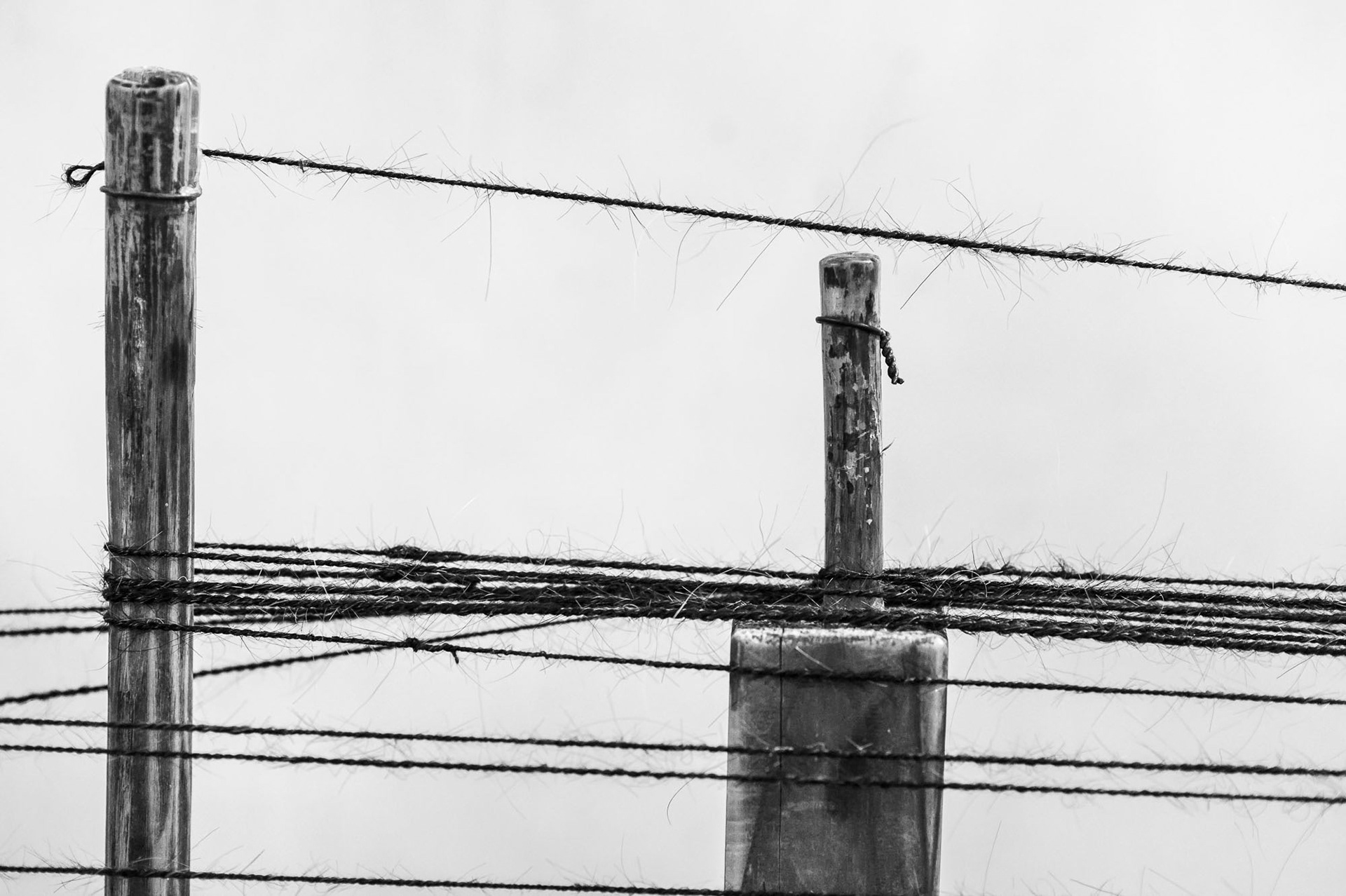
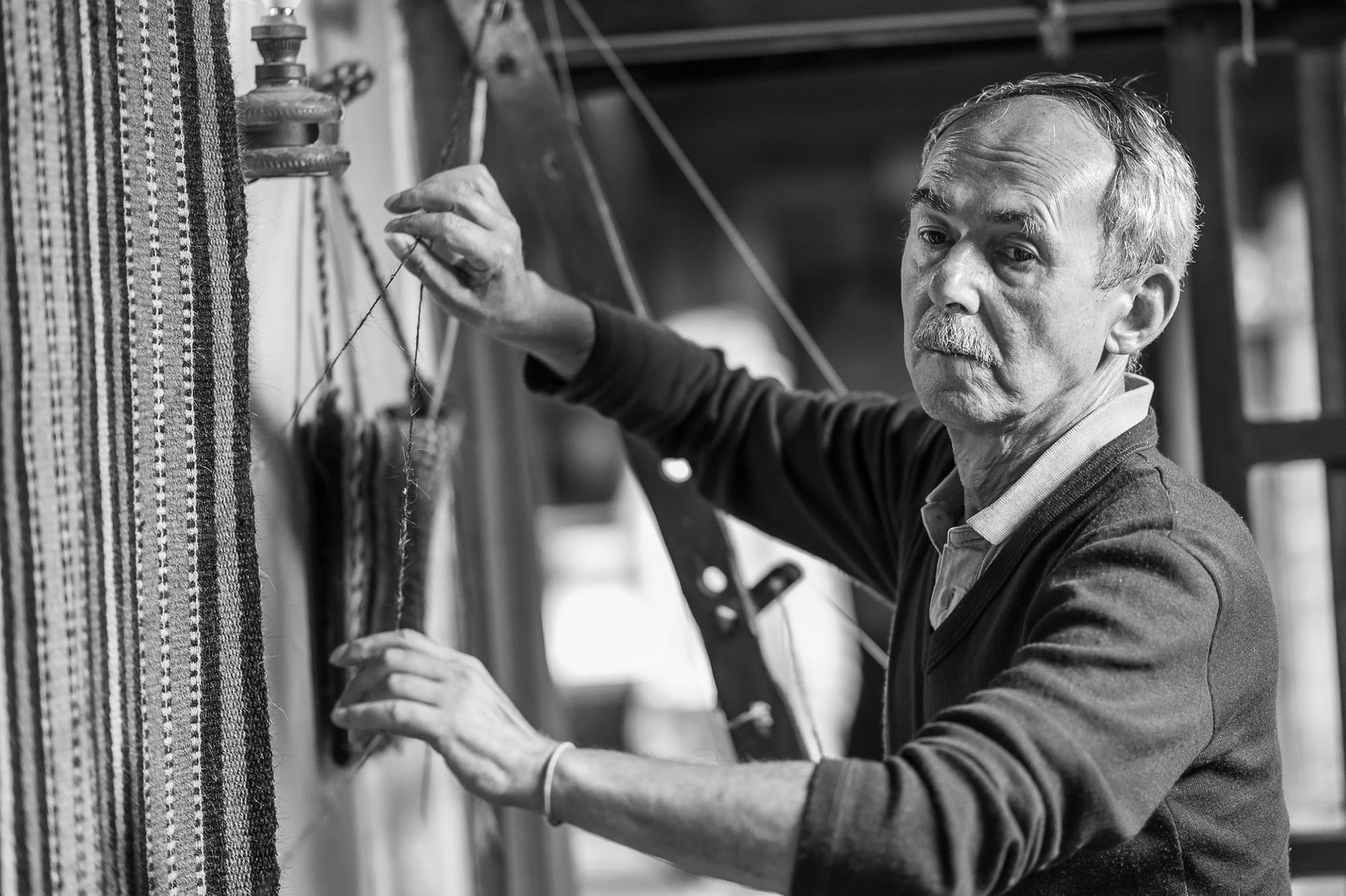
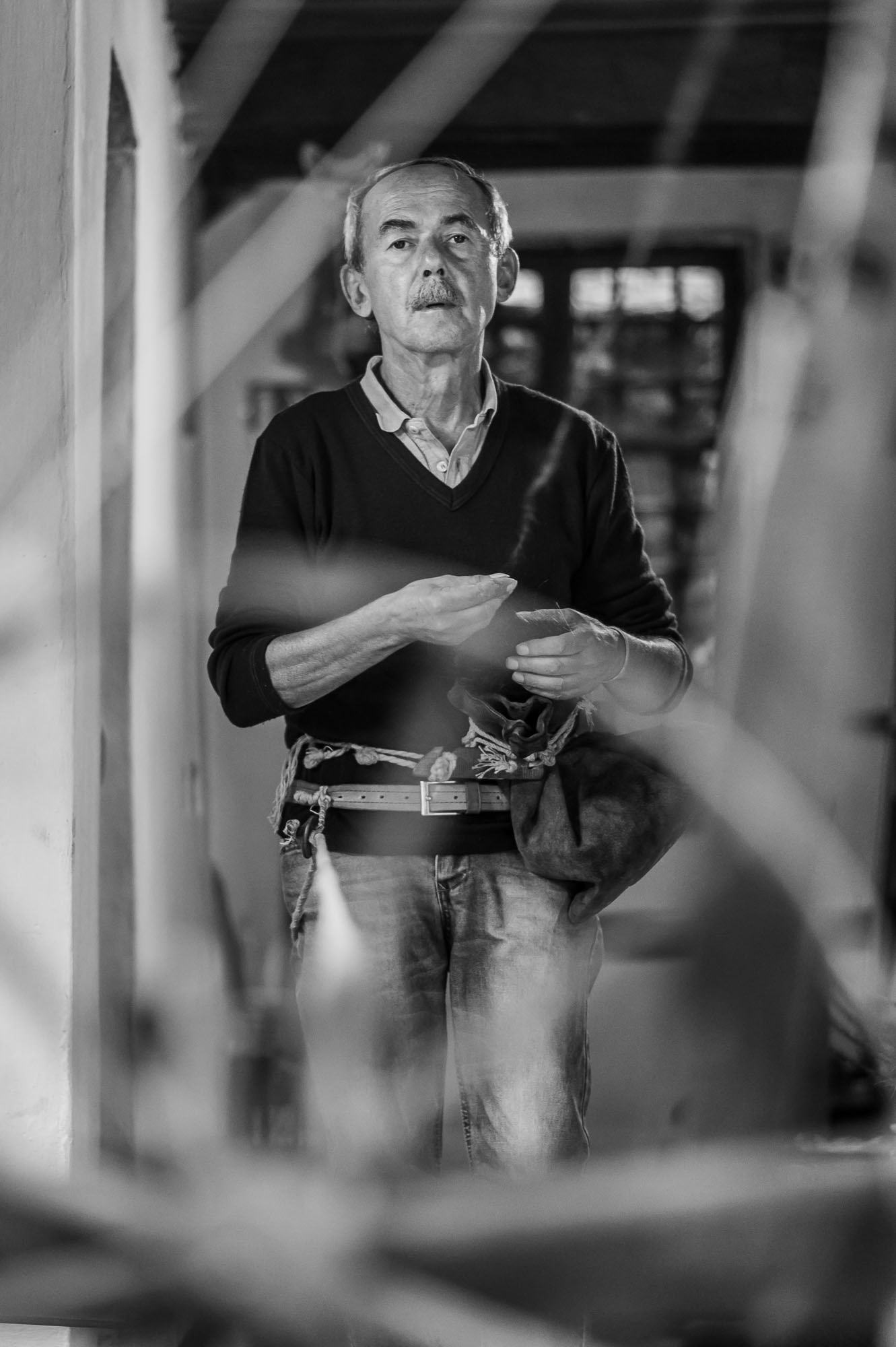
Spinning a thread with a Mutafchii wheel – the master is straight and, moving backwards, begins to spin.
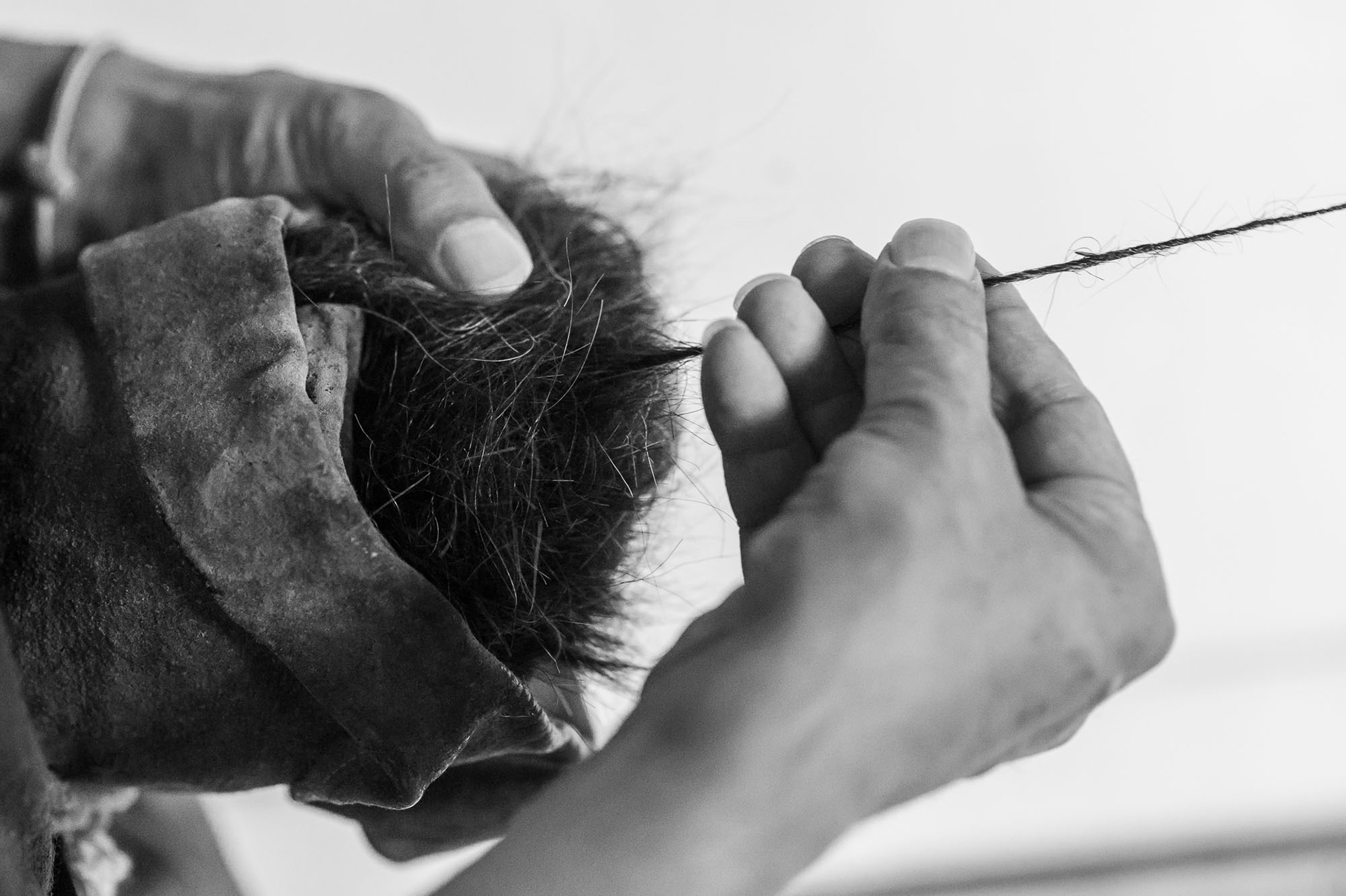
Spinning is the pulling of a thin, increasingly long thread into a wick that is twisted
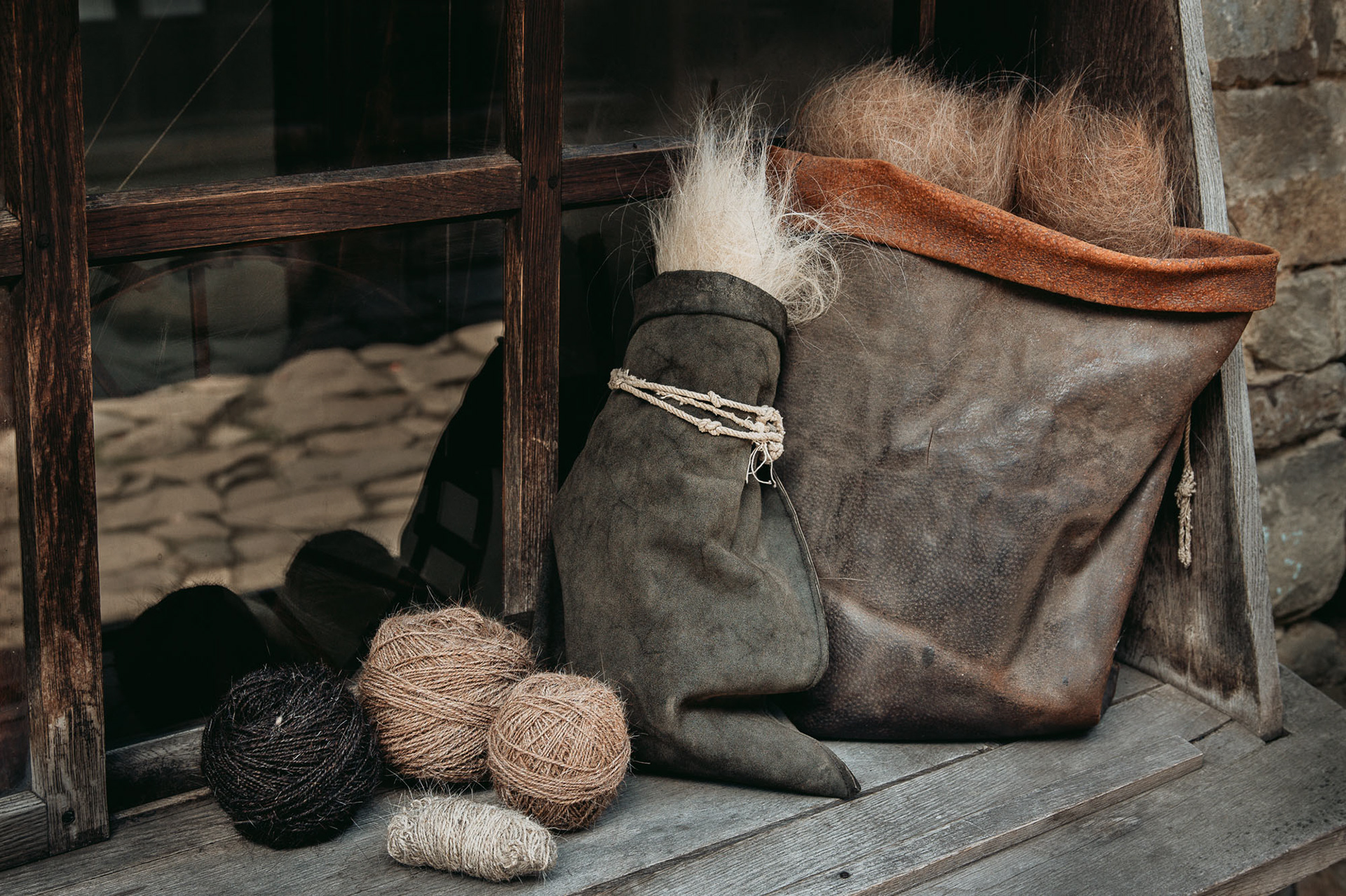
Yarn is spun from the cleaned and color-sorted fur. The end product of spinning is the balls of hair threads (also called weft), which are interwoven with the warp when woven into fabric.

Master Marinov is also skilled in the full maintenance of the tools and appliances in the workshop, which are predominantly over a century old. In order to be able to replace ropes of various thickness needed for the heddles of the loom, for beating the hair and for the structure of the spinning-wheel, the goat-hair artisan has also learned to knit ropes. He has gone an extra mile by preserving knowledge about dyeing the hair, although goat-hair working uses mostly the natural colors of the material. In the recent years, he has mastered tablet weaving of belts from wool, and he sometimes makes art panels from goat hair in a non-traditional style. For many years, Master Marinov has been presenting his craft at exhibitions both at home and abroad.
"The loom that I use to weave was made in 1903"
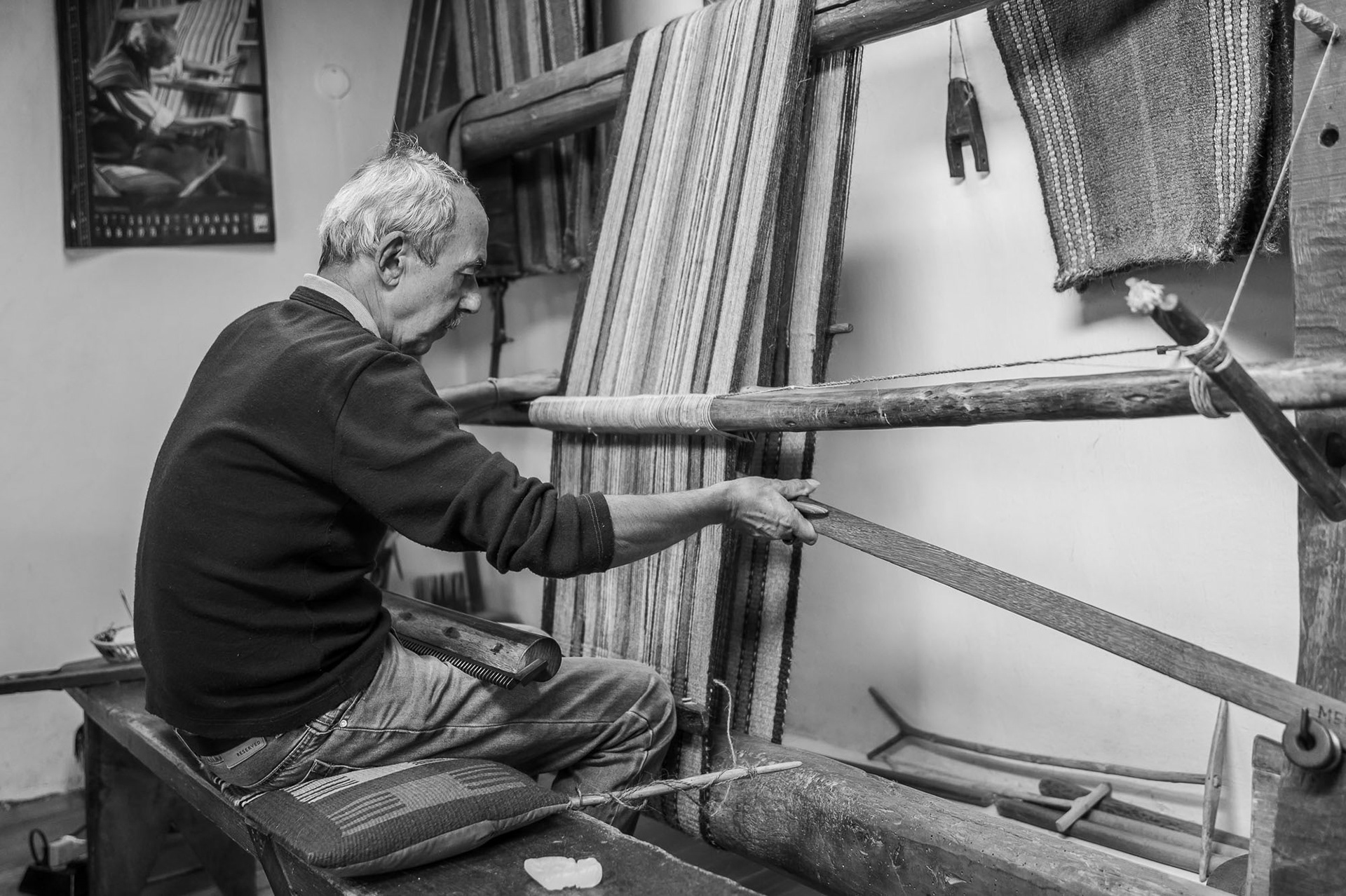
Weaving Mutafchii fabric
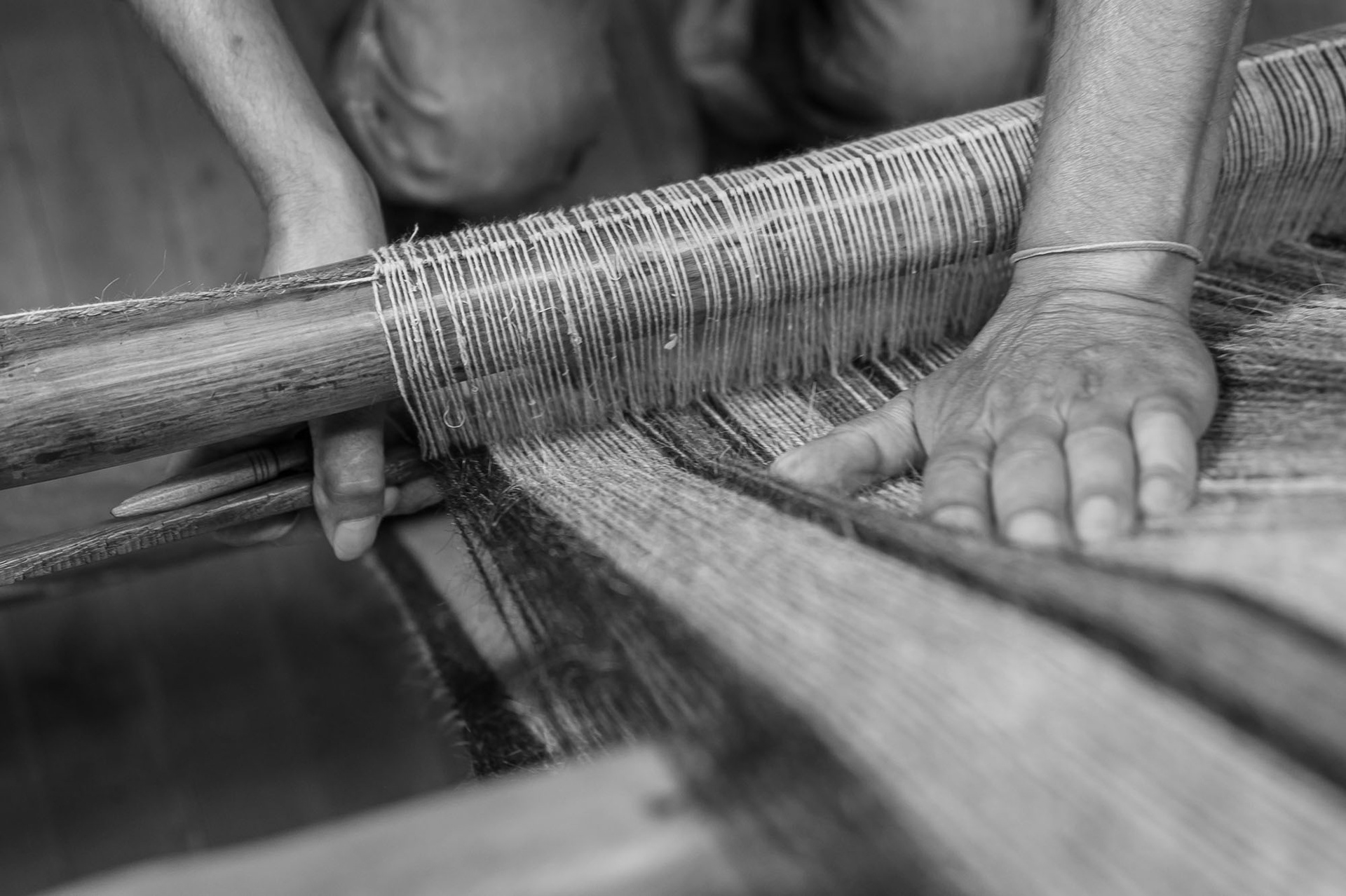
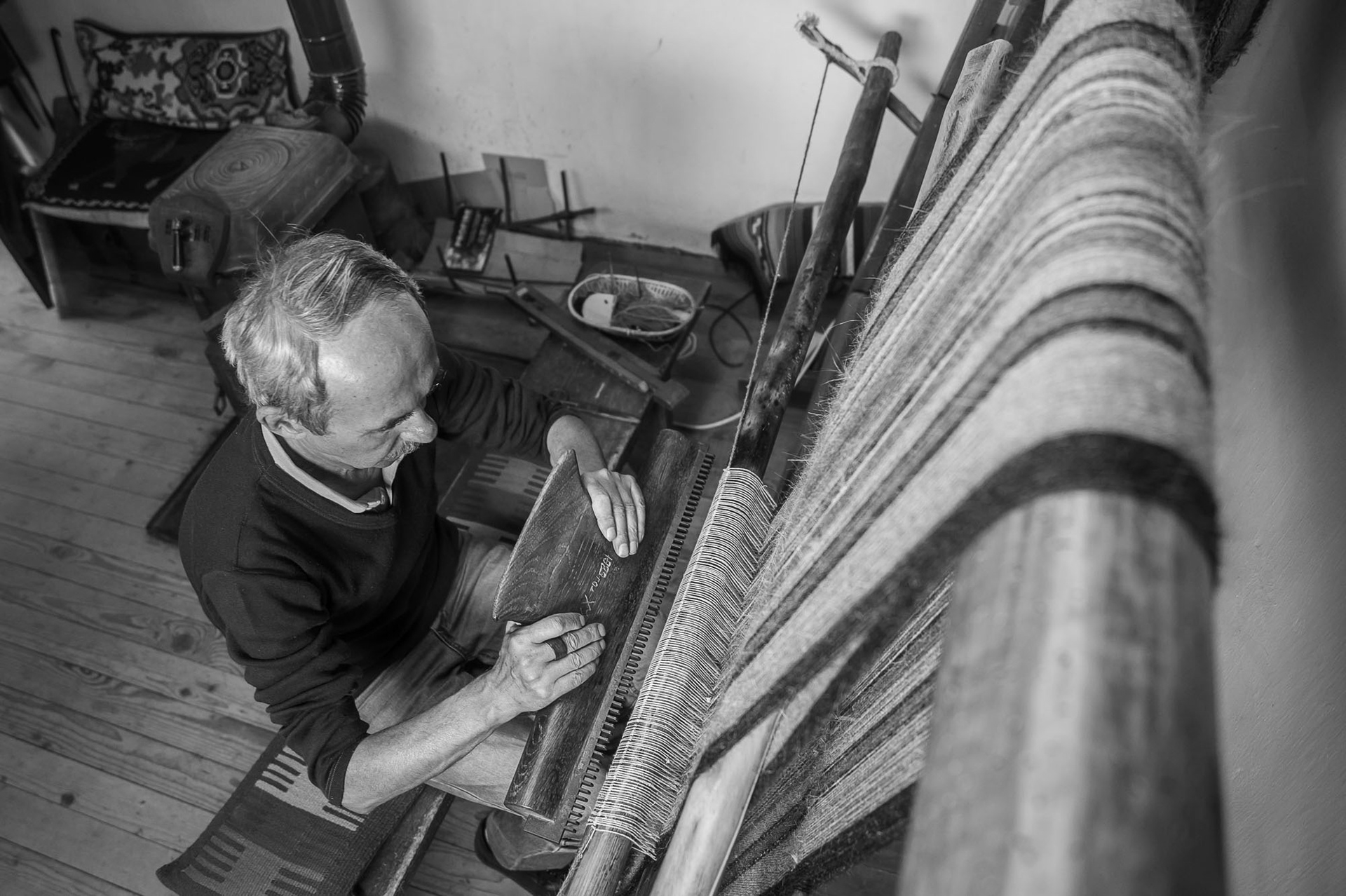
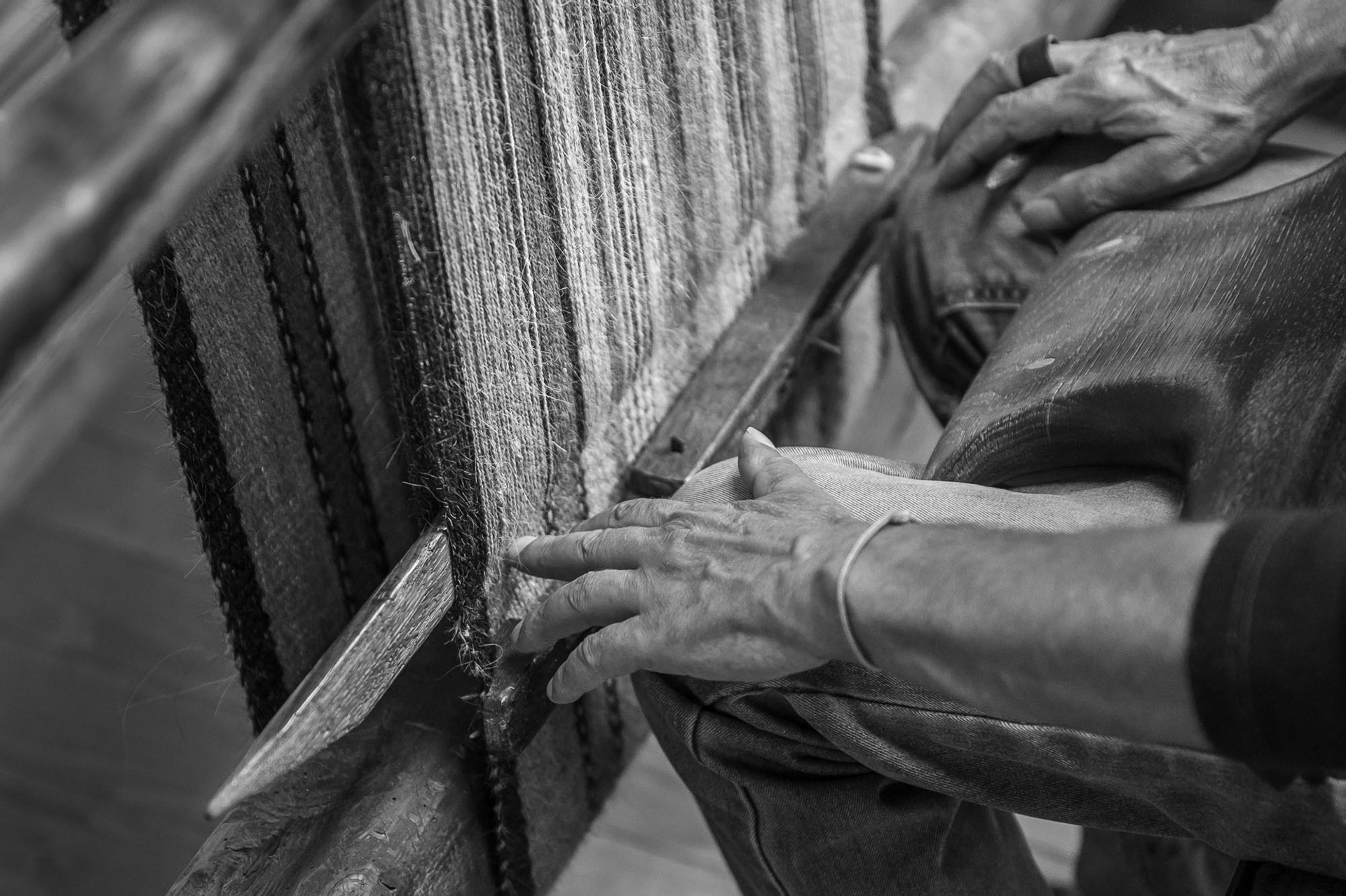
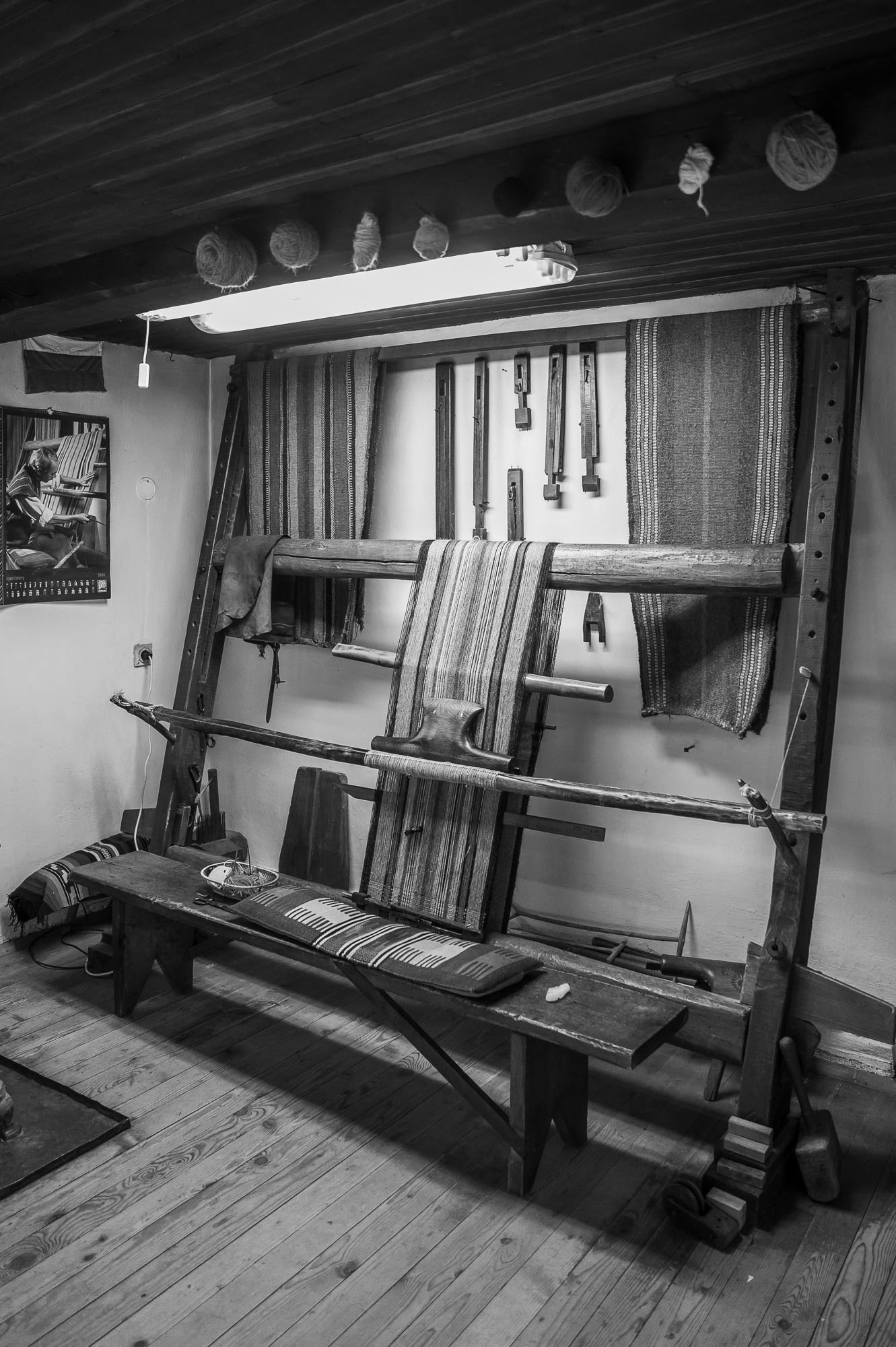
A vertical loom is used to weave traditional Mutafchi fabric
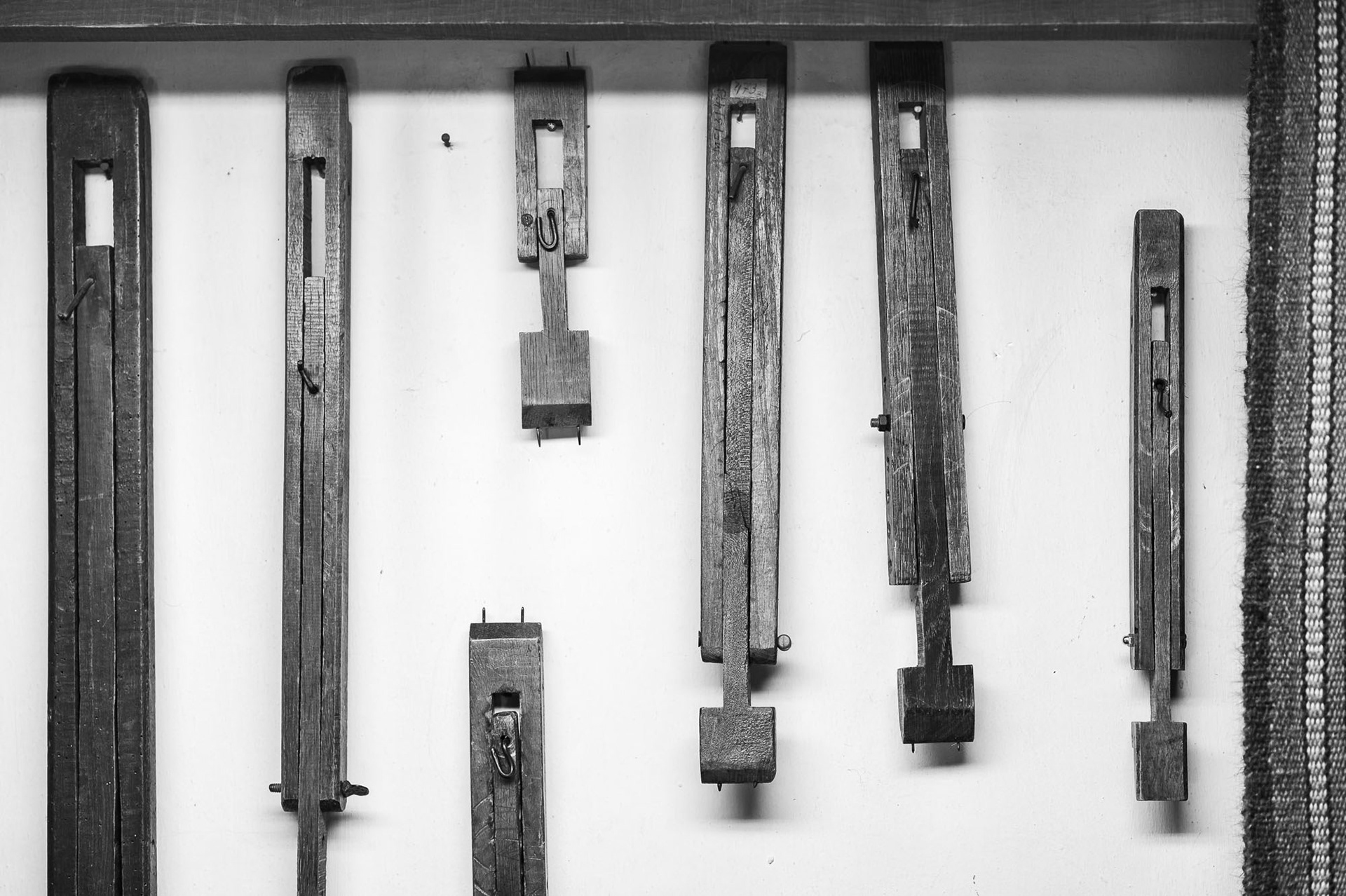
The width of the fabric is determined by the size of the tools used to stretch the cloth
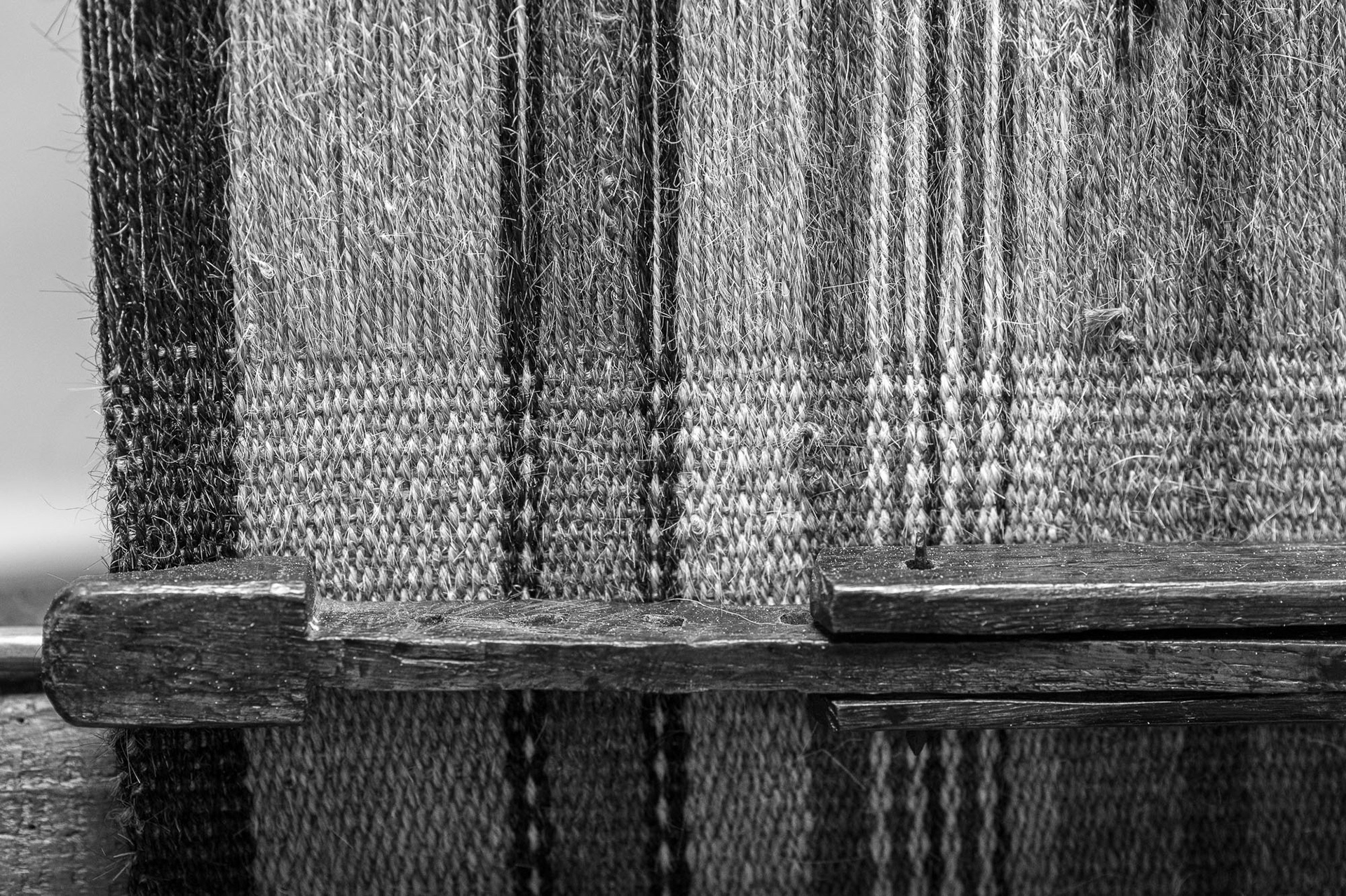
Stretching the fabric in the process of weaving
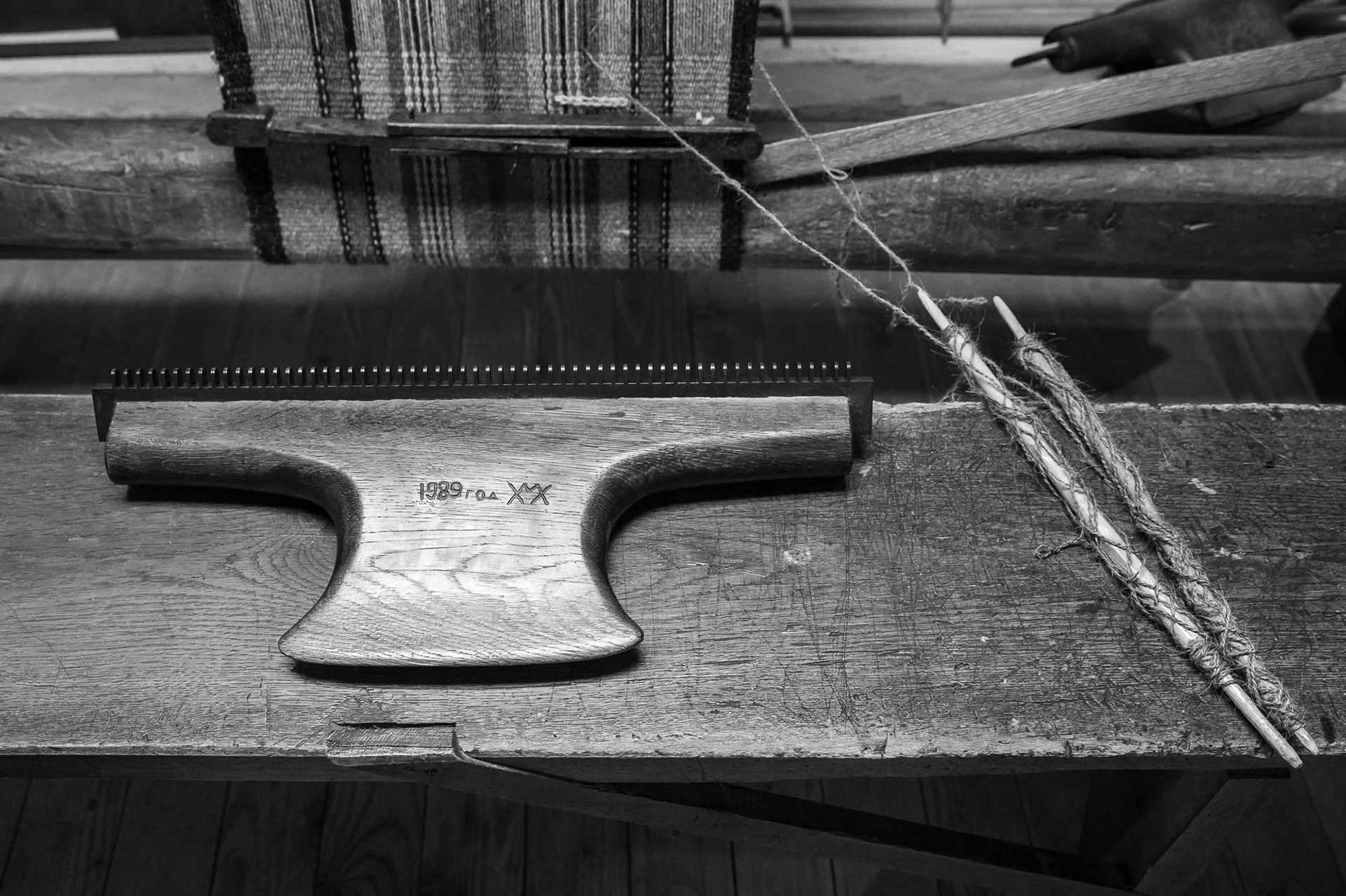
The tarak tool (a heavy comb with metal tines and a wooden handle) is used to beat the threads when weaving the cloth
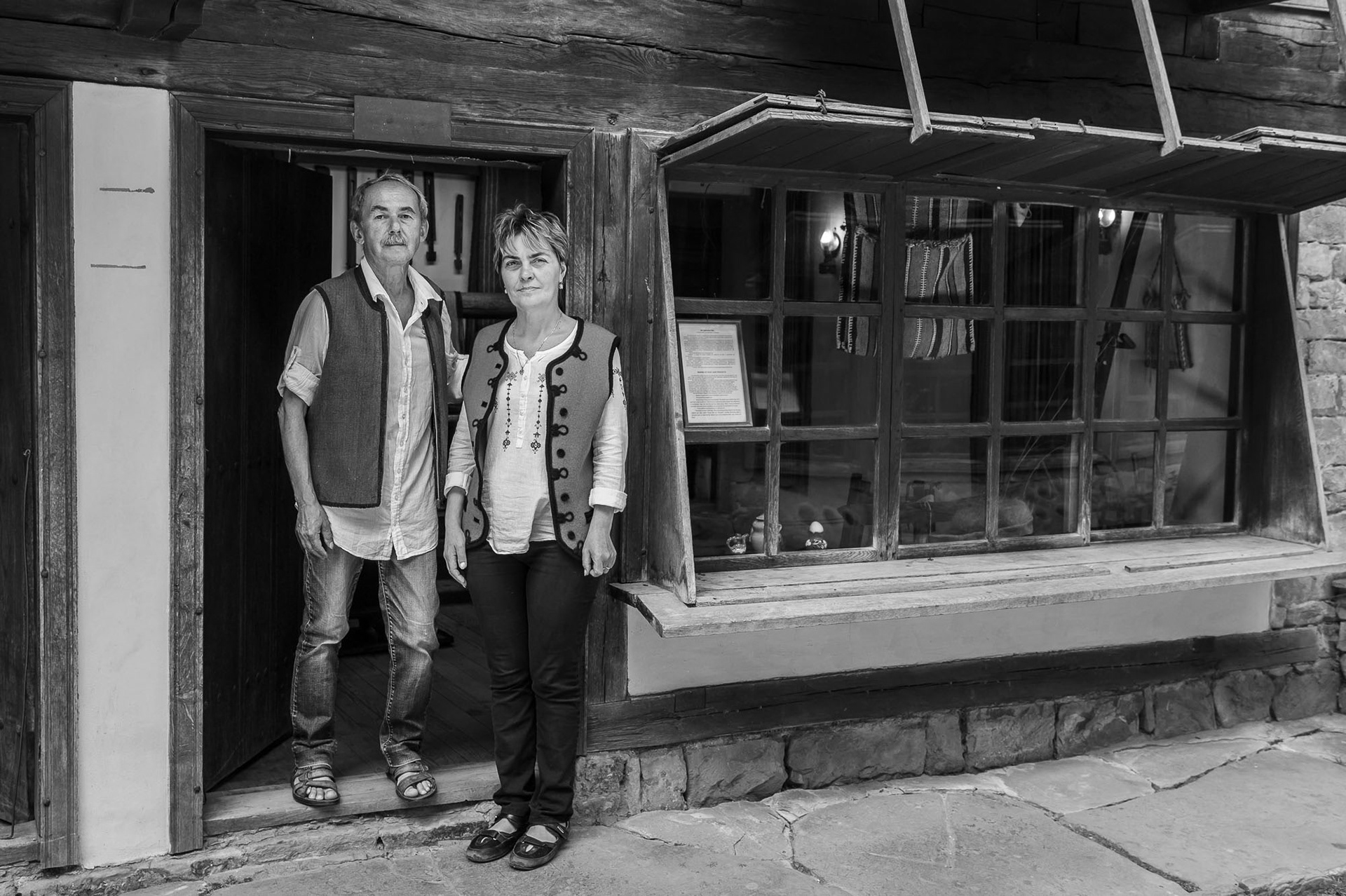
“I have been training my colleague for two years. I have already passed it on to her and she has mastered all the ins and outs of the craft.”
For the time being, the art of goat-hair working can only be observed in the workshop of Master Hristo Marinov at Etar Open-Air Museum which has an indisputable contribution to the preservation of this craft. The 67-year-old goat-hair craftsman is not the last practicing the trade, because he has trained his successors – all of them women in what has traditionally been an exclusively male occupation. The year 2022 marks 40 years since the then 27-year-old young man enrolled as an apprentice in this same workshop run by Master Lyubomir Bogdanov, who had trained with the most prominent among masters, the elder Filyo Ivanov. Shortly after he received his master’s certificate his teacher retired from the trade, so Hristo Marinov remained the only warden of the goat-hair workshop, and as years went by, the only keeper of the craft. Today there are already three of them including Milka Krasteva and Veylada Mutafchieva who works side by side with Master Marinov at the Etar Museum.
"I am lucky to have been in touch with the Revival era masters some of whom still practiced the craft way back, though well advanced in years."
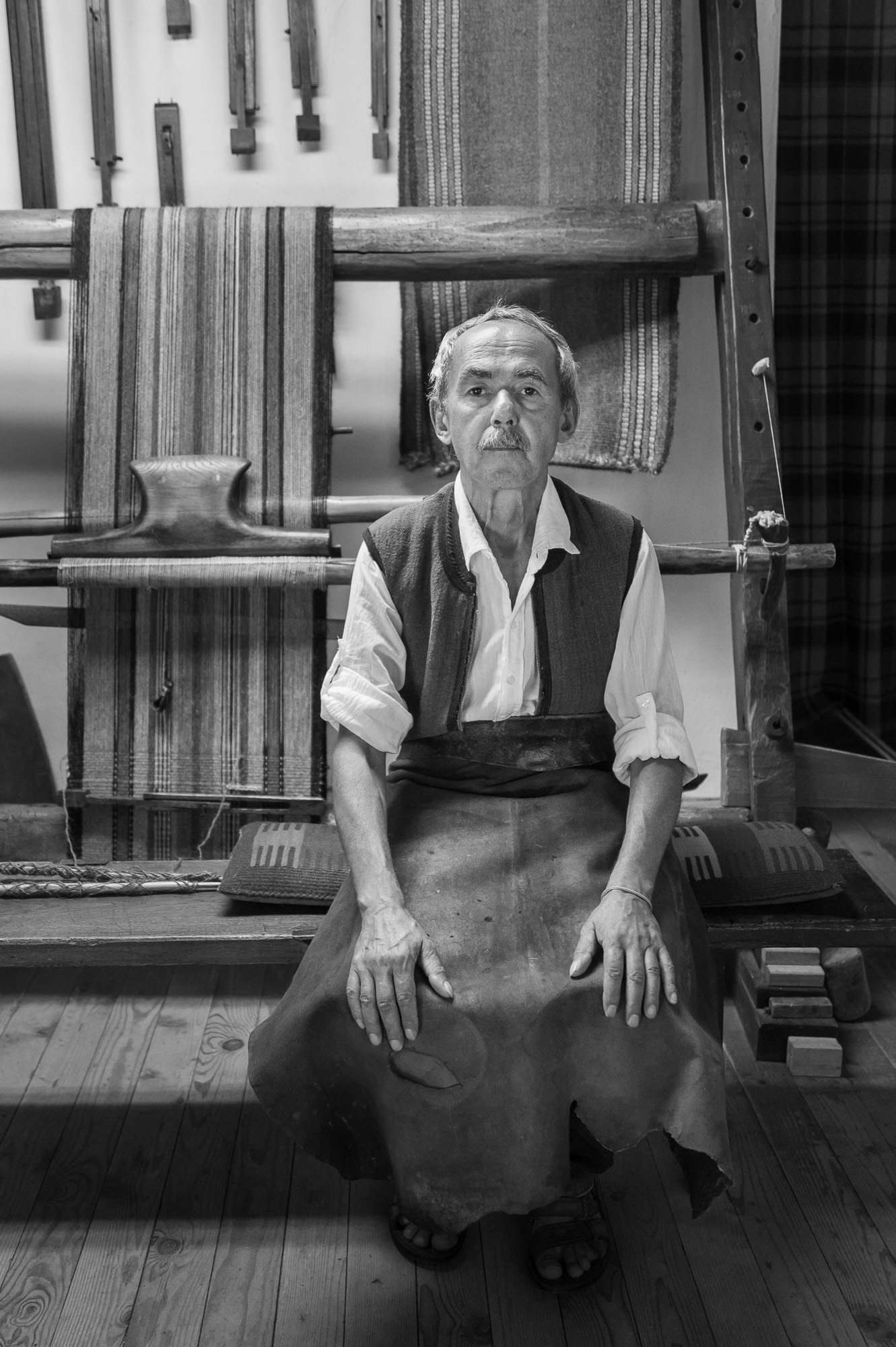
Explore additional material about Hristo Marinov's story on the pages of Eight printed magazine (February 2023)
PROJECT
Crafted by Hand. Photo Diary (2022)
IDEA & PHOTOGRAPHY
Rosina Pencheva
TEXT
Maria Boncheva
CRAFTS CONSULTANCY
Rositsa Bineva
GRAPHIC DESIGN
Kostadin Kokalanov
TRANSLATION
Daniela Konstantinova
COMMUNICATIONS
Maya Ivanova
DIGITAL CONTENT
Rosina Pencheva
Denislava Dikova (assistant)
PRODUCTION
PARTNERSHIP
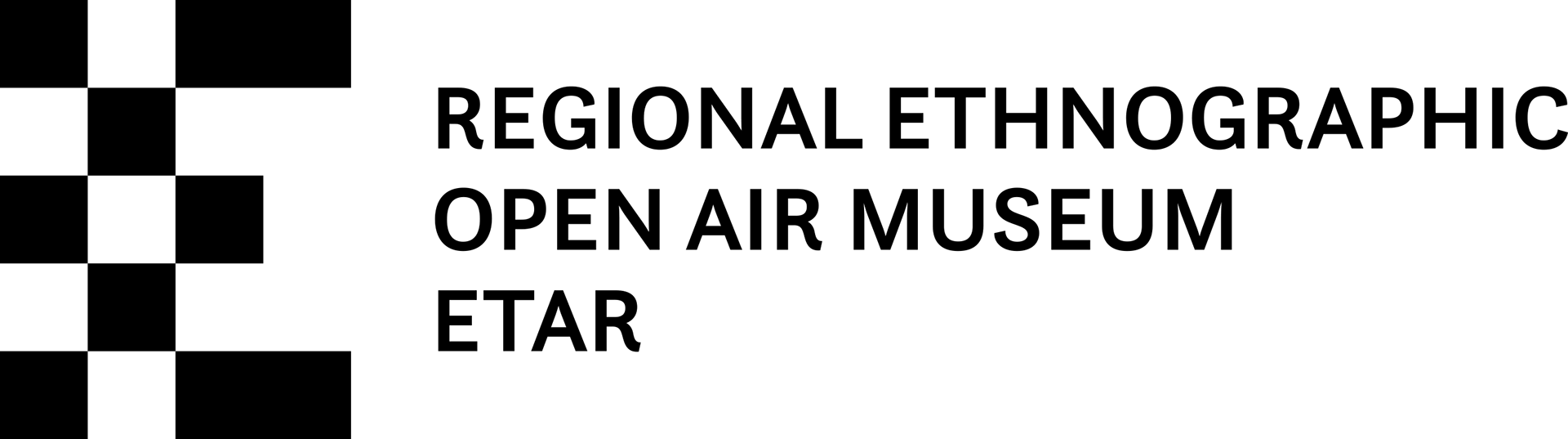
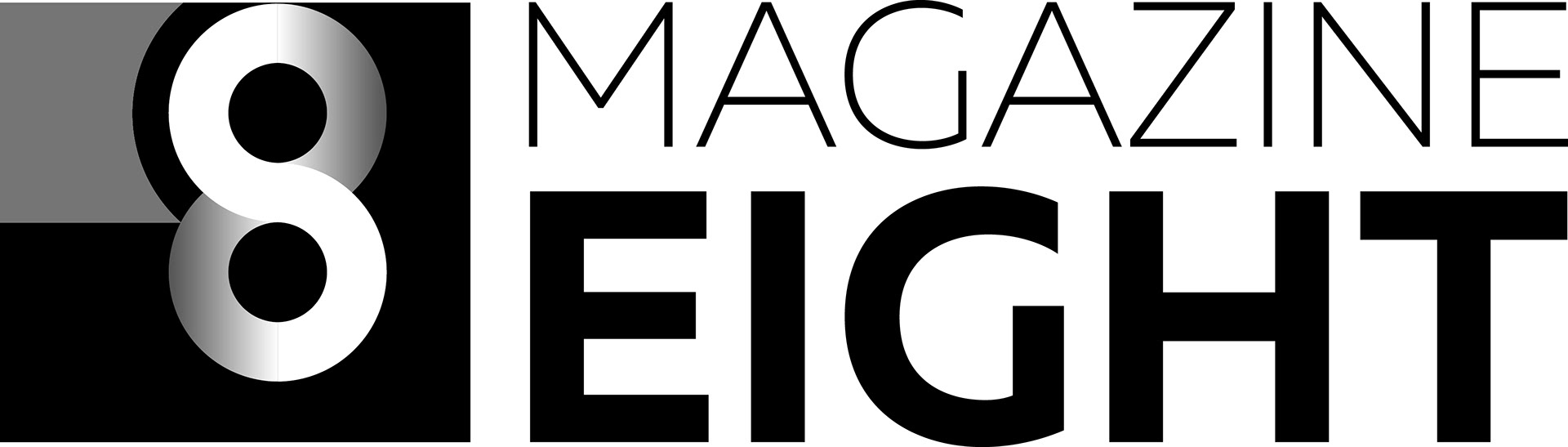
CO-FUNDING
2022 Culture Program, Gabrovo Municipality