Published: 05.12.2022
Creative concept and photography: Rosina Pencheva
Text: Maria Boncheva
Creative concept and photography: Rosina Pencheva
Text: Maria Boncheva
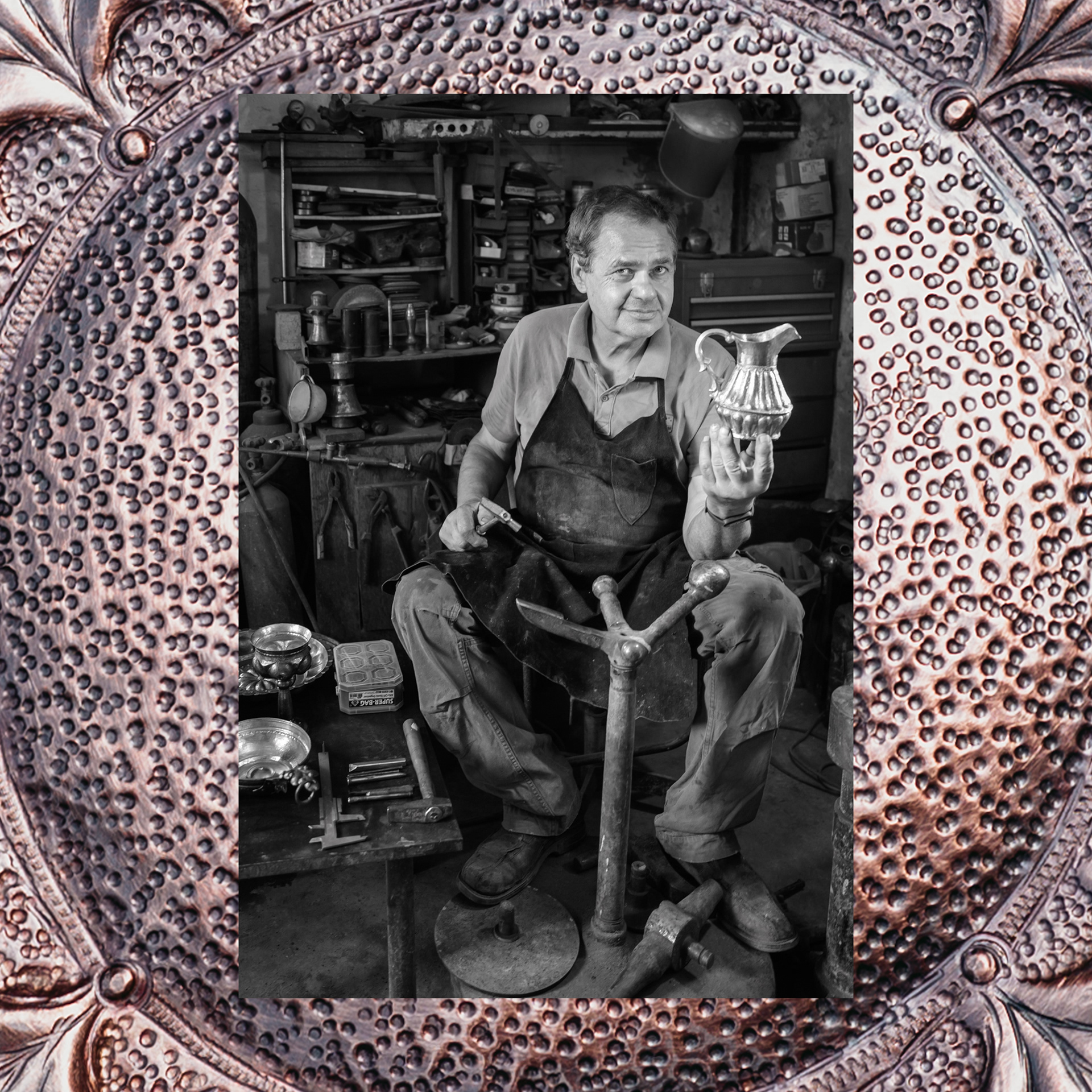
His works were shown in Paris (at the Louvre), in Tokyo and at a series of other exhibitions and competitions across the world.
Аwarded with the title “usta” or “true master”.
An introducer of innovations to both the decoration of copperware and the optimization of tools.
Coppersmith’s trade is one of the most ancient handicrafts in the Bulgarian lands – the Thracians used to be skillful masters of processing precious metals, including copper. Due to its wide range of applications in day-to-day living, it continued to thrive during the First and the Second Bulgarian kingdoms and did not stop during the Ottoman yoke. Copper was the material to make most of the household vessels: coppers, cauldrons, pots, various kinds of bowls, baking dishes and tins, pans, coffeepots, cups, pitchers, jugs, church bowls, baptismal fonts, trays, fire-pans, spoons, etc.
Prior to the Liberation, a few well-established Bulgarian coppersmith centers thrived including Stara Zagora, Veliko Tarnovo, Kazanlak, Troyan, Asenovgrad, etc. The craft lived its heyday in the 19th century. Coppersmithing suffered an obvious decline in the aftermath of the First World War, when tangibly cheaper goods started to be imported massively, and subsequently, as the production of aluminum, enameled and other vessels expanded. Today, the craft has lost its economic worth, except to some extent in the production of rakiya brandy cauldrons, coffeepots, and articles of artistic value. This decline has been prompted mainly by the high price of the raw materials, the long production time, as well as by the need of regular tinning for household use.
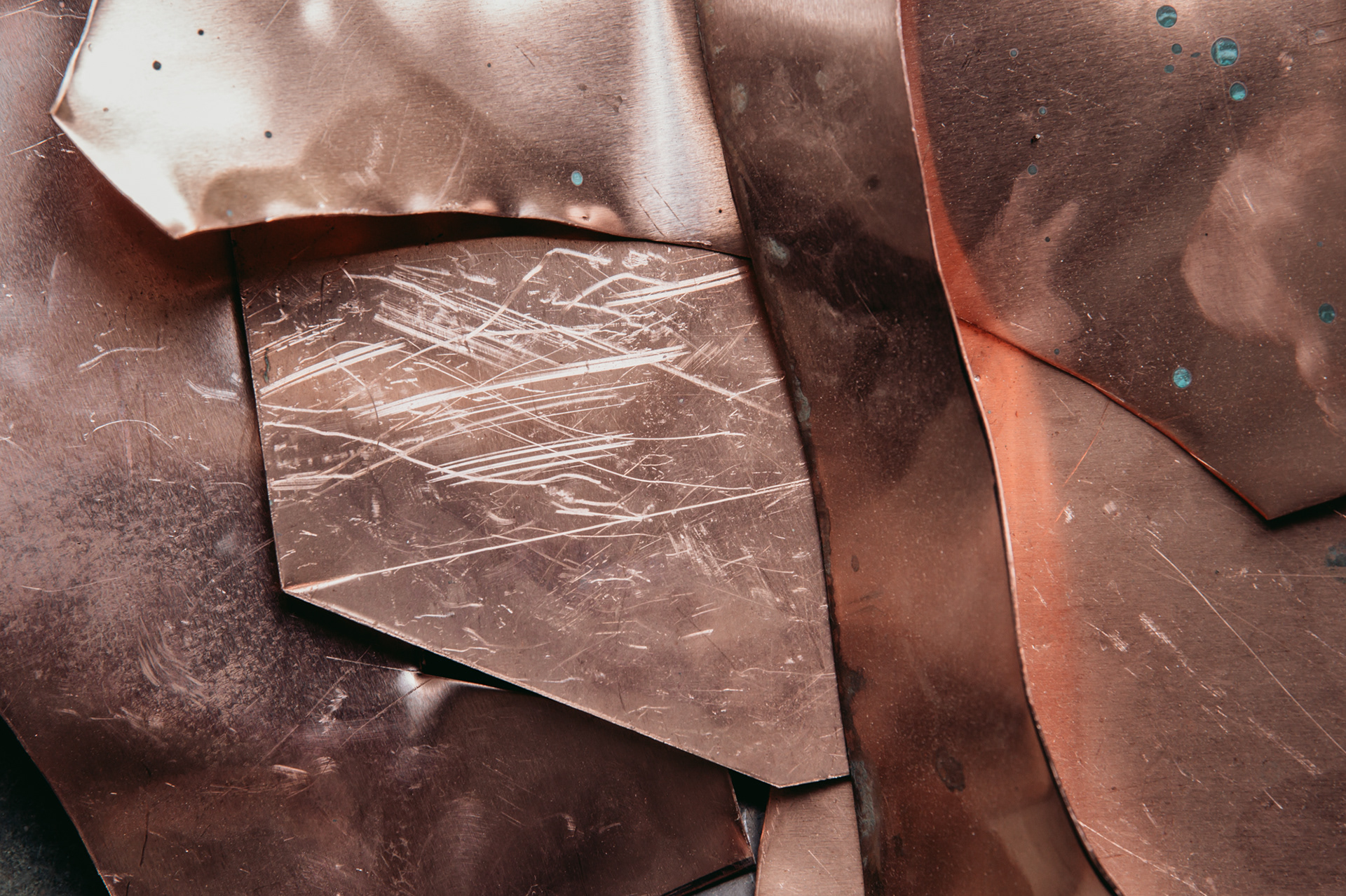
Scraps of copper sheets
Copper works by Petar Paunov
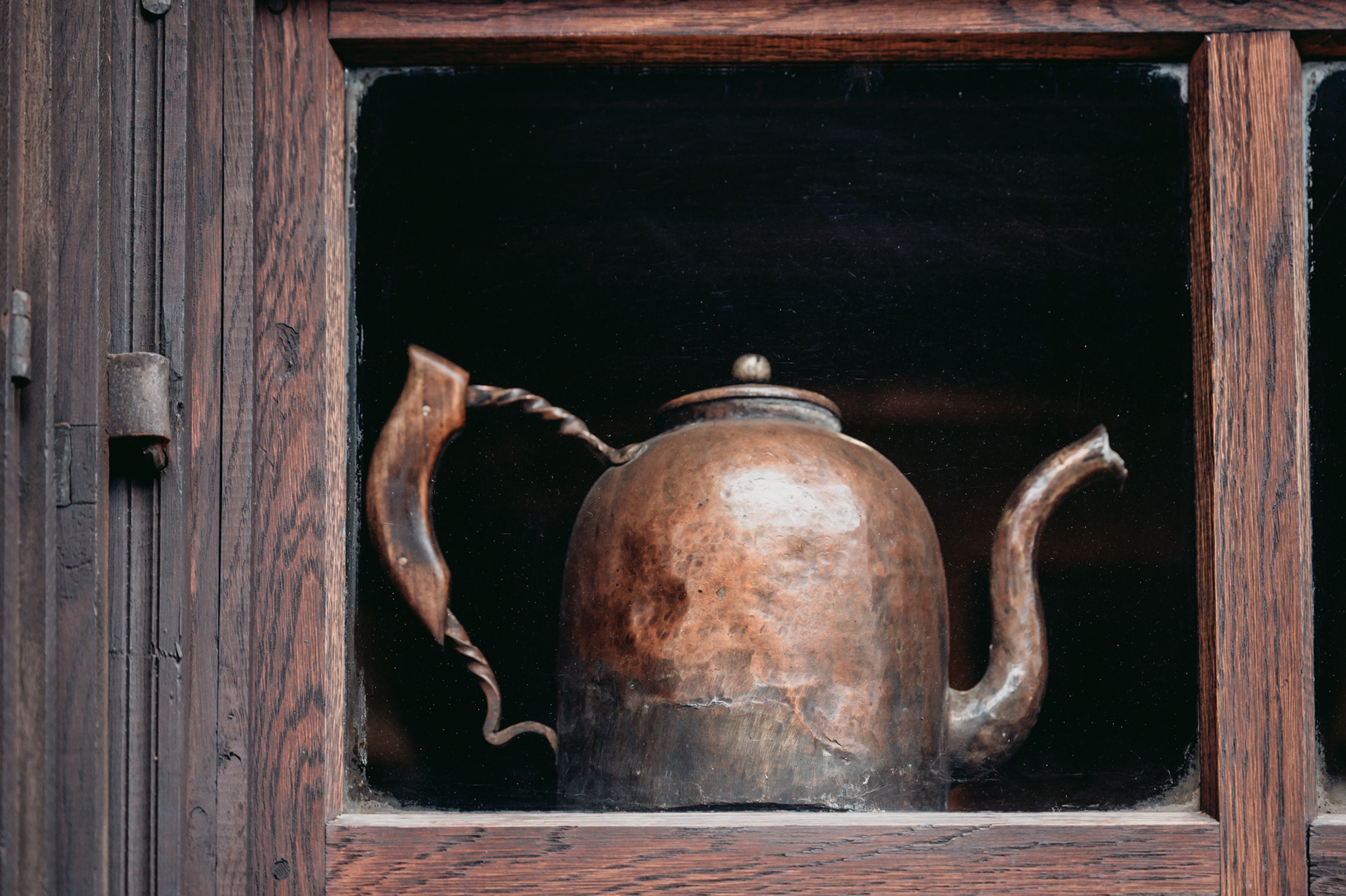
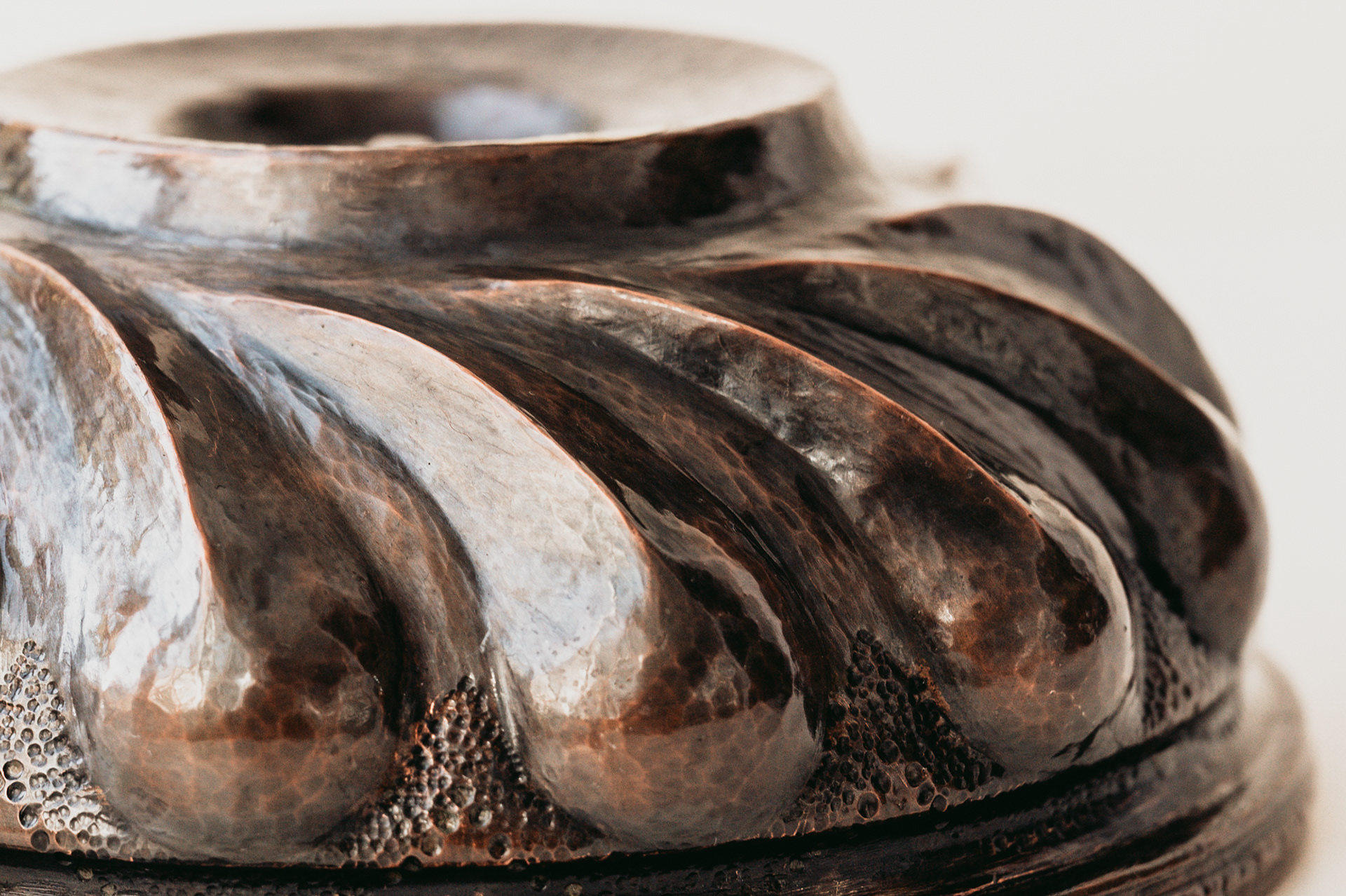
Detail of bowl (put upside-down)
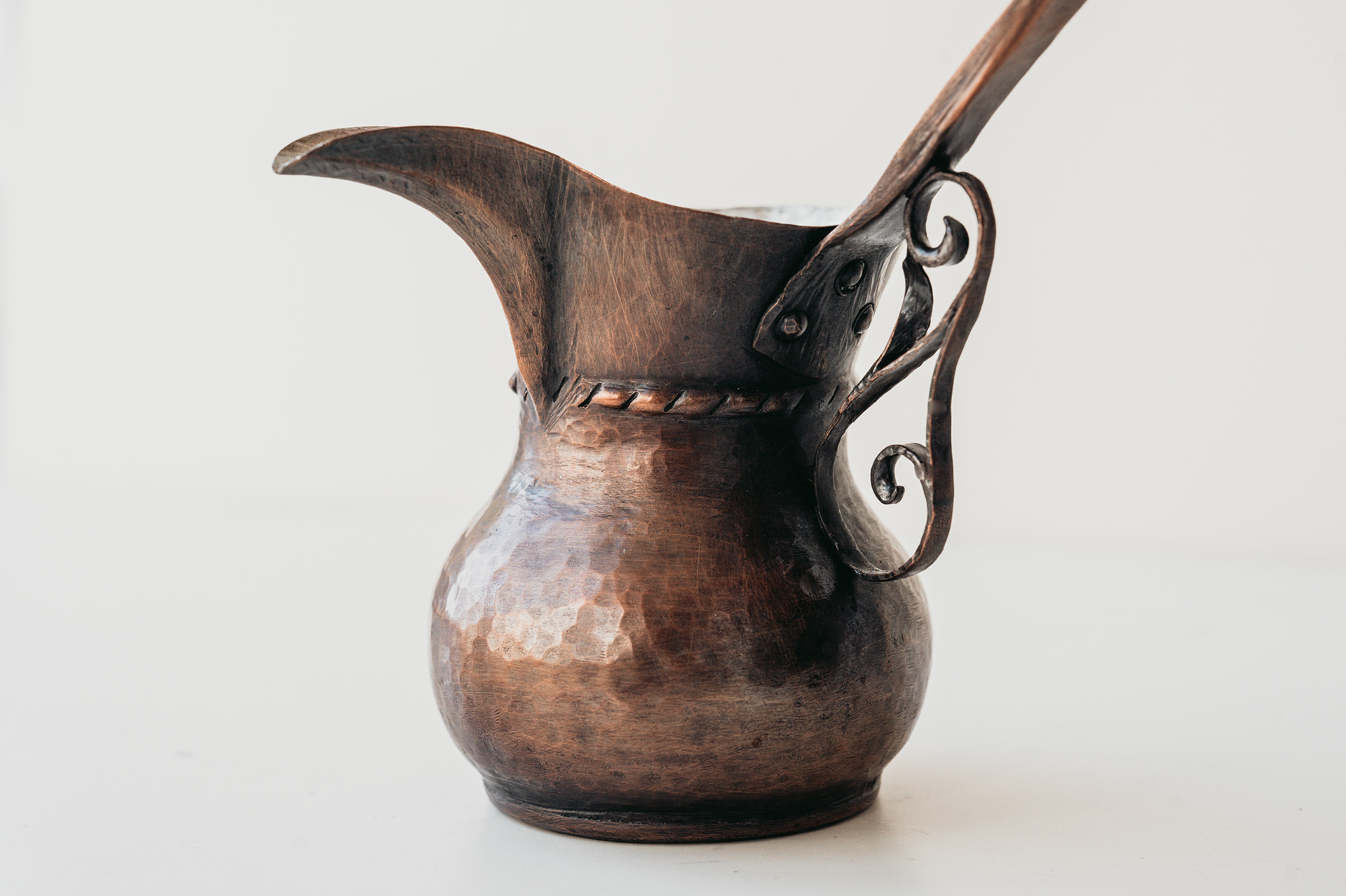
Detail of jug
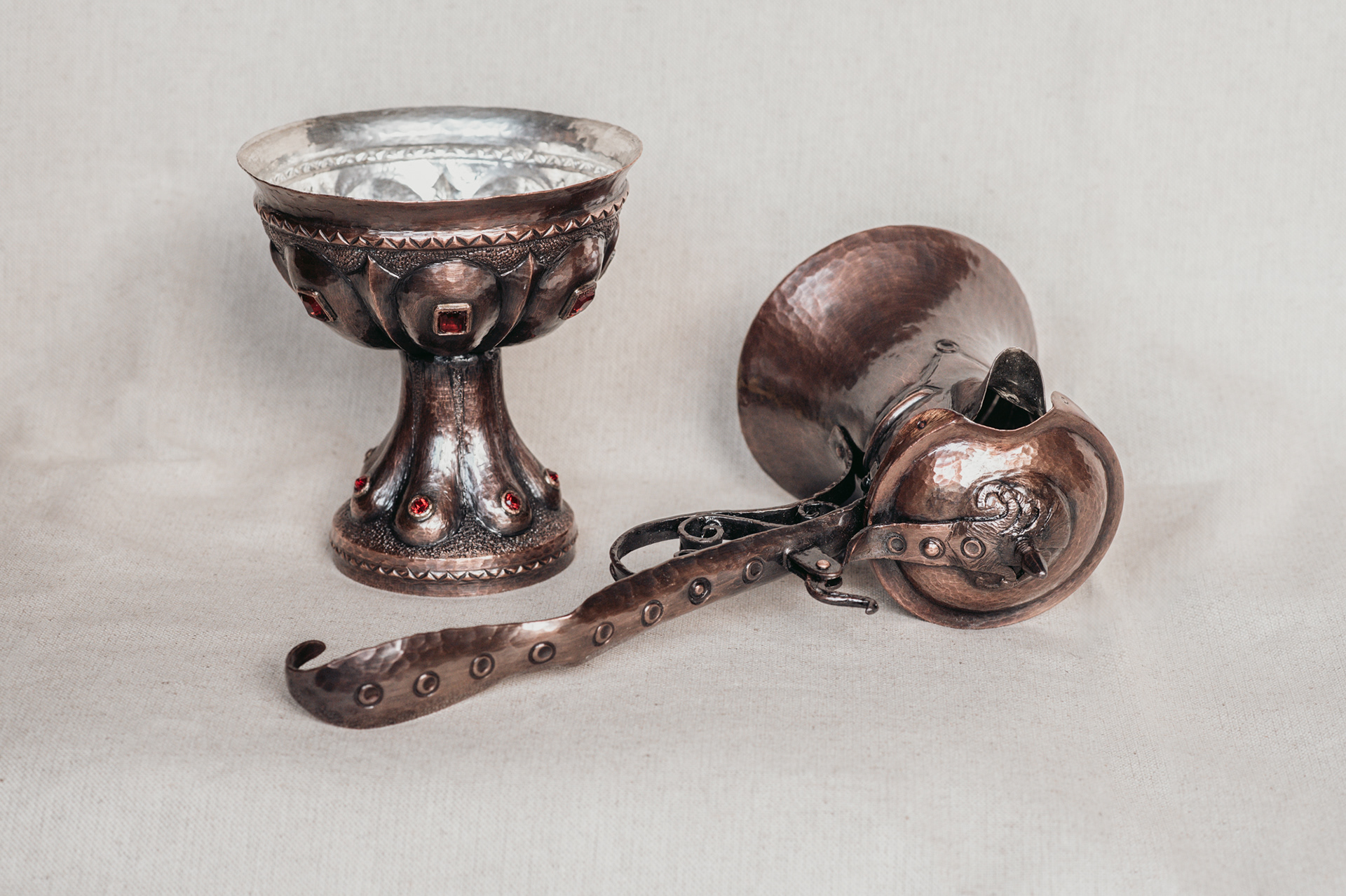
Cup and jug with lid
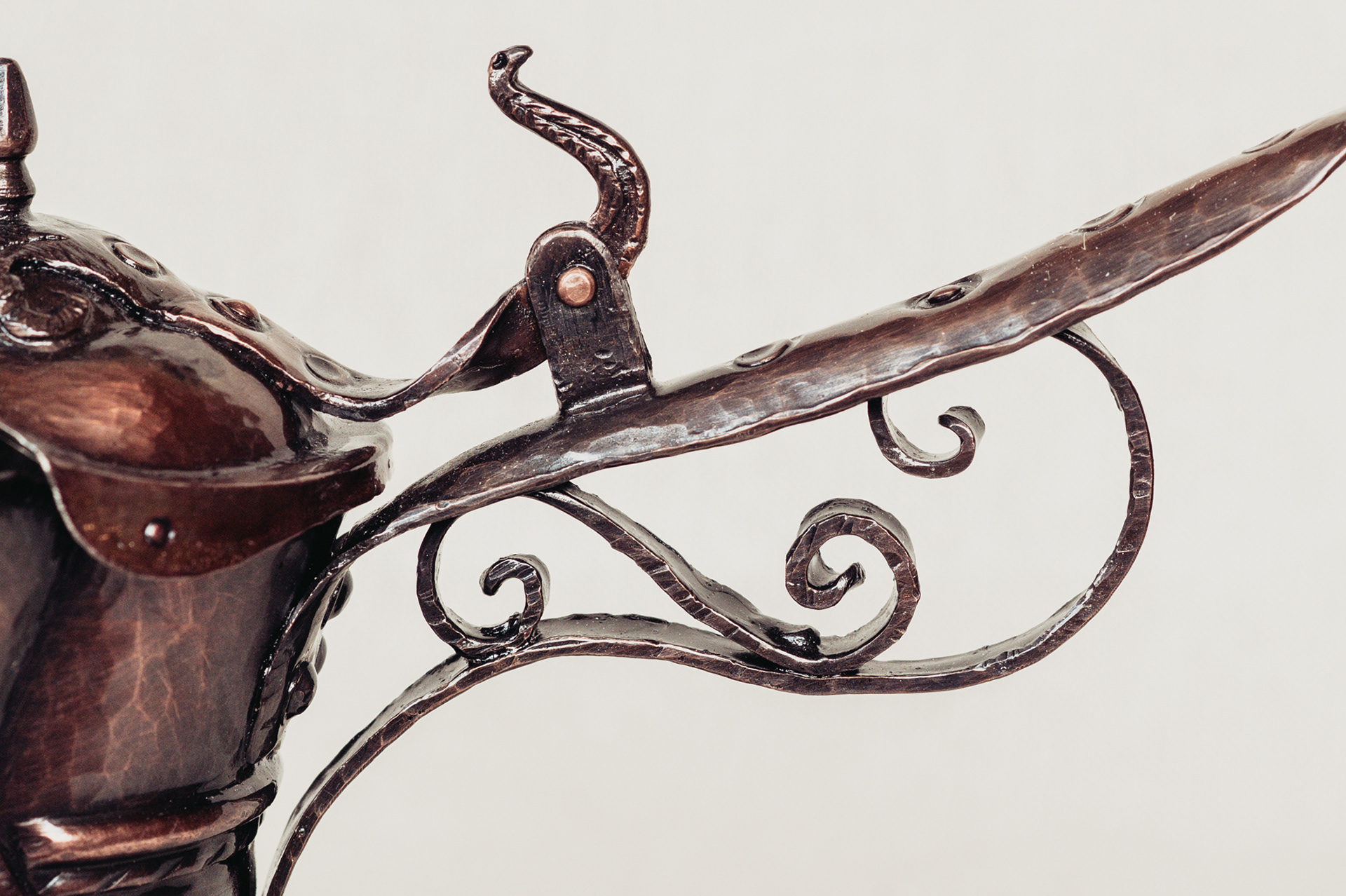
Detail of jug handle with lid
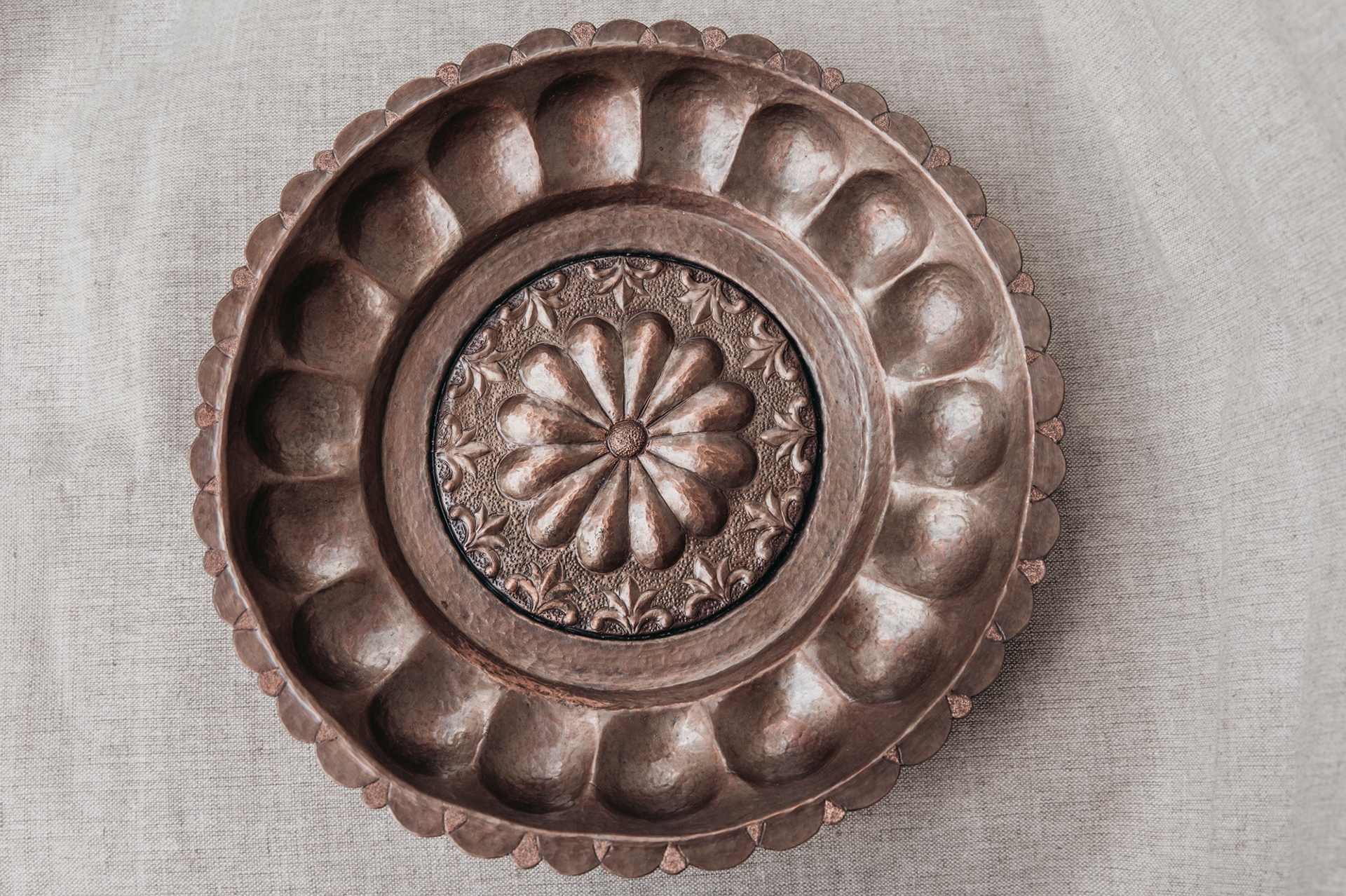
Bowl
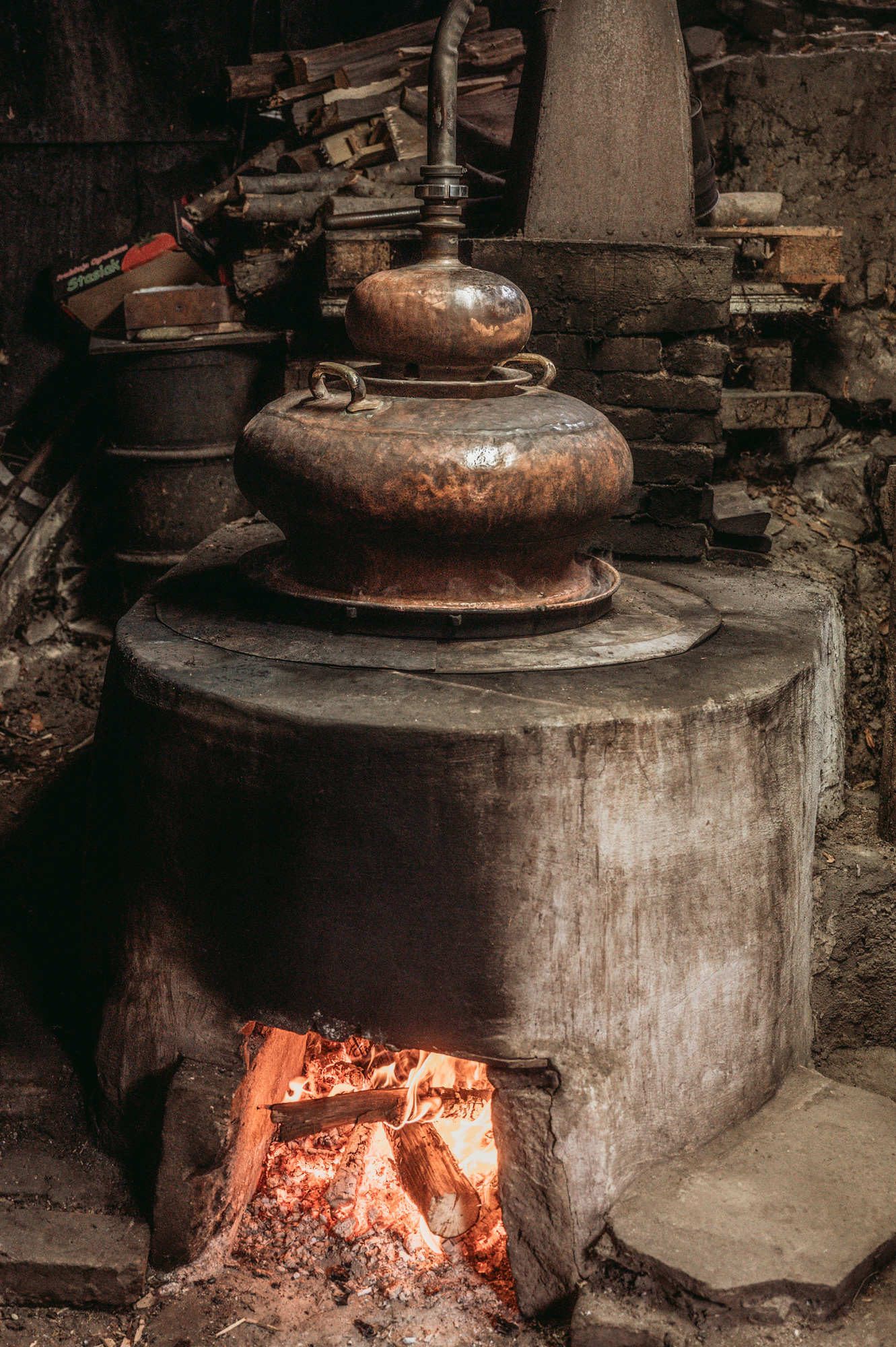
Working cauldron for Bulgarian rakiya (alcohol drink)
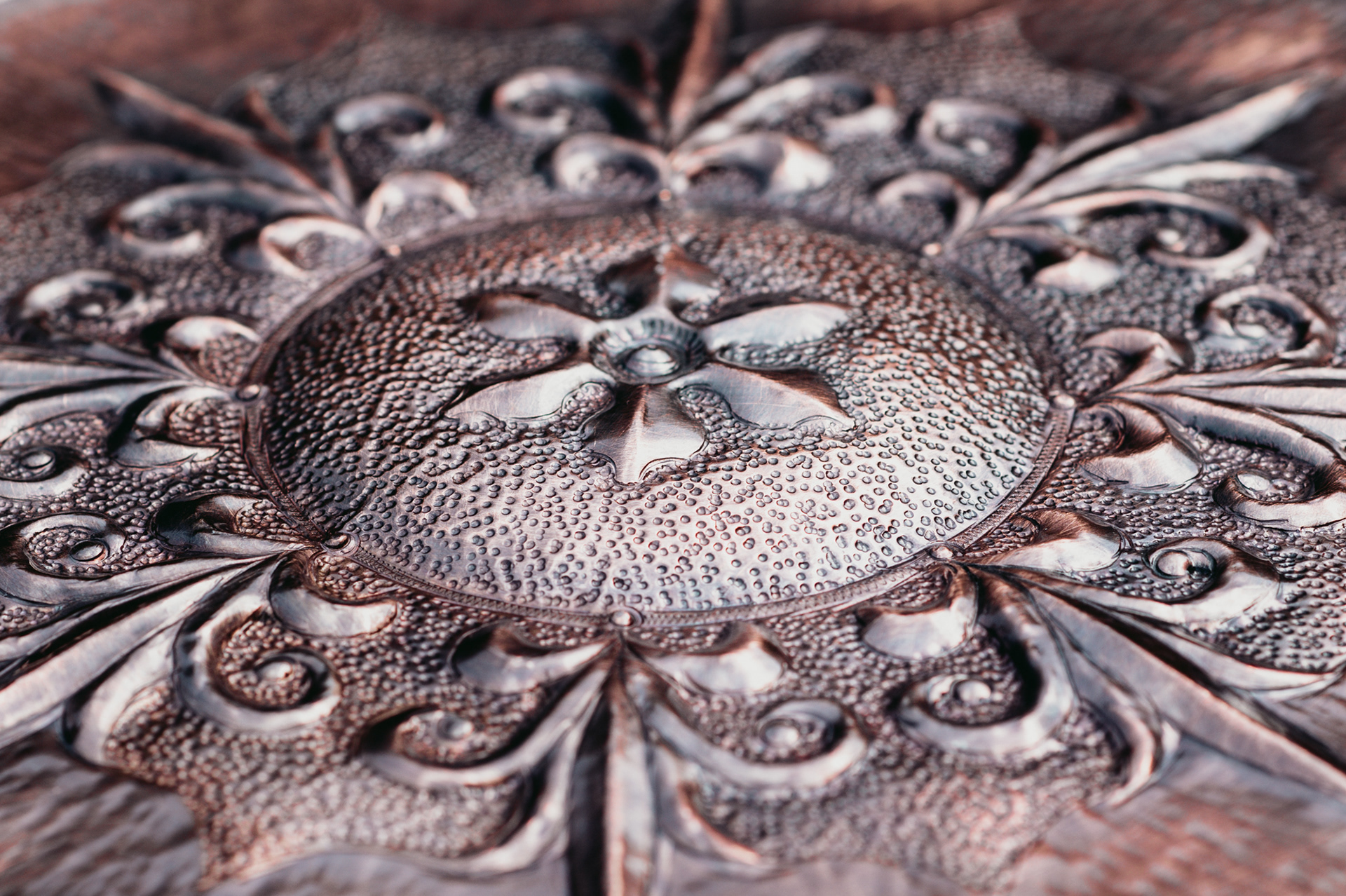
Since ancient times, copper goods have combined the practical application in everyday life with the artistic element of their decoration. It is exactly in making the decoration that the artisan demonstrates not only his imagination, but also the diversity of techniques that he masters, such as smith and impression-die forging, fretwork, acid etching, burin engraving, etc., while at the same time creating artistic value. Today, there are only few people who are initiated into the secrets and subtleties of coppersmithing in this country, and those who actively practice it can be counted on the finger-tips of the two hands.
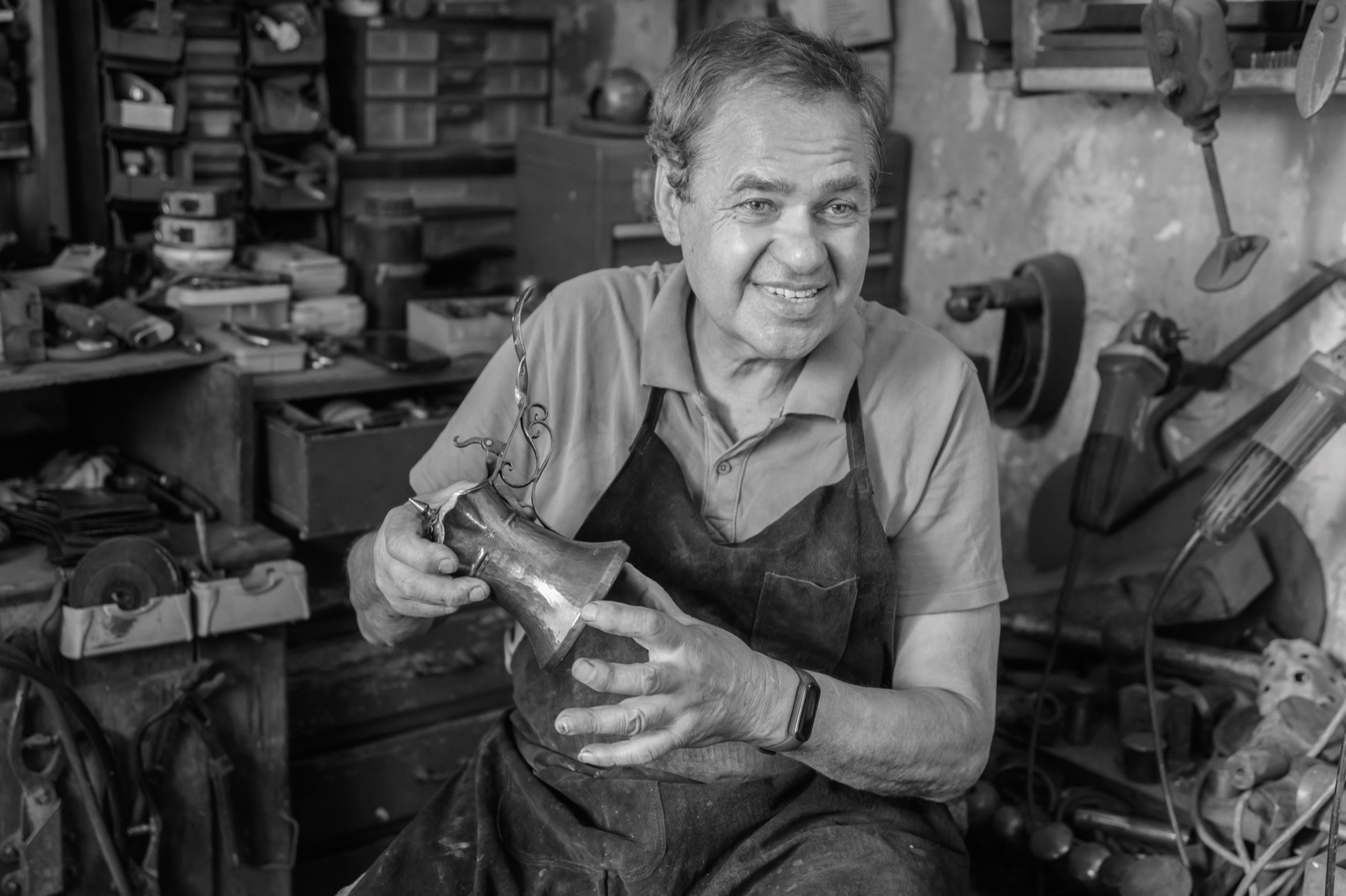
Aged 73 and sporting a spirit, mind and creative charge of a young man, Master Usta Petar Paunov, born in the village of Vardim, Svishtov region, is one of the luminaries of his craft in this country. He is one of those endowed with a rare gift – possessing both accurate engineering thinking and artistic talent. Master Paunov distinguished himself with special skills already in his first professional field – tool fitting. Upon graduating from the Mechanical Engineering School in Gabrovo, he was one of three graduates who were awarded the 5th professional rank instead of the common 4th rank. This was followed by 14 years of full-time work at the electric hoist plant in Gabrovo, where he once again stood out among his colleagues with his skillfulness. There he mastered the use of all types of metal-cutting tools, and thanks to this experience, subsequently introduced improvements to the toolkit of coppersmithing.
My apprentice from Rousse Ventsi would tell me: “Master, isn’t it time for you to retire? You’re 73 already! The moment we’re about to catch up with you, you suddenly take off again.”
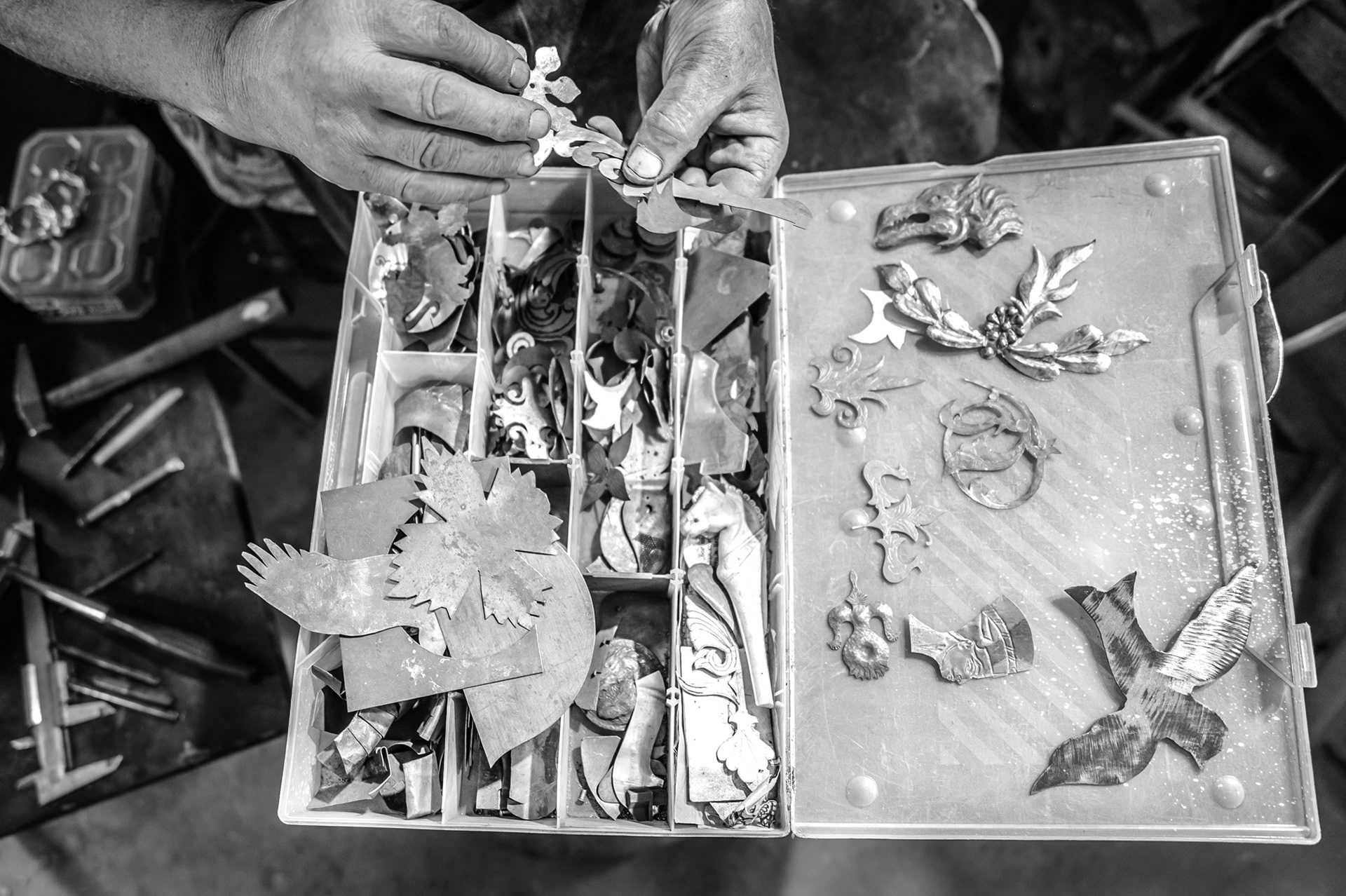
Copper foil stencils for decorative figurines. The next stage is hammering the relief.
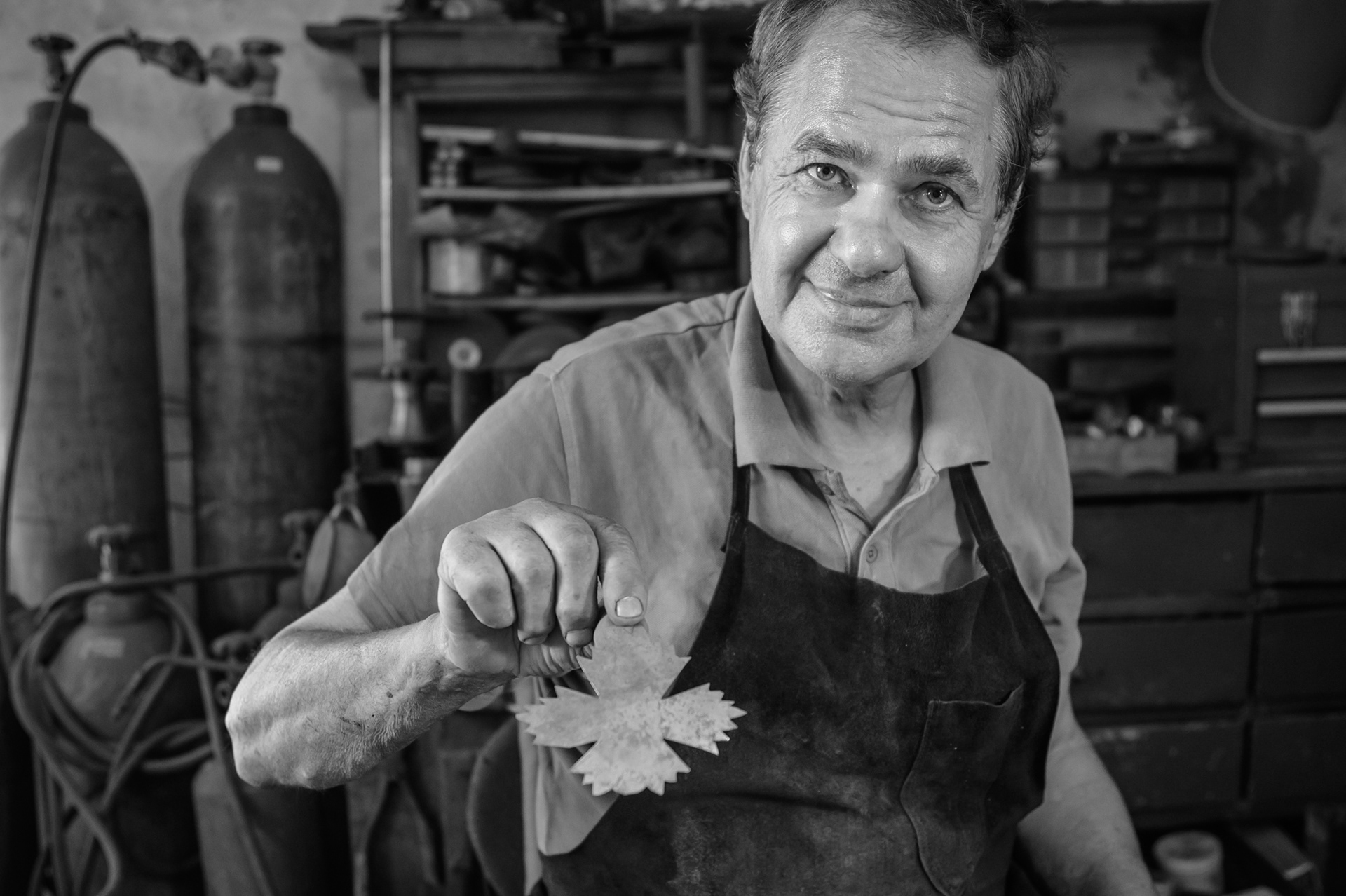
A vine leaf shape cut from a copper sheet for appliqué – the same model as the one that Paunov drew for the commission in the Etar Museum. The next stage is engraving.
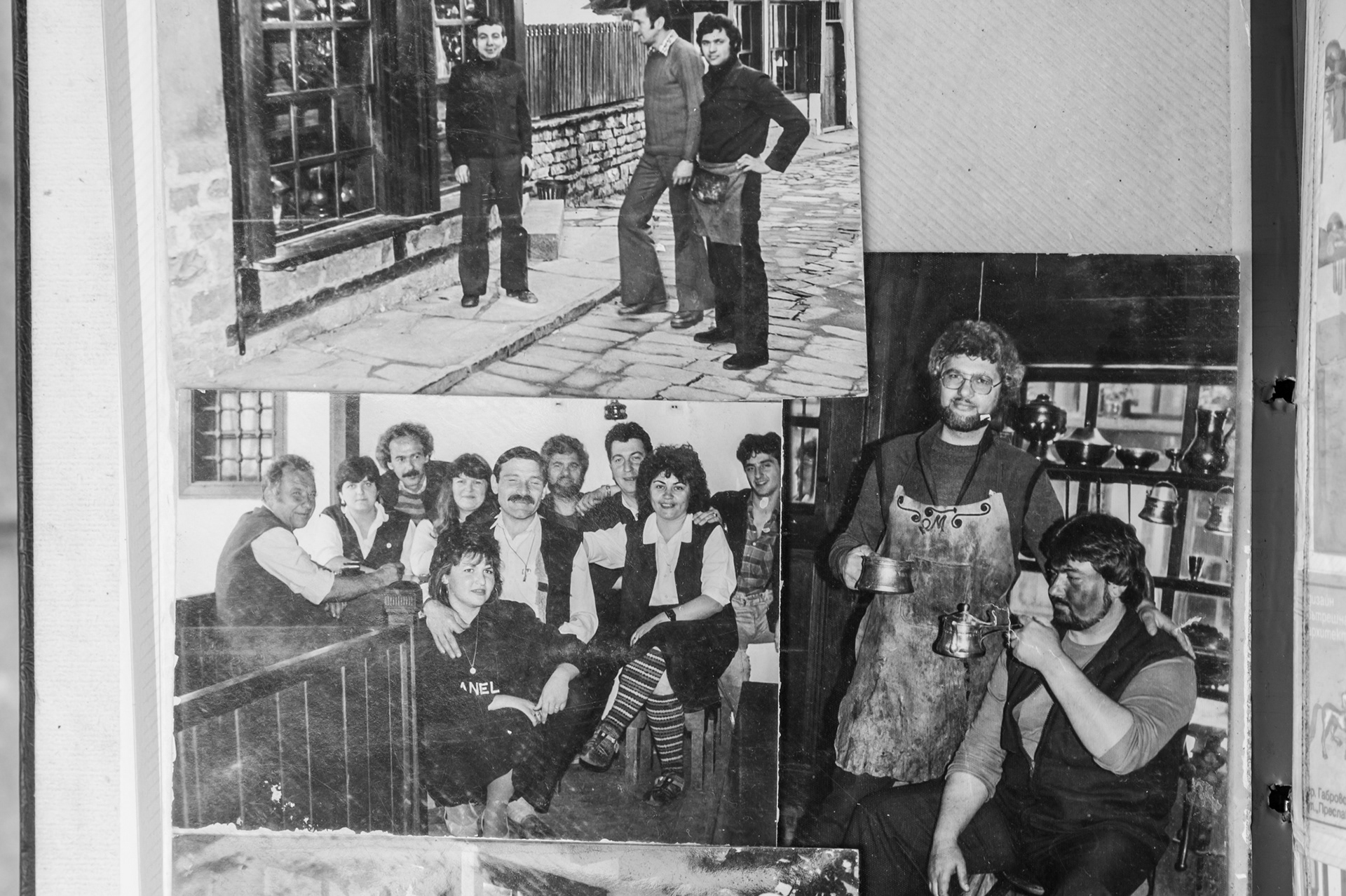
Photographs from Paunov's archival photo album showing his colleagues in the coppersmith's workshop and the masters in Etar Museum, 1980s
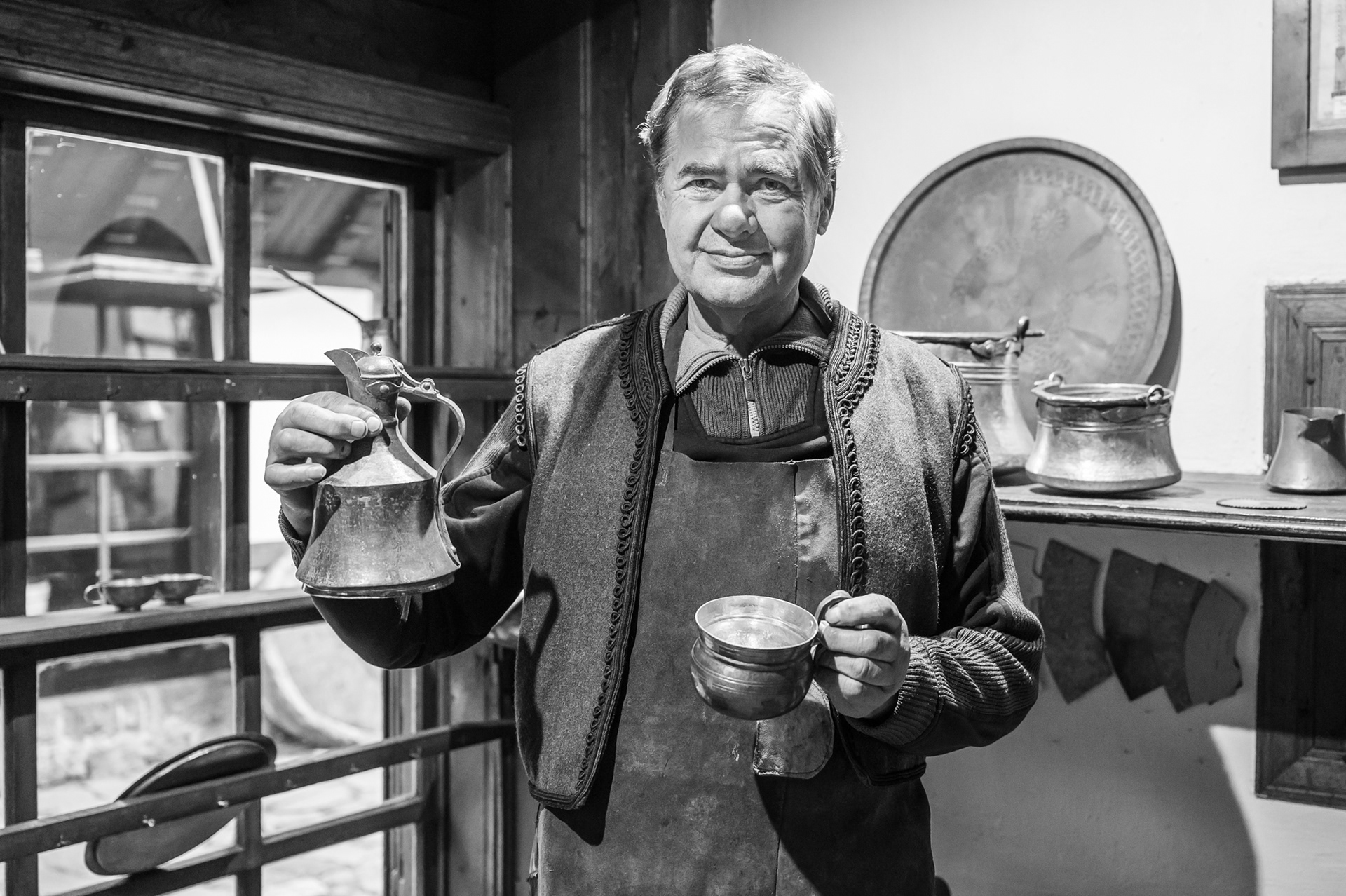
With two of his works, which now are part of the Etar museum's Coppersmith workshop exposition of the craft
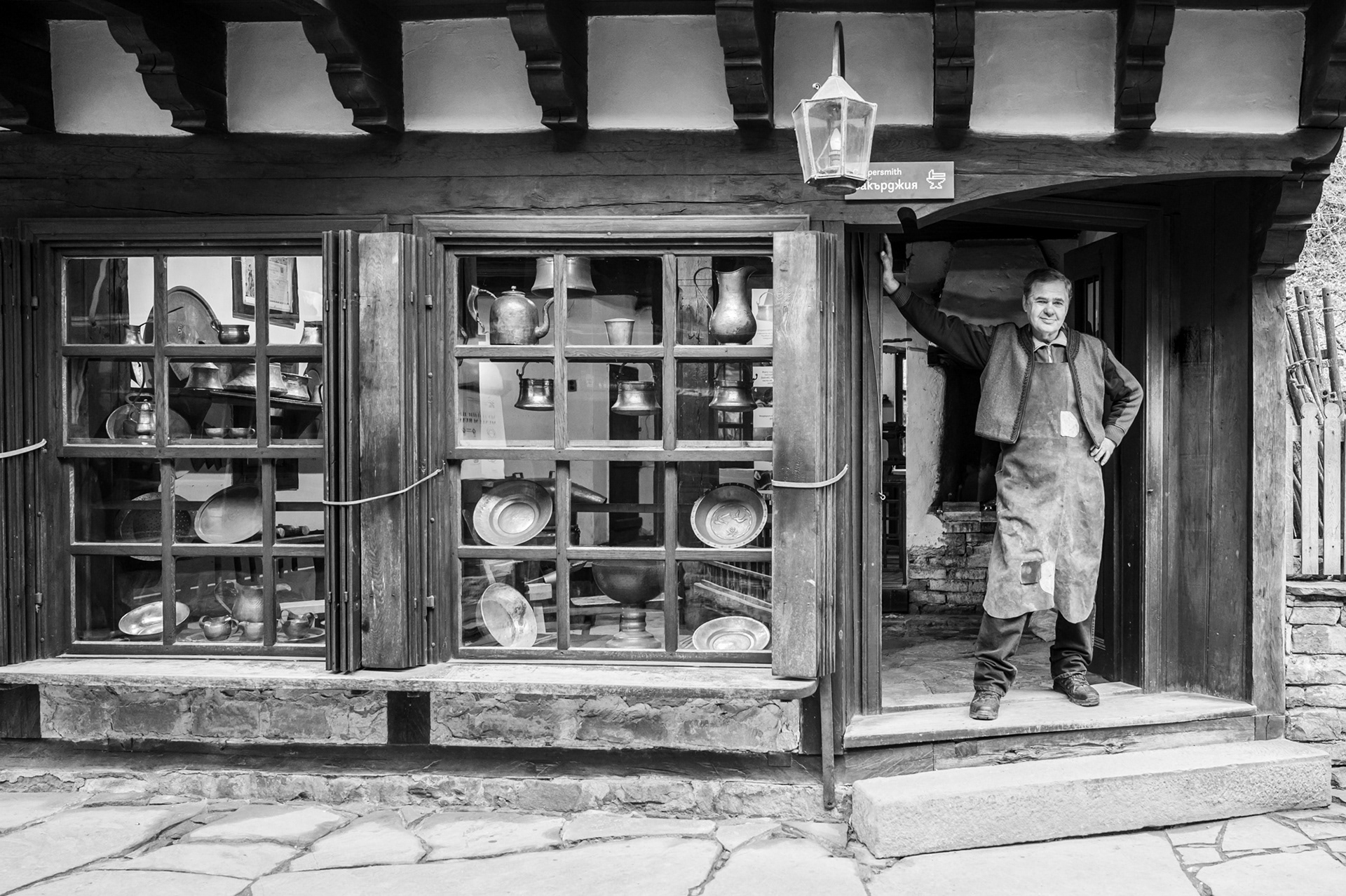
In front of the Coppersmith Workshop of the Crafts street in the Etar Museum, where Paunov worked from 1980 to 1994
In 1980, chance took him to the craft: during a break, he sketched a knight from a panel that sculptor Ivan Donkov, the son of the founder of the Etar Museum, was crafting at the factory. The artist noticed the boy's talent and told him to go to Etar, where there were openings for apprentice coppersmiths. Petar Paunov did what he was told. By the irony of fate, Lazar Donkov himself was at the coppersmith's workshop with the old master Goodman Stefan (Stefan Yonkov Valev), when the young man turned up on the doorstep looking for his vocation. Without knowing the two men, he explained who was sending him and why. He was asked to draw something and he quickly sketched a vine leaf with his pencil. They asked him if he could also engrave it. "Just give me a burin", replied Petar Paunov, and he thus won an apprenticeship with Goodman Stefan due to his technical literacy.
Once again, at this stage of his training, Petar Paunov stood out for his dexterity and skill – in only six months he was promoted to the rank of senior apprentice and a year later defended his master's certificate, which usually would take as long as three years of training.
While I was working for the sheikh in the Persian Gulf, I trained other Bulgarians. Two of them moved away to set up an independent workshop. I was happy to have competition, motivation and diversity.
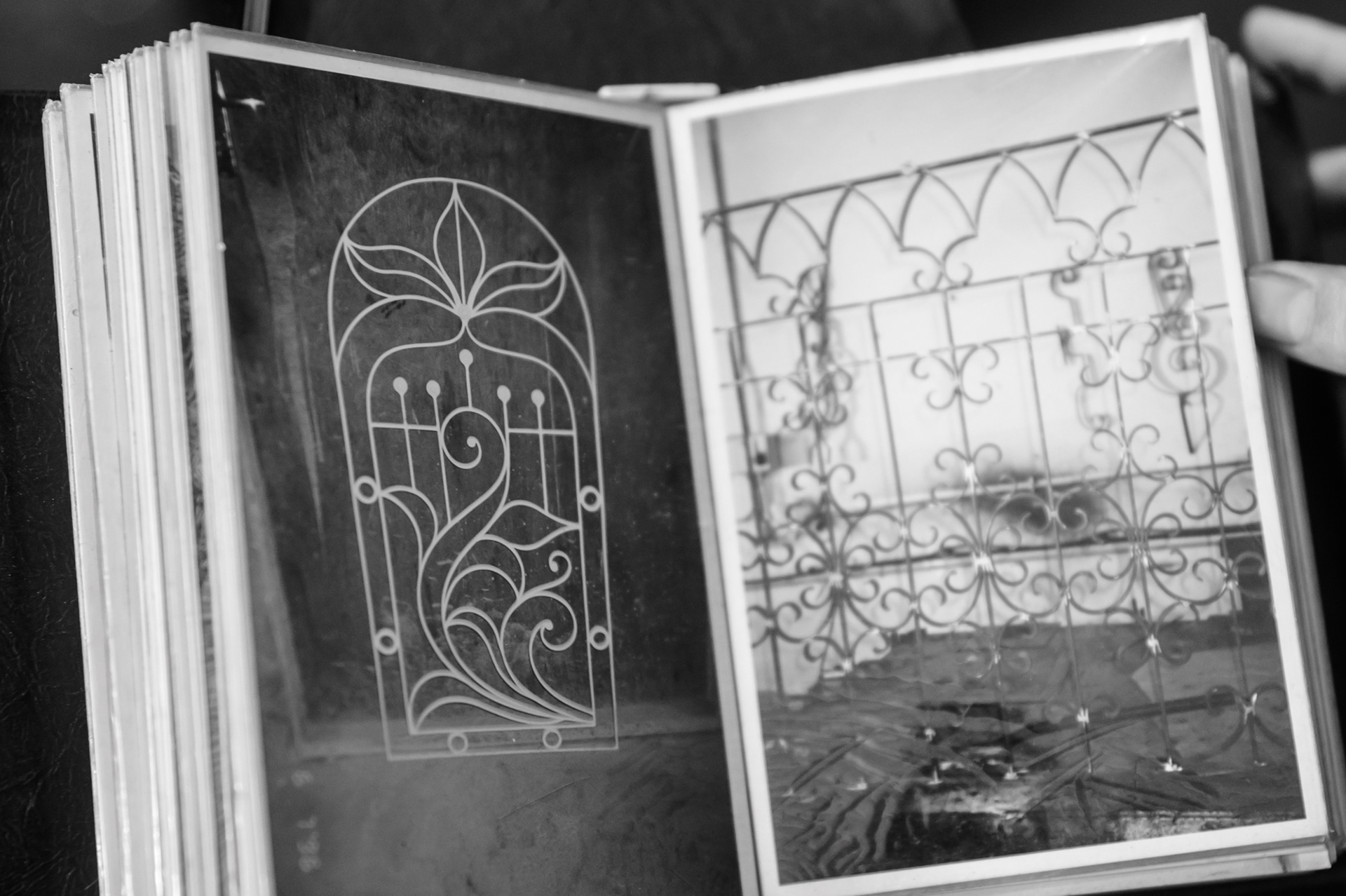
Fences – archival photo album of photos from Paunov's work in the Persian Gulf
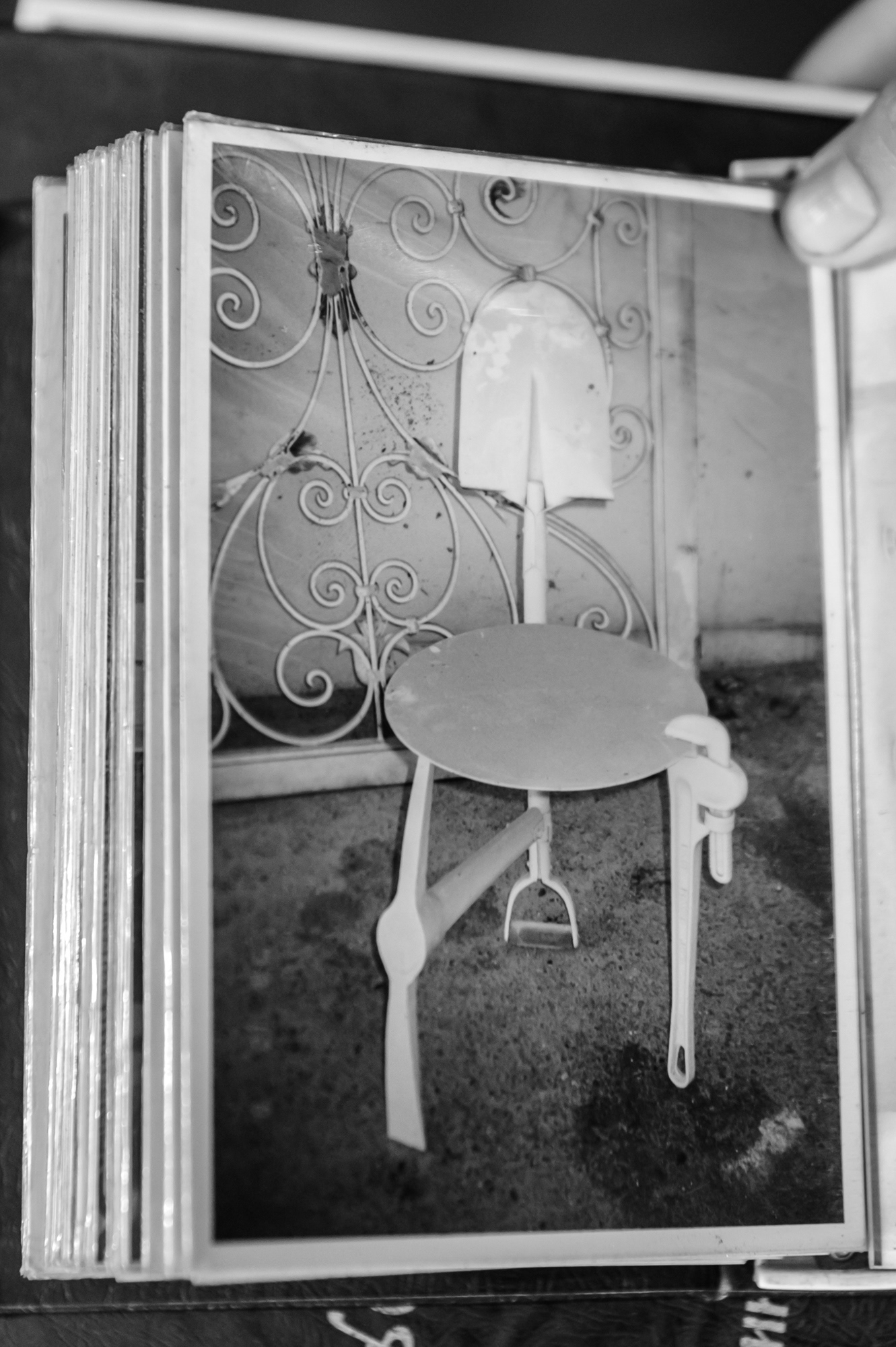
Chair, interpretation of tools
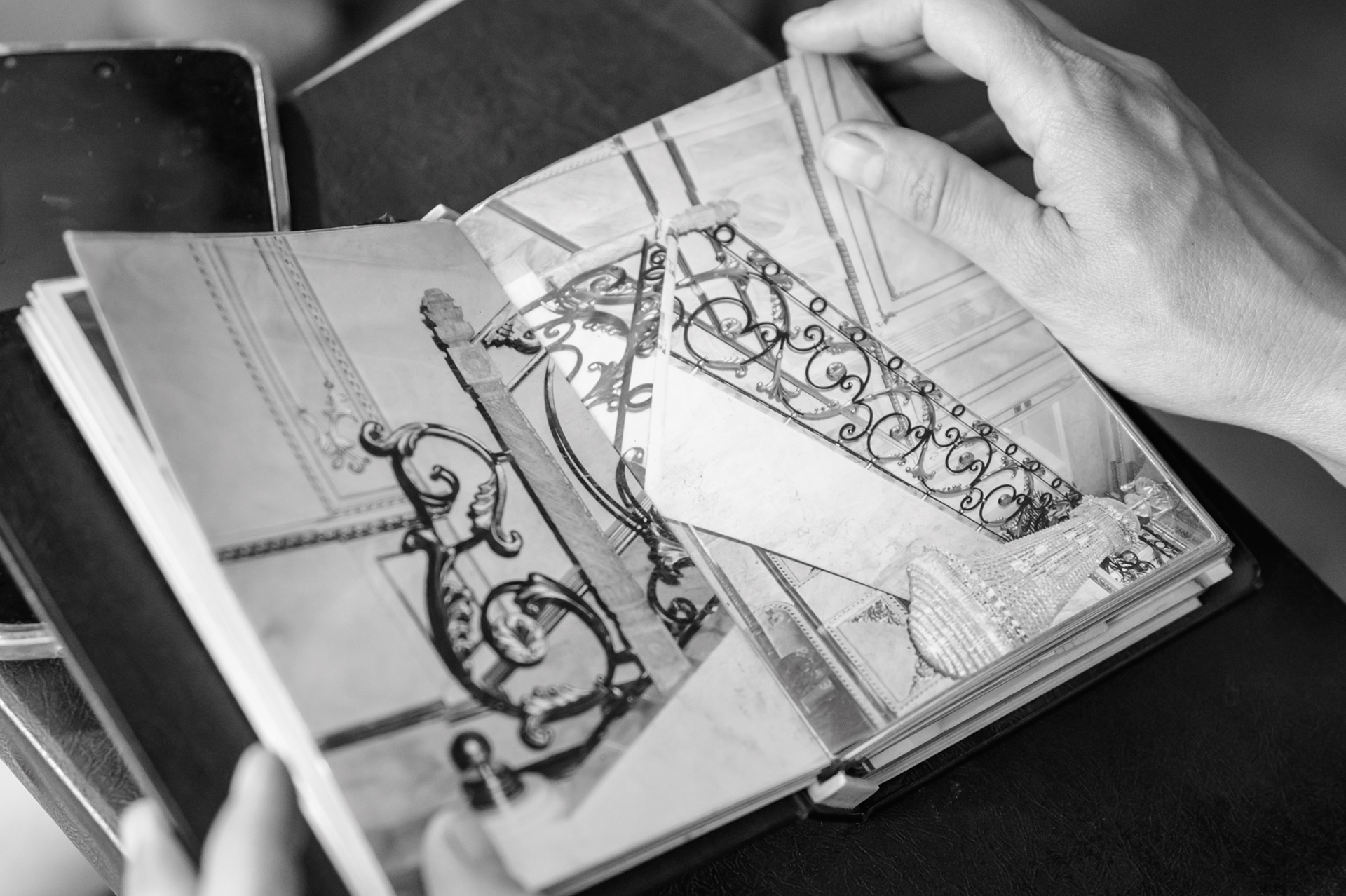
Wrought Iron Stair Railing and Brass Applique, Qatar
He remained at Etar for 14 years, until 1994. He then moved to the Persian Gulf for five years at the invitation of a local sheikh to work for him mainly in wrought iron which the craftsman had been mastering since the age of 16. On the spot Paunov fully equipped a wrought-iron workshop, trained 80 people from various nationalities – Bulgarians, Arabs, Filipinos, Indonesians, etc. in foundry, wrought iron, welding, gilding, etc., and designed original layouts for all possible interior elements – doors, railings, chandeliers, bedrooms, tables, chairs, doors, etc.
Upon his return in 2000, he continued his activity as a coppersmith, already independently, as a craftsman registered with the Artisan Cooperative. He designs objects traditional for the craft – from coppers to brandy cauldrons, originally designed articles of high artistic value, replicas of Thracian treasures.
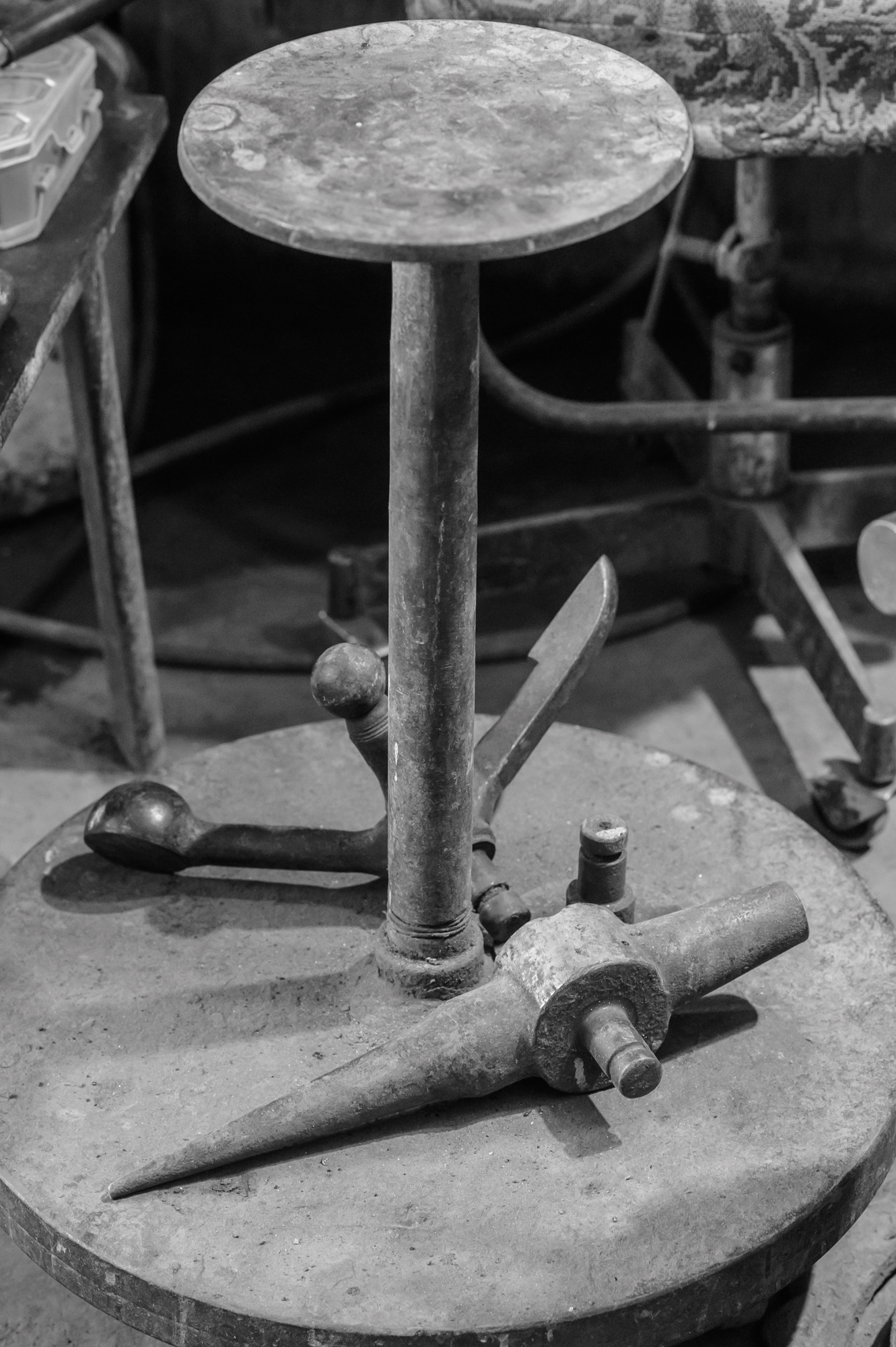
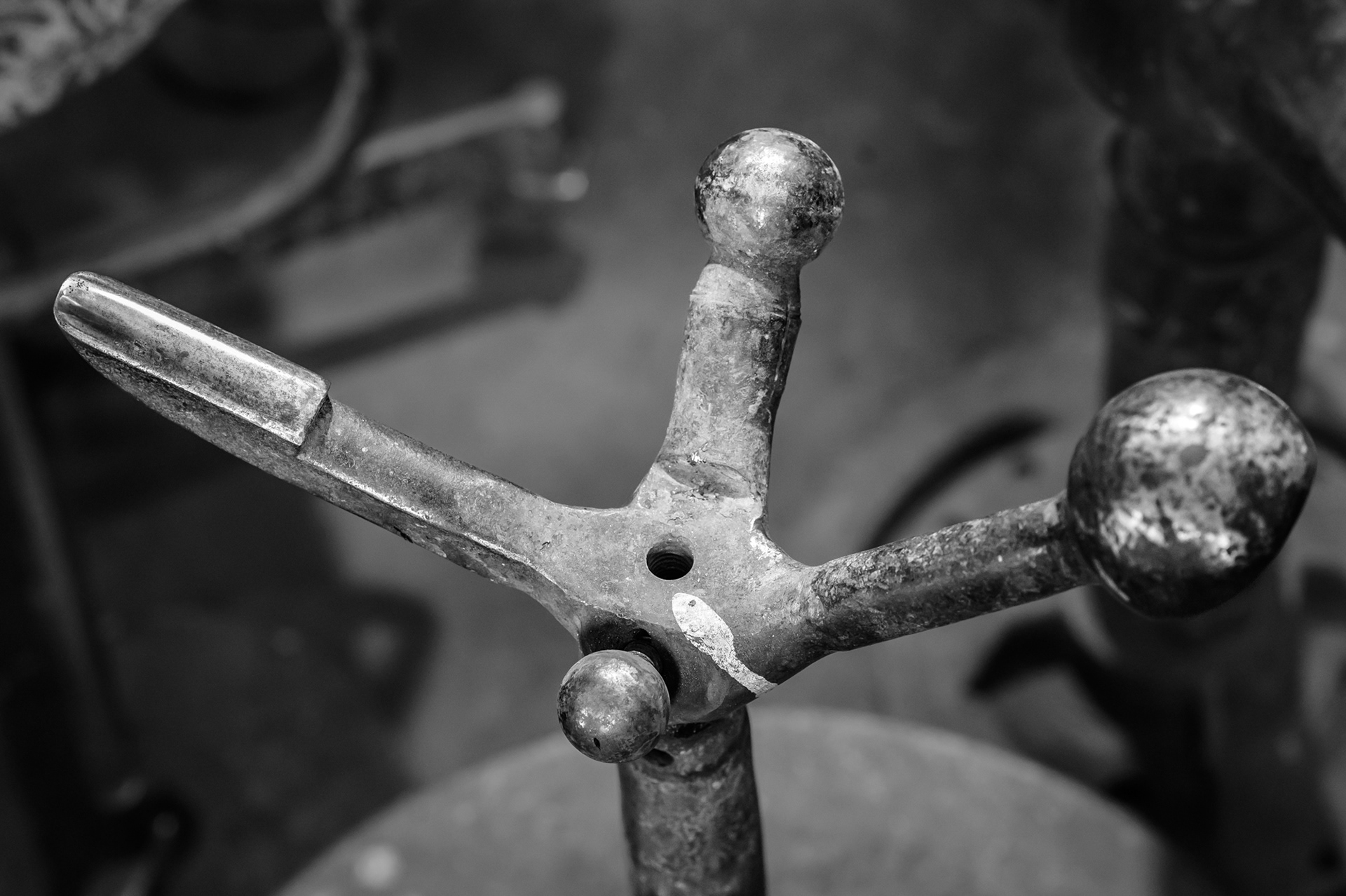
Custom made combined anvil with different profiles
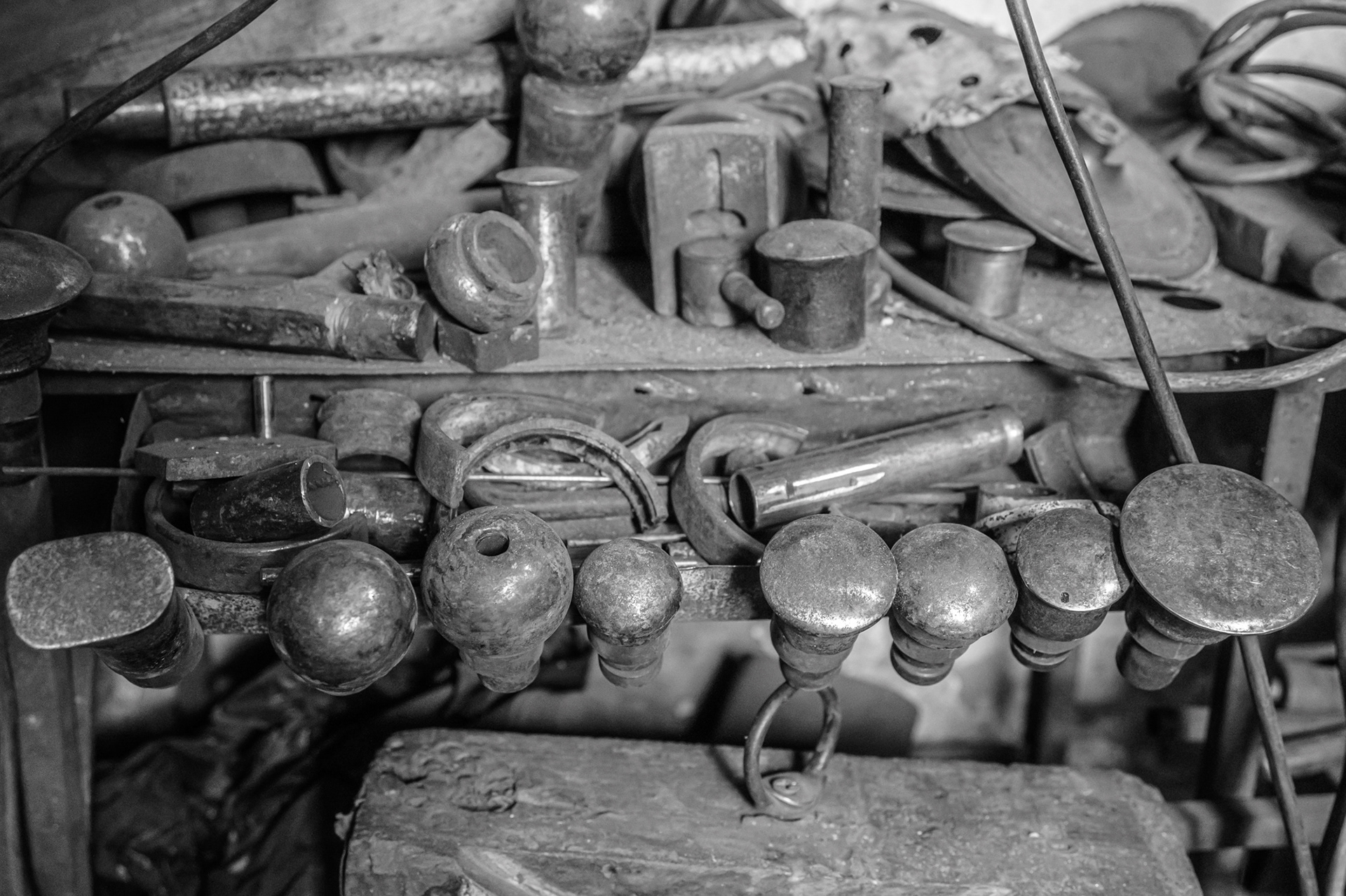
Tools for leveling the bottoms
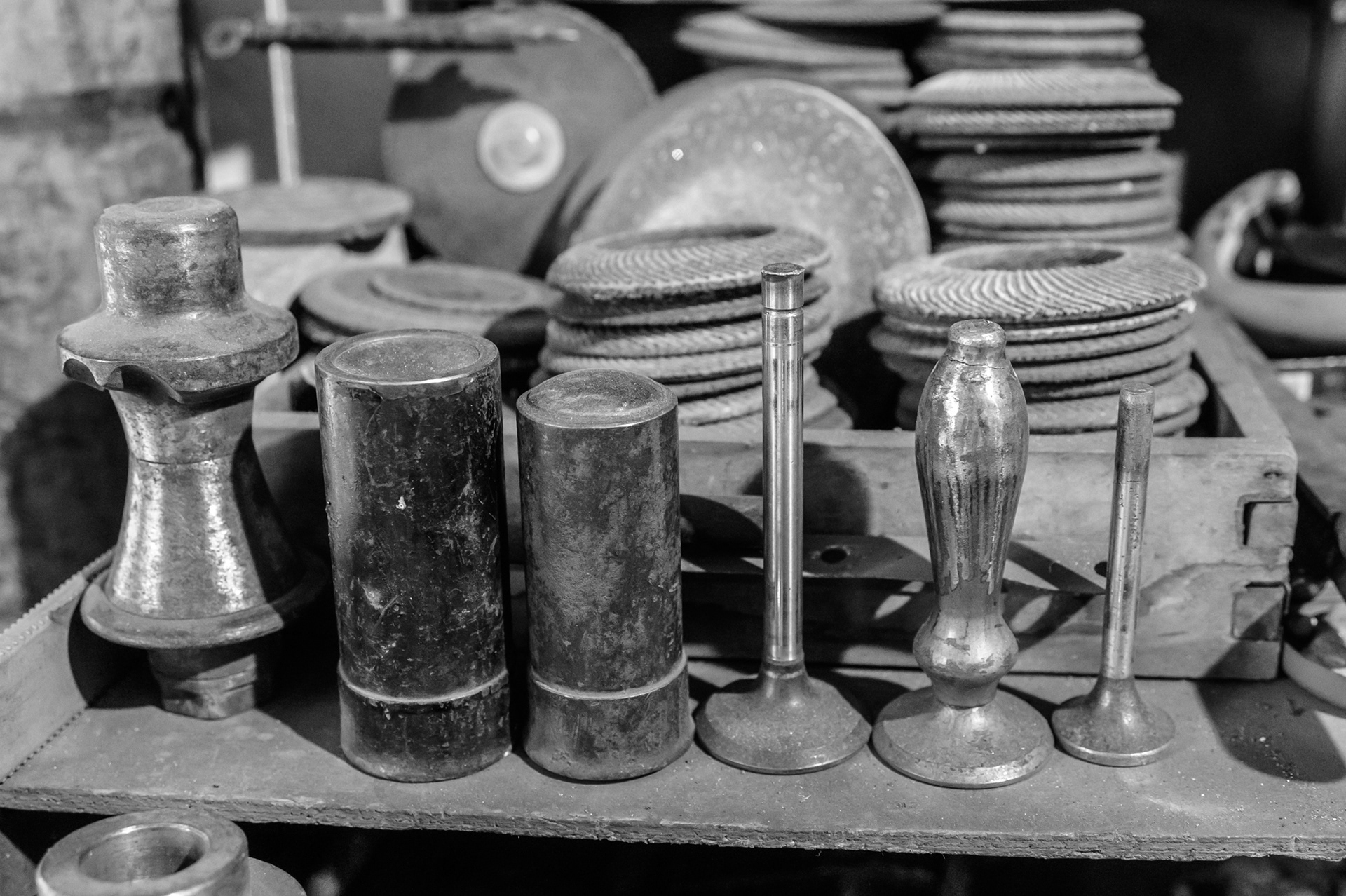
Modified or completely custom made by master Paunov tools to suit his personal needs in the craft
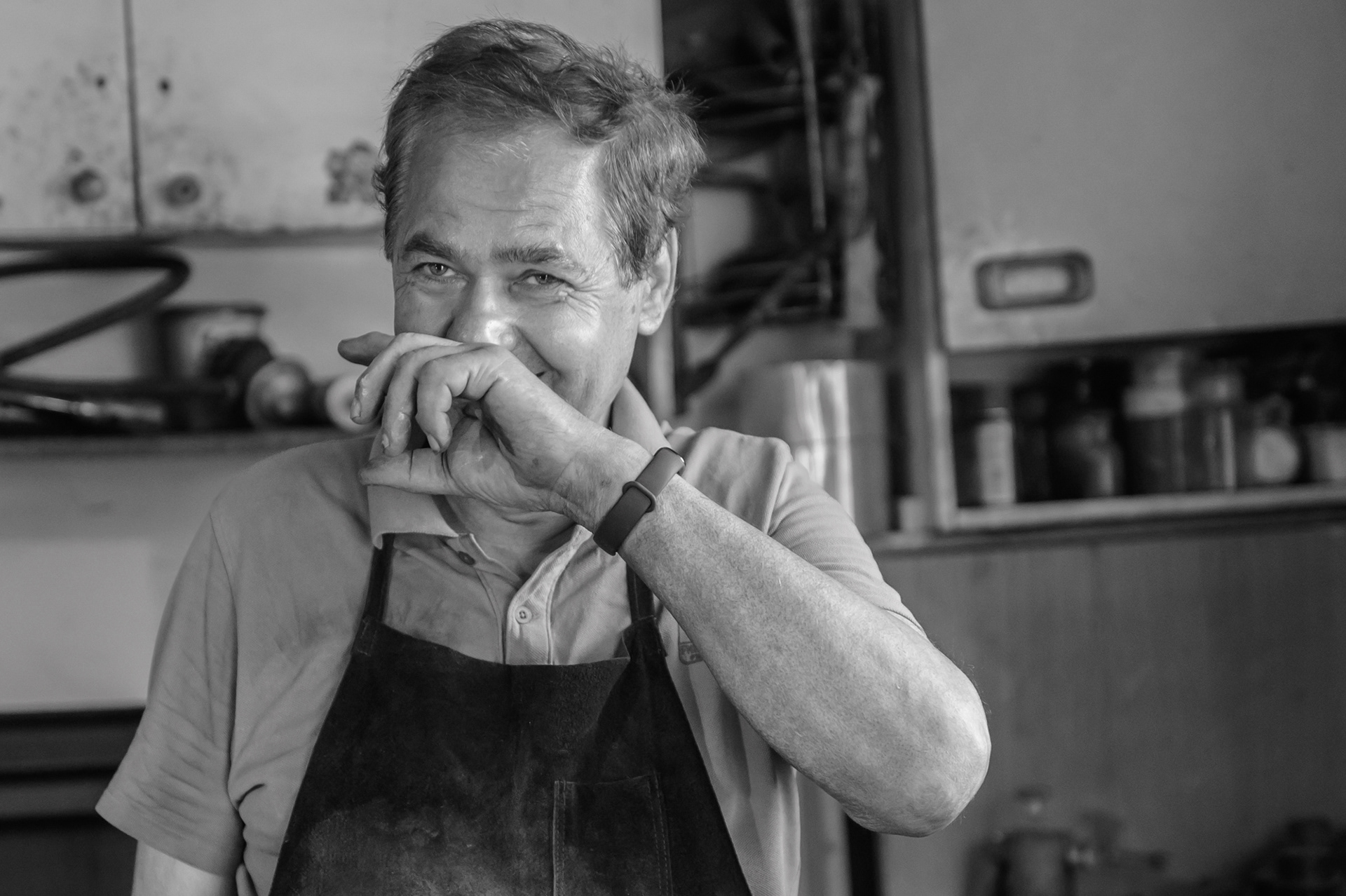
"Every morning I indulge in coffee fortune-telling – as a way to further develop my imagination"
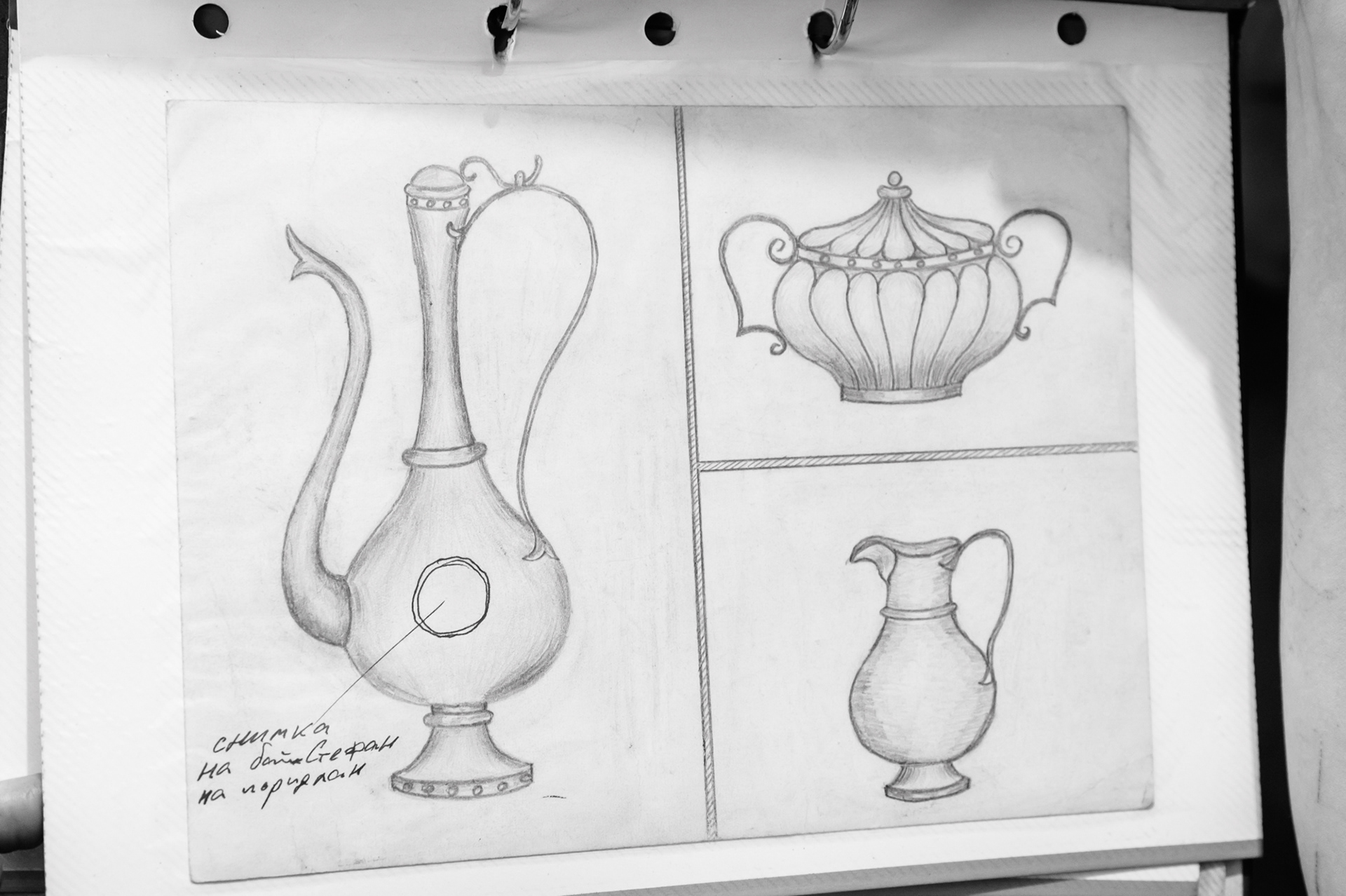
Sketches of the craftsman – preparatory stage for making copper vessels
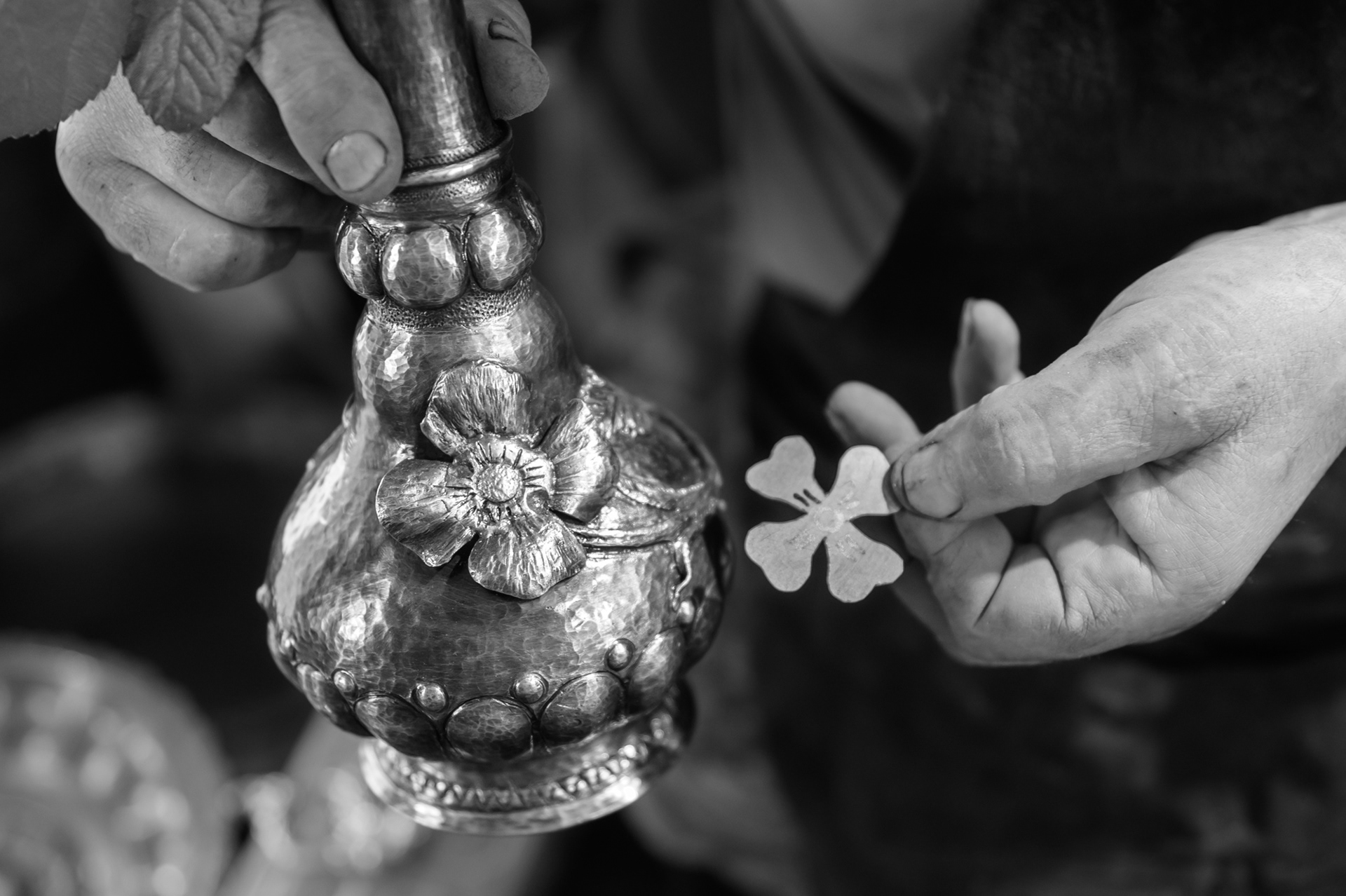
Comparison between a finished relief figure of a flower and its preparation state
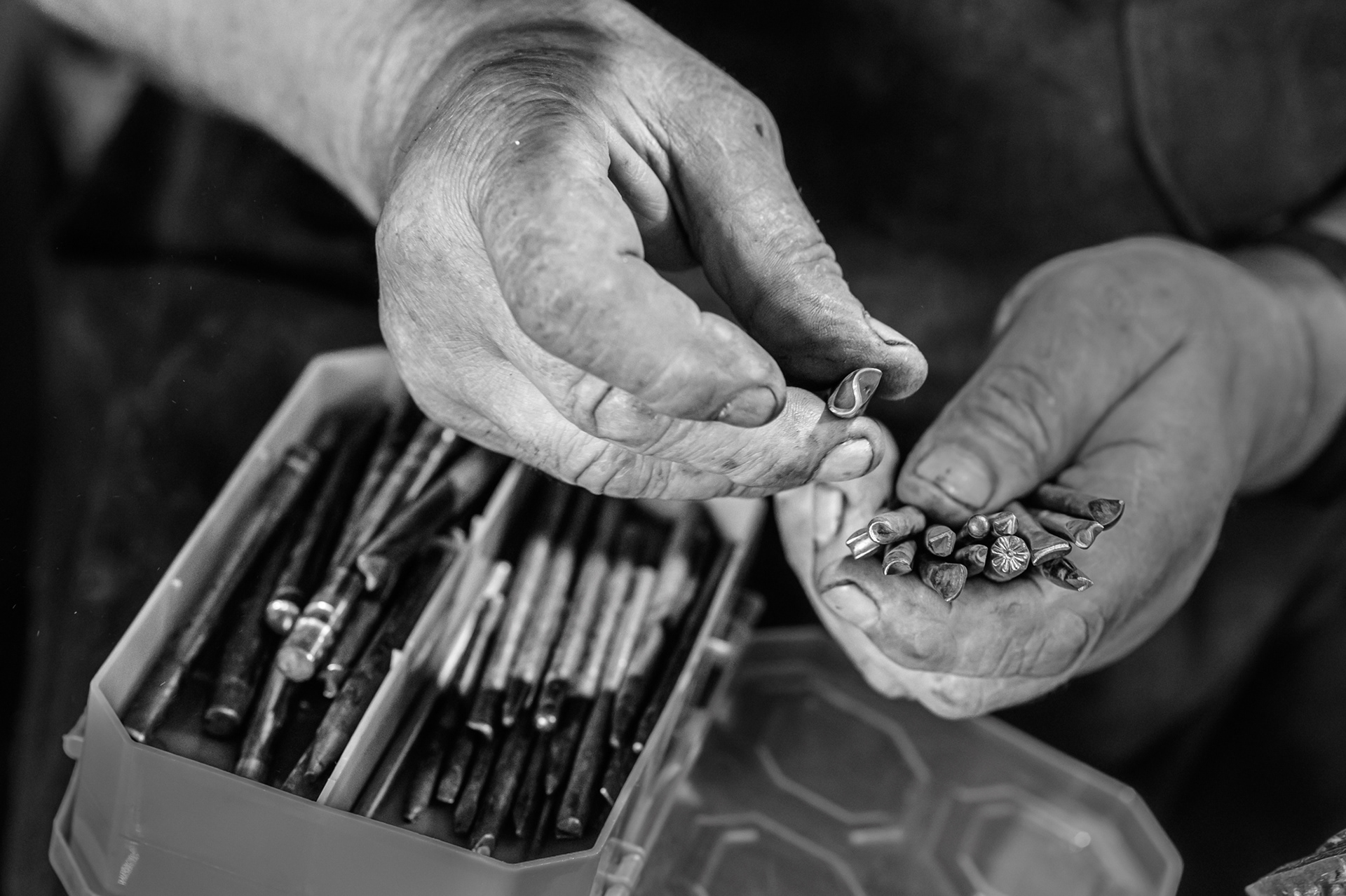
Embossing decoration tools or as the craftsman calls them – "chikanki"
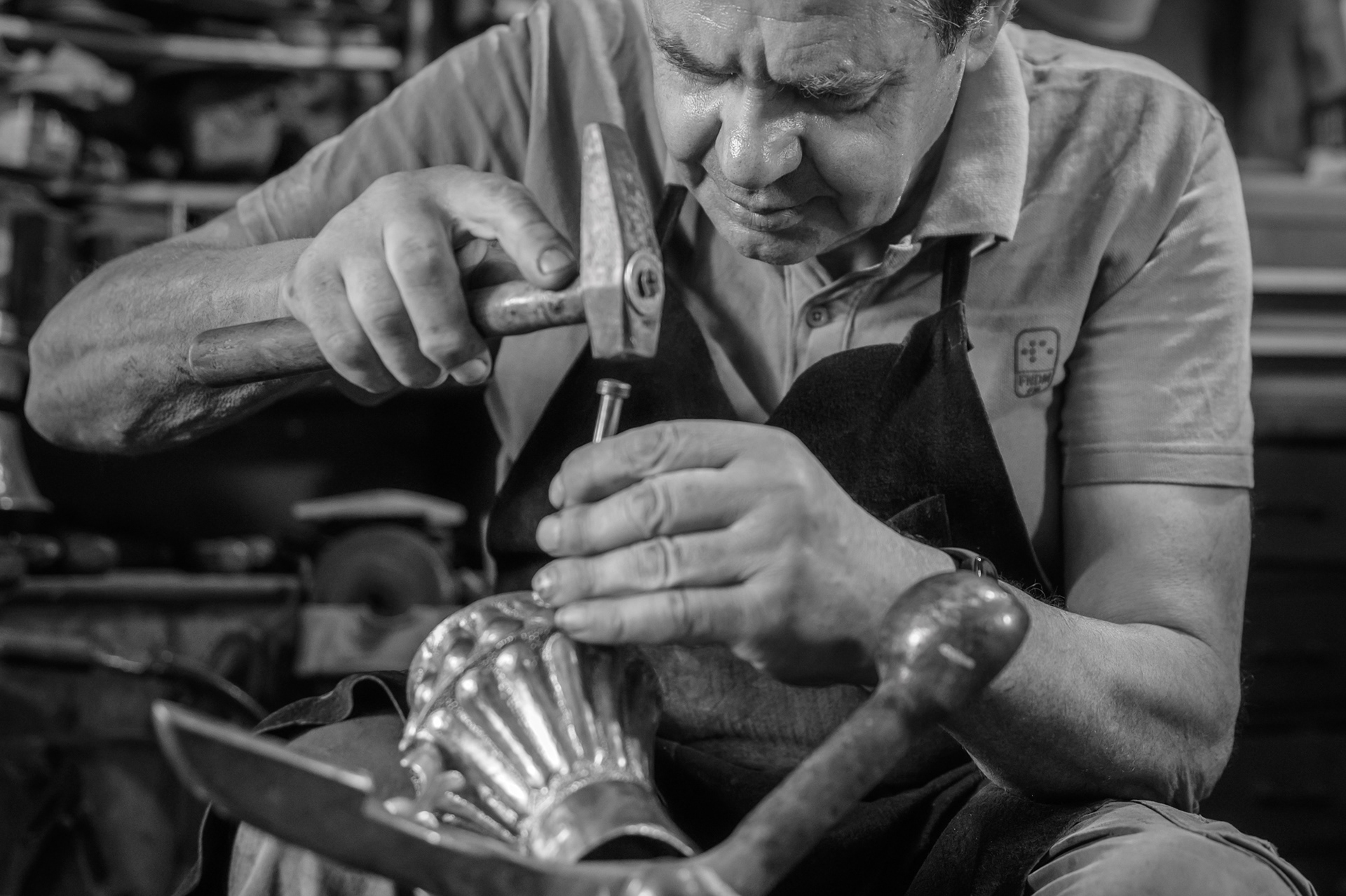
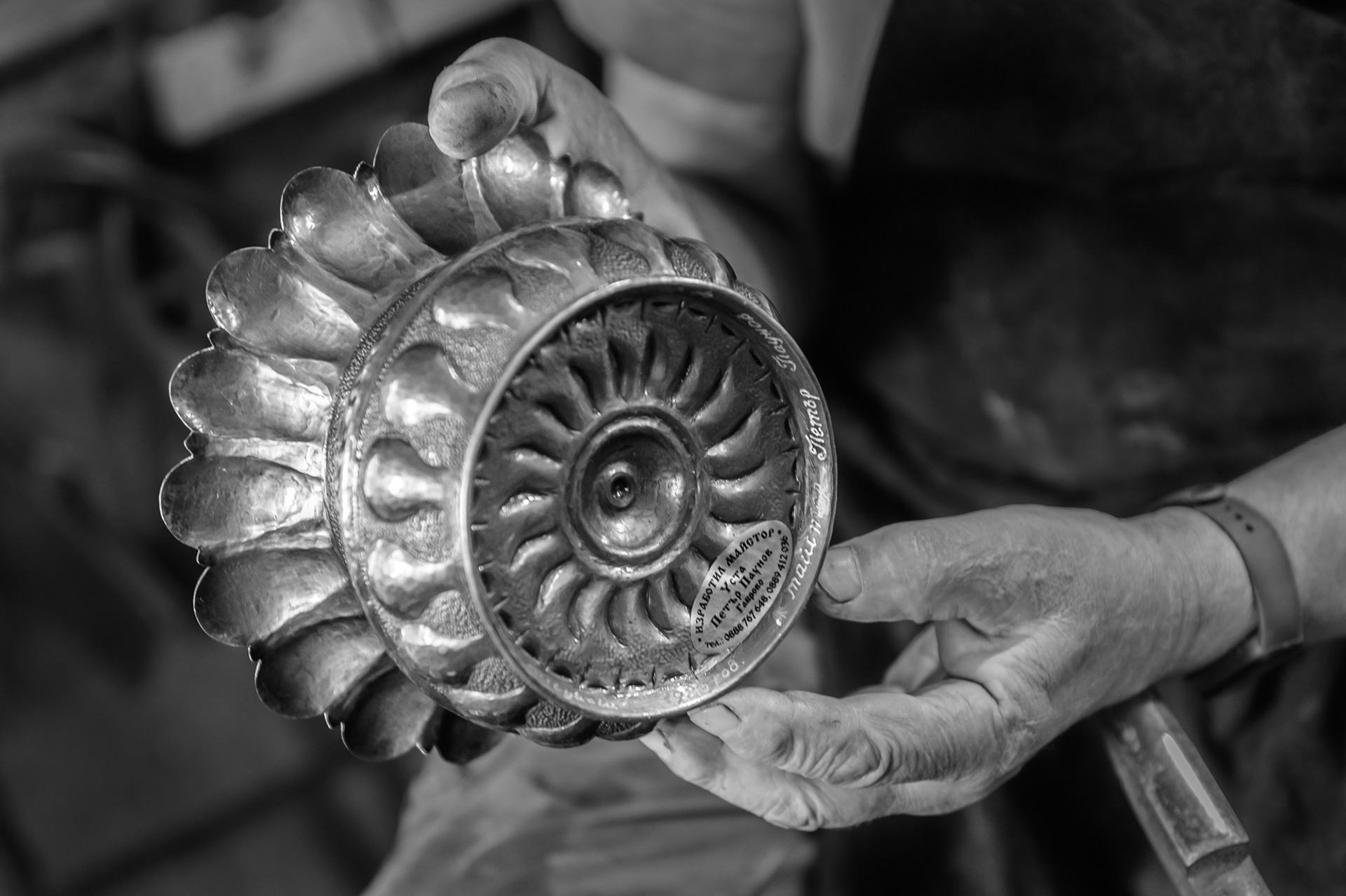
Pineapple type bowl made by bending and hammering a single sheet of copper (no cutting)
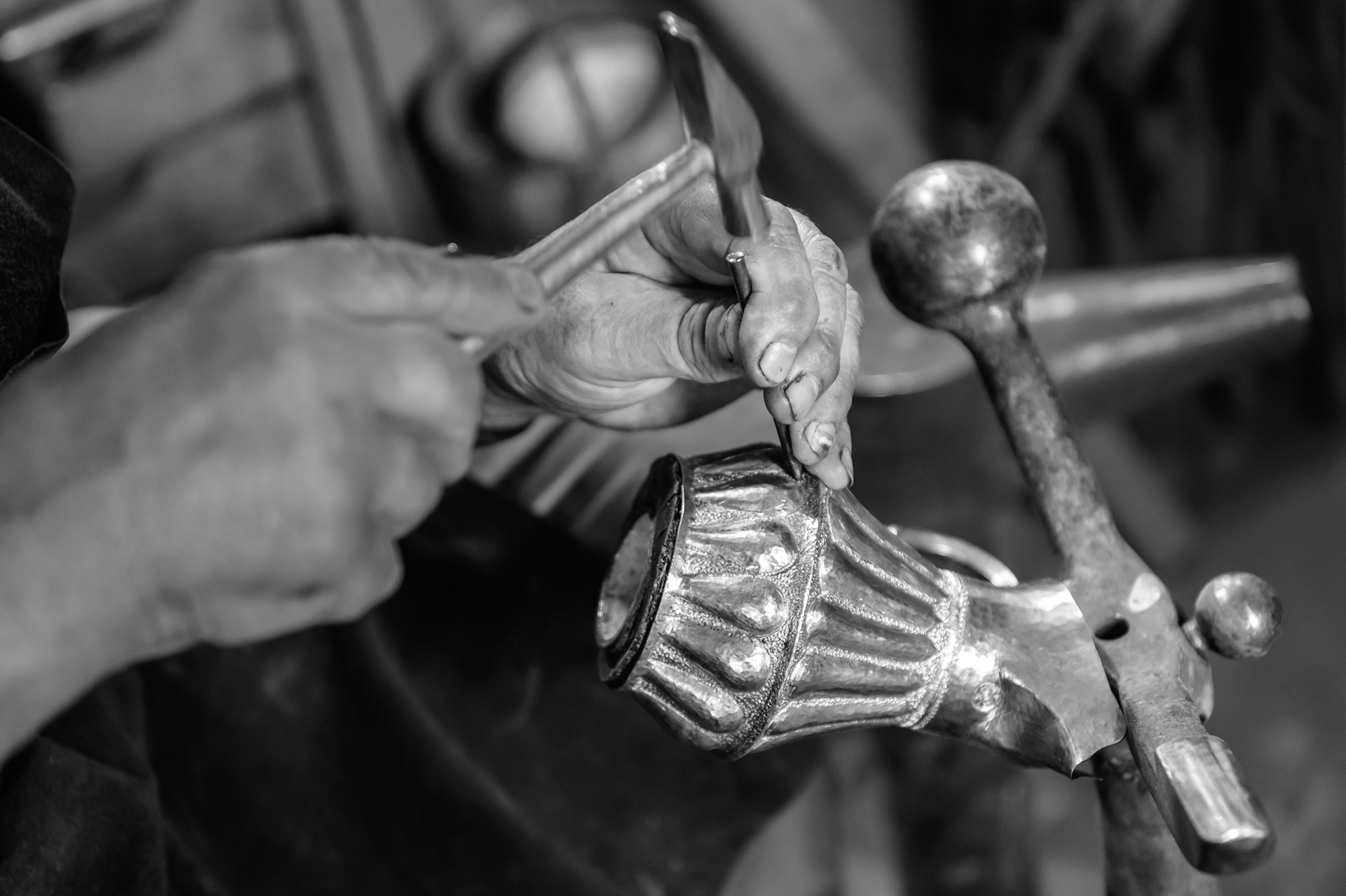
Hand relief hammering, a process of decorating a copper article
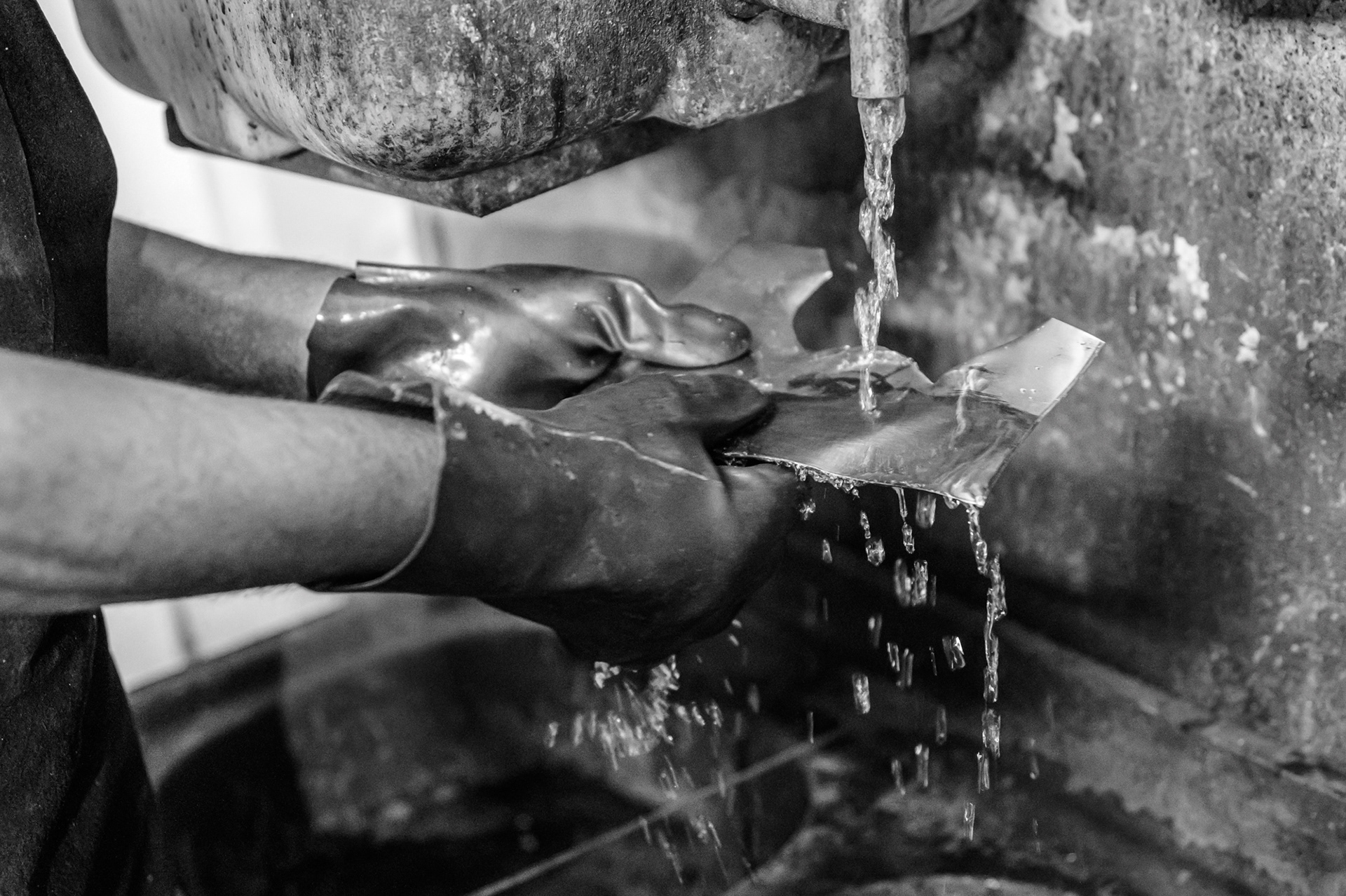
A stage of the process of patination – chemical aging and conservation of copper
Peter Paunov on continuity in the craft:
It is a streak of luck if you come across a good master to teach you.
My master had trained six craftsmen. I have trained fifteen, but only two of them continue practicing the craft.
While I was working for the sheikh in the Persian Gulf, I trained other Bulgarians. Two of them moved away to set up an independent workshop. I was happy to have competition, motivation and diversity.
My younger son, when he was just 6 years old, was already welding in the workshop. I have trained both my sons, but today they have other occupations.
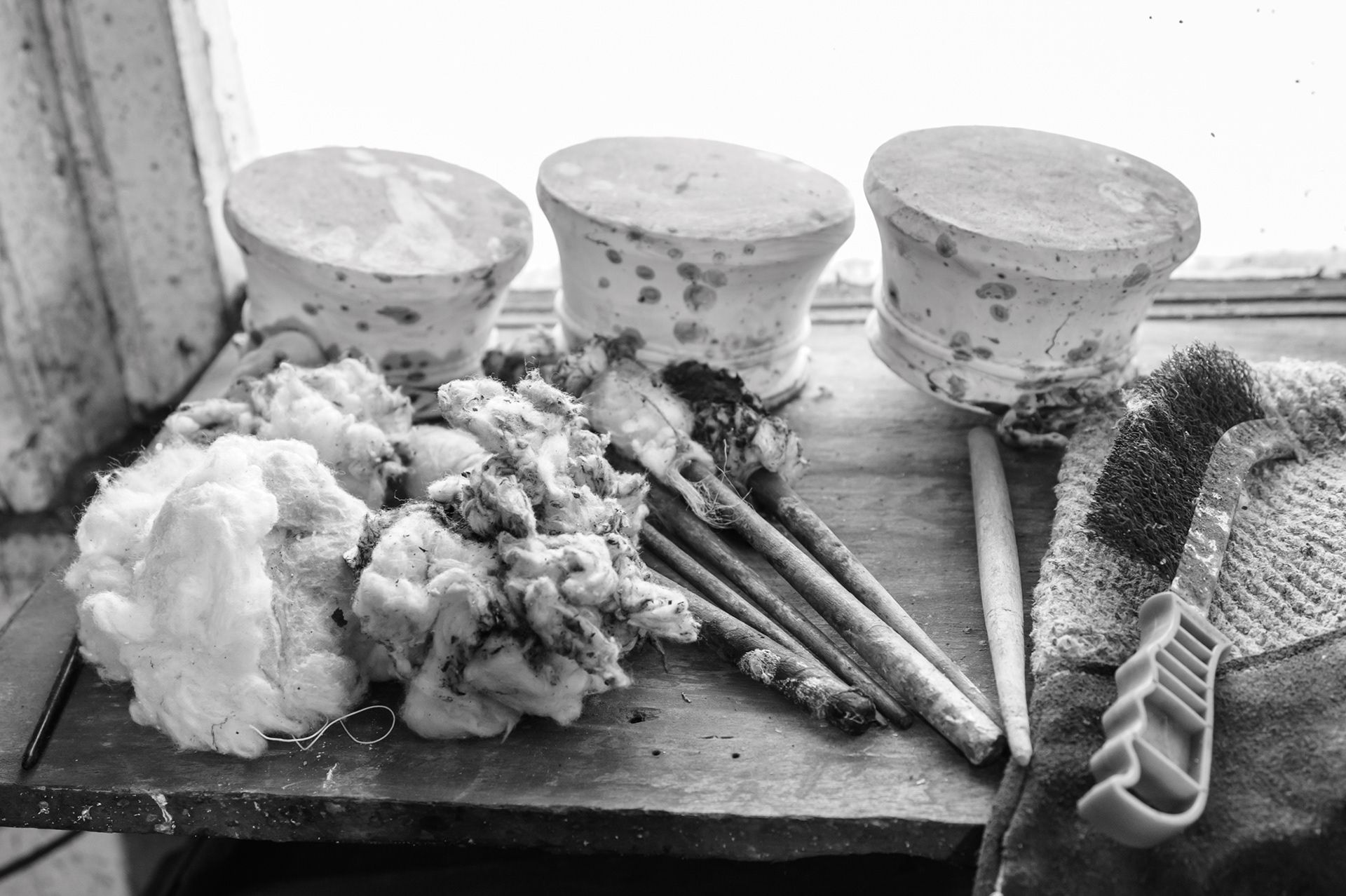
"Menchetta" (vessels) smeared with Wienerweiss (white limestone powder), cottons for spreading the tin and a wire brush for preliminary cleaning of the vessels – a stage of the tinning process. This procedure makes copper vessels suitable for food by preventing the release of harmful copper oxide.
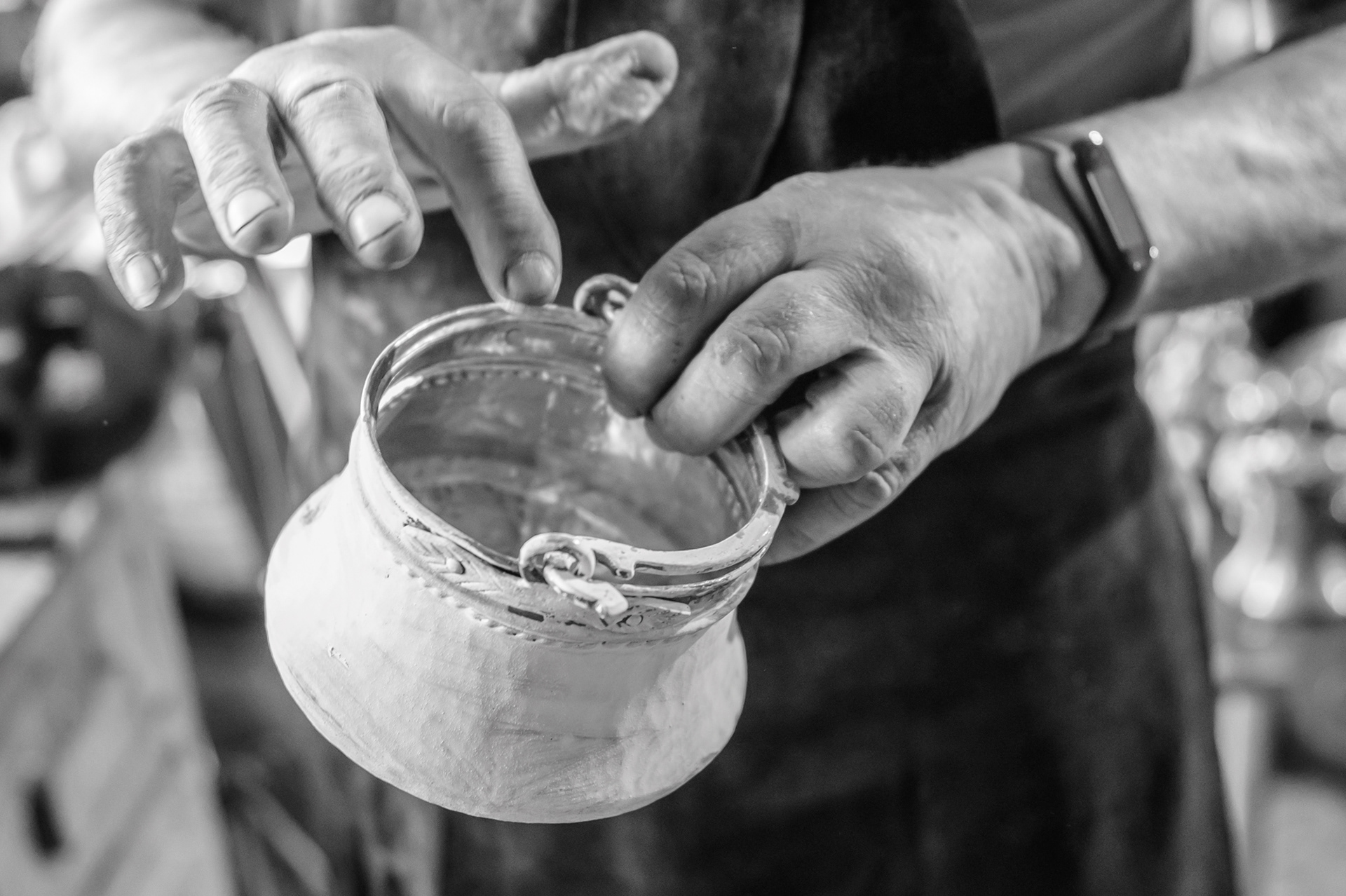
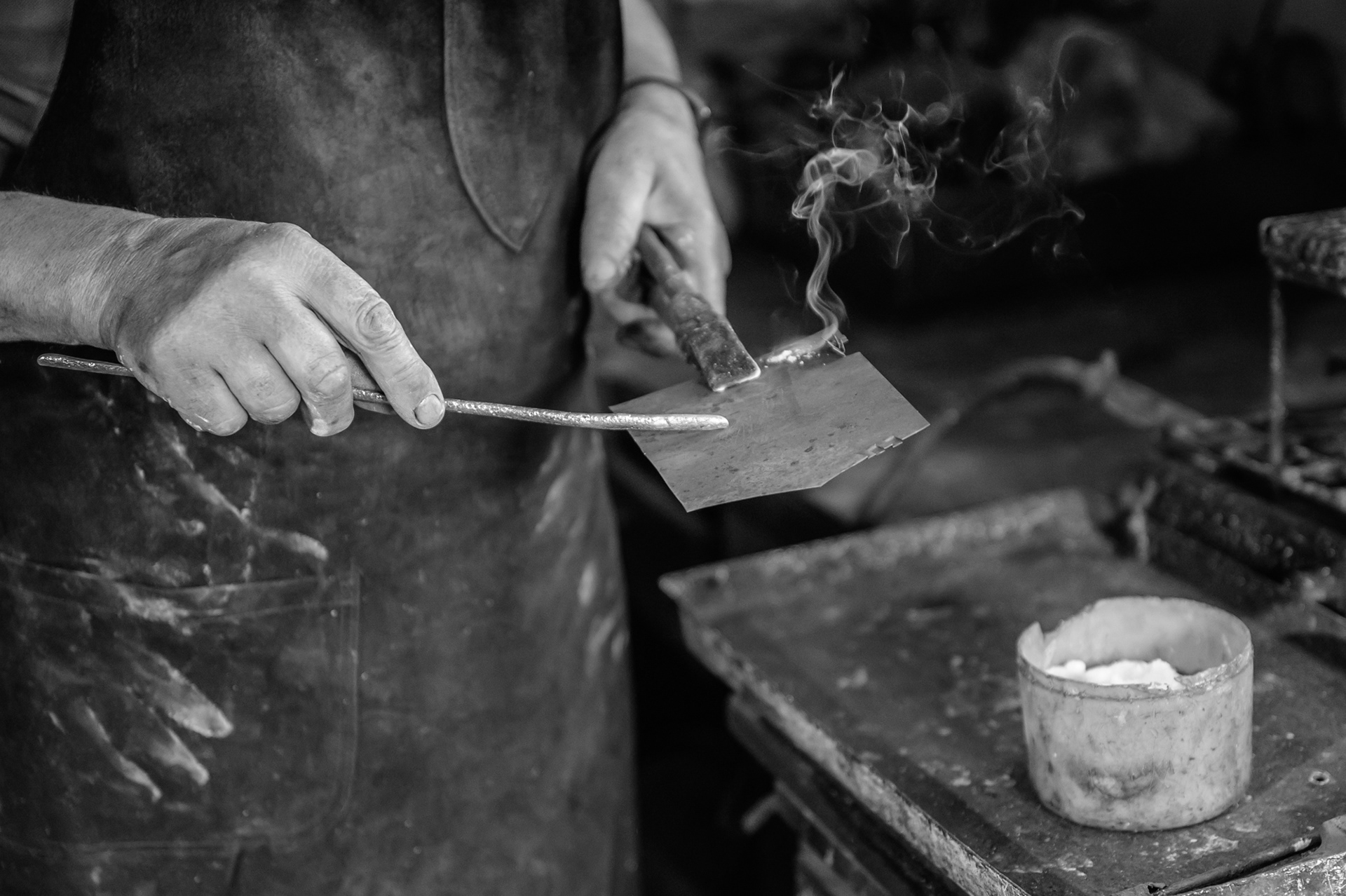
Applying tin (which is in the form of a rod) to a heated copper sheet. In a subsequent stage, it is spread evenly with the help of cotton.
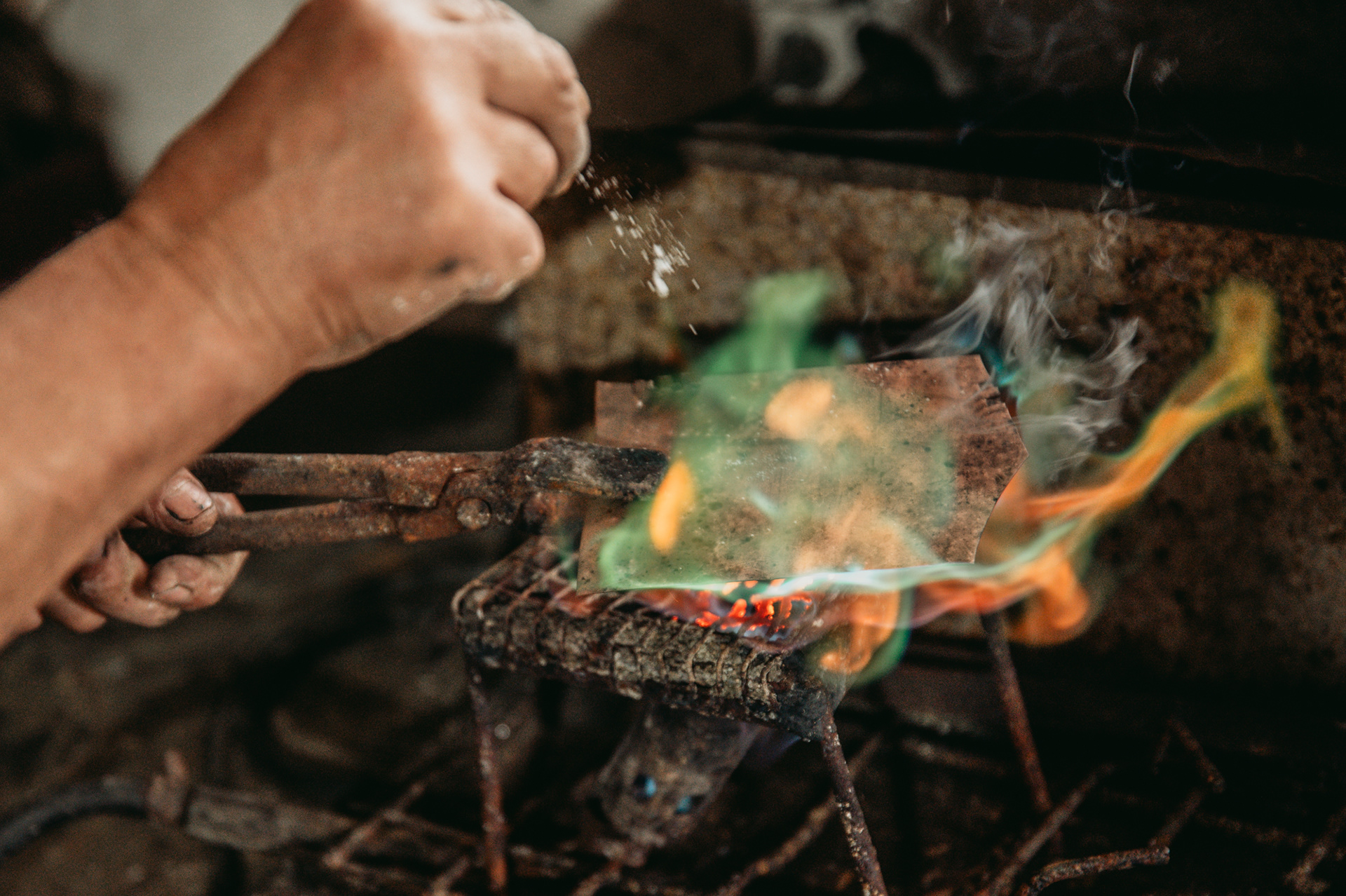
Chemical reaction – burning of copper oxide with a sprinkling of nitrite (ammonium chloride), stage of the tinning process
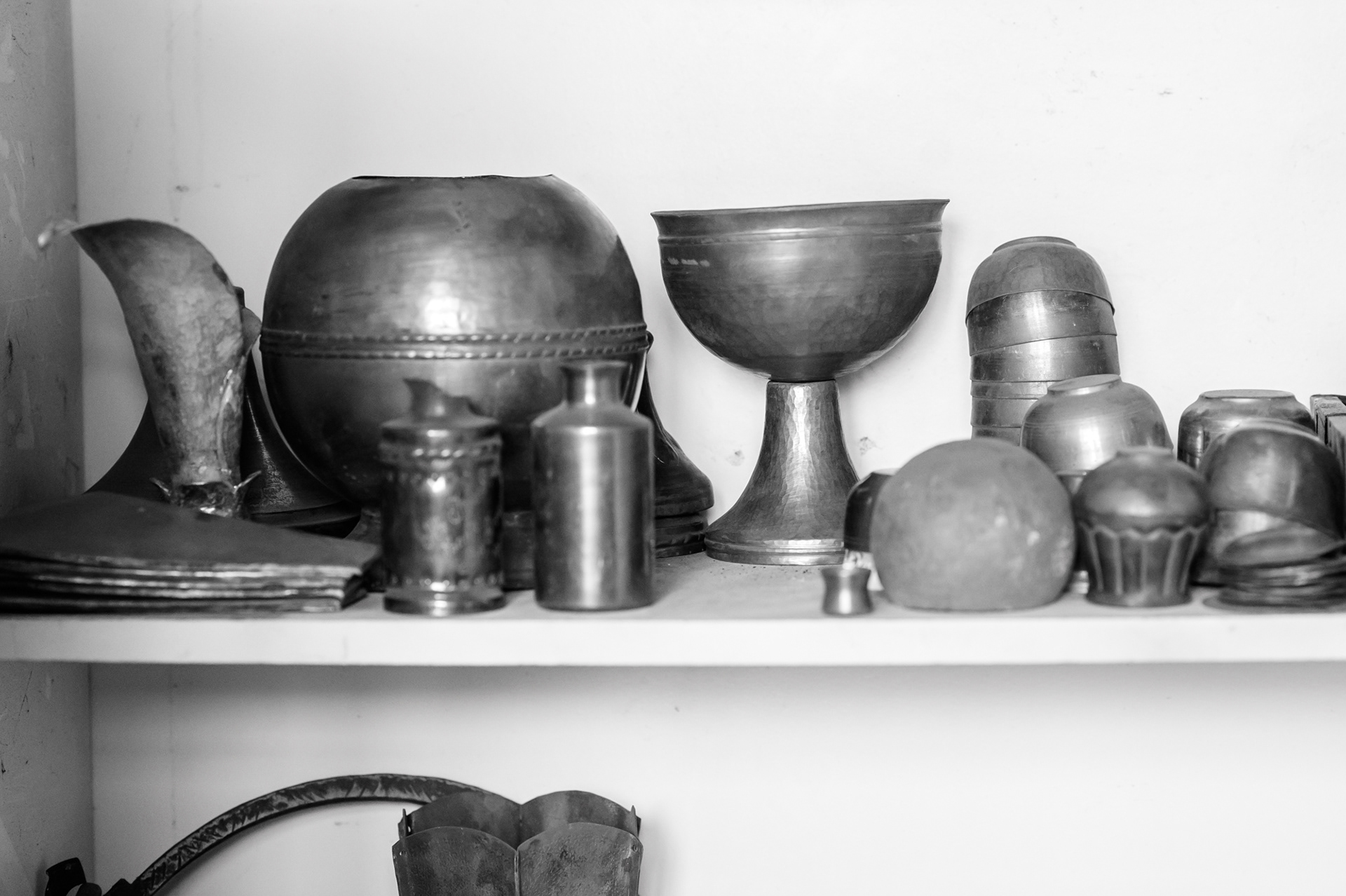
"Cabinet of reserves" – discarded products and preparations
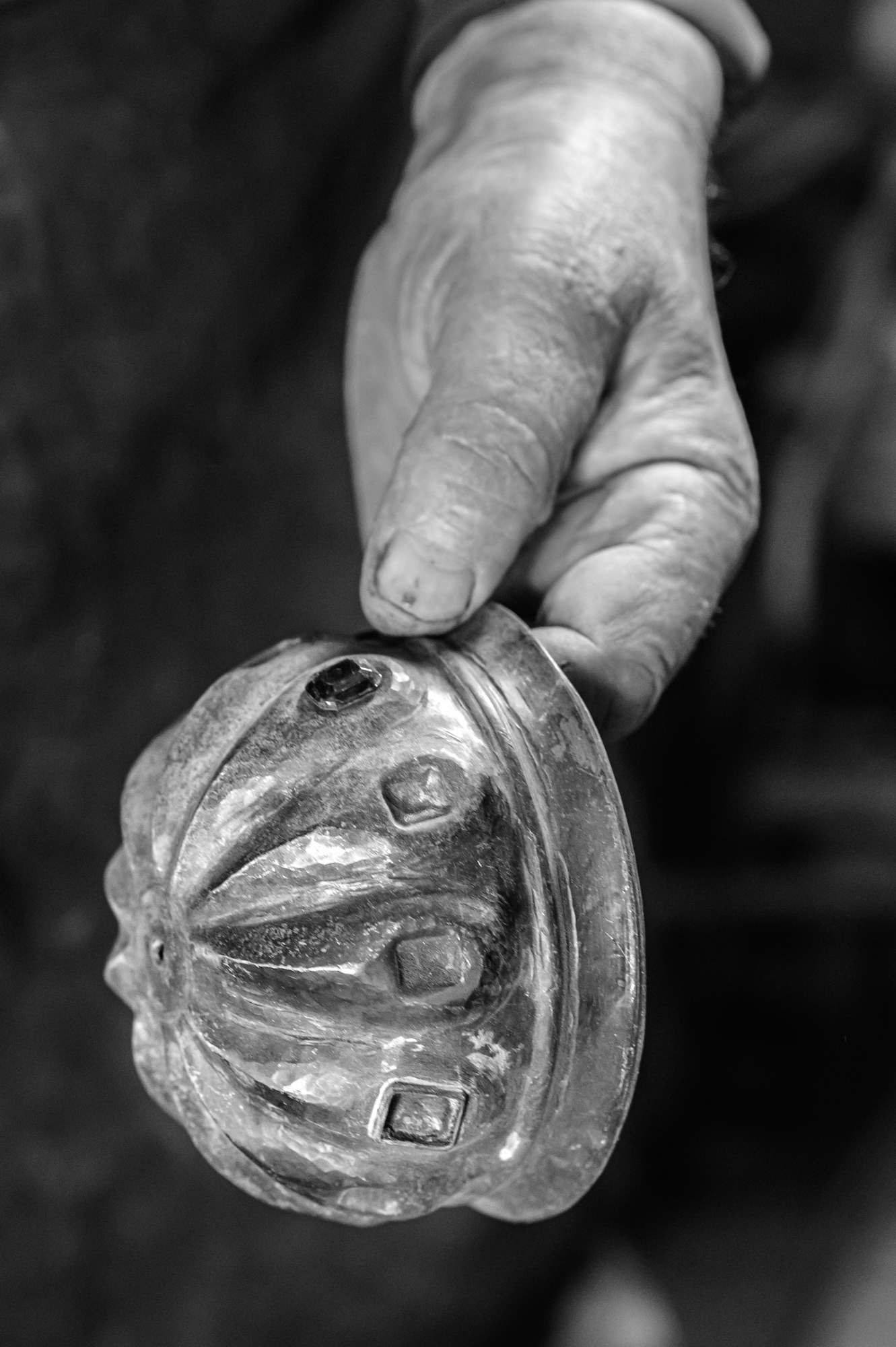
Upper part of a cup in preparation stage
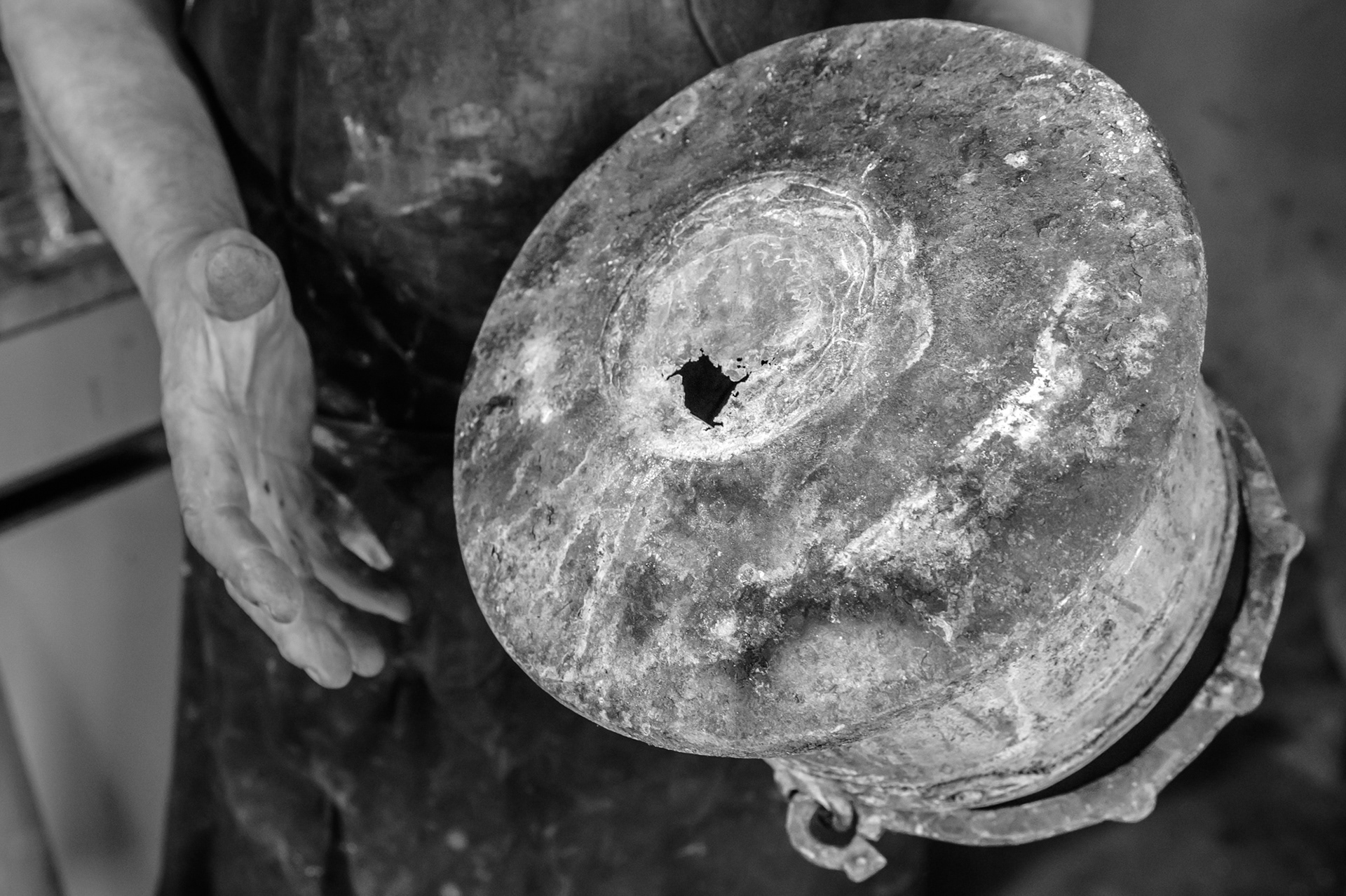
An old pot, worn out, made by Paunov in the 80s. Today it is back in his workshop – for repairs. The repair and restoration of dishes is a more complex activity than making new ones, therefore it is a sign of high mastery skills.
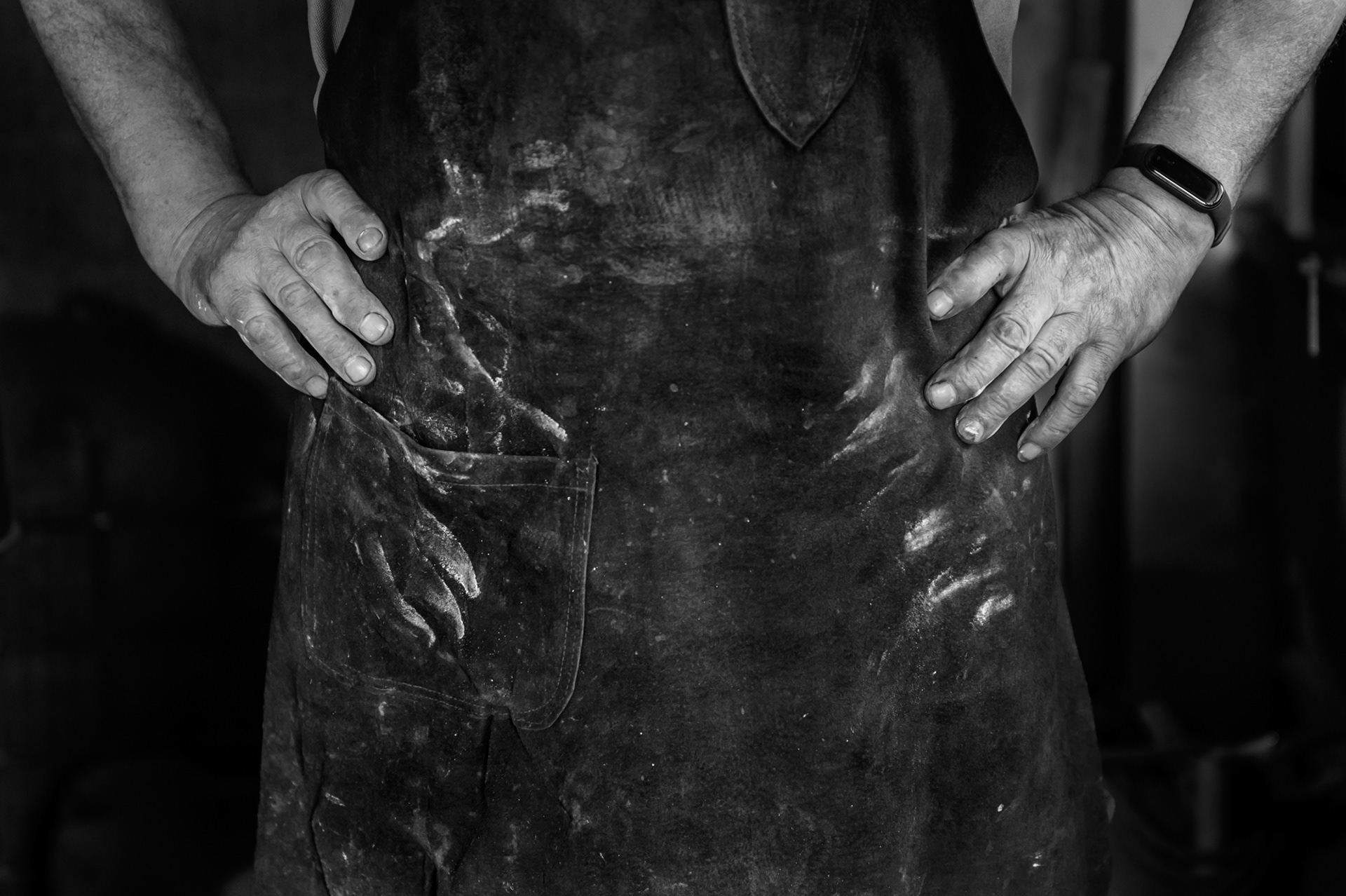
Explore additional material about Petar Paunov's story on the pages of Eight printed magazine. Out on December 8th 2022.
PROJECT
Crafted by Hand. Photo Diary (2022)
IDEA & PHOTOGRAPHY
Rosina Pencheva
TEXT
Maria Boncheva
CRAFTS CONSULTANCY
Rositsa Bineva
GRAPHIC DESIGN
Kostadin Kokalanov
TRANSLATION
Daniela Konstantinova
COMMUNICATIONS
Maya Ivanova
DIGITAL CONTENT
Rosina Pencheva
Denislava Dikova (assistant)
PRODUCTION
PARTNERSHIP
CO-FUNDING
2022 Culture Program, Gabrovo Municipality